HiLock
The HiLock realization type can be used for any more or less parallel combination of PSHELL and PCOMP elements, and creates a 1D element construct consisting of RBAR, CBAR and CBUSH elements.
The outer extensions represent the thicknesses of the outer shell elements. The inner nodes of the RBAR element are connected to the shell elements whereas the inner nodes of the CBAR elements are coincident to the shell nodes. Between the appropriate connected and coincident nodes CBUSH elements are created. Each outer node connects one CBAR and one RBAR.
Each HiLock connection gets its own coordinate system with the z-axis collinear to the HiLock direction. All affected nodes are assigned to this coordinate system, which is taken into account for the DOF definition of the CBAR elements, the stiffness calculation of the CBUSH elements, and the DOF of the node constraint.
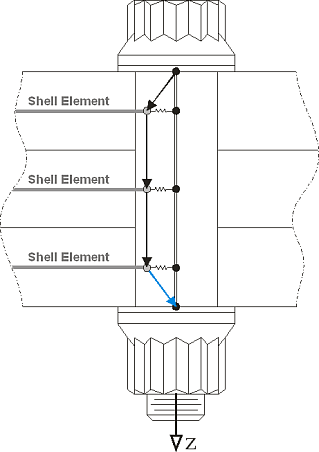
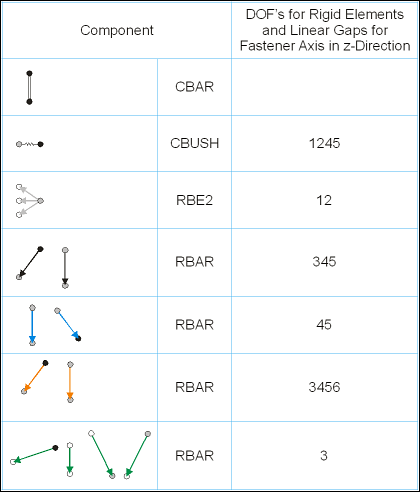
This realization also uses the prop_opt_nas_hilock.tcl property script.
Details and Requirements
- In the case of composites, only PCOMP cards in which the laminate option is either blank or set to SYM (symmetric) are supported. MEM, BEND, SMEAR, and SMCORE options are not supported for HiLock realization, and will cause realization to fail if used.
- The joined shells should be parallel to each other and planar.
- The fastener should be perpendicular to the shells.
- The z-axis of the element system, the material system, and the fastener system should be collinear.
- Stiffness is calculated assuming that the shells are perfectly planar and parallel. Small deviations will produce insignificant changes in predicted stiffness, but larger ones would require a system transformation.
- The shell elements which share a node with the HiLock (separate for each layer) should have the same properties, same materials, same material orientations, and similar sizes. The attributes of the element upon which the projection falls is assumed to be the same as the other surrounding elements (no averaging method is used.)
If attributes necessary for the stiffness calculation are missing, the connector fails and an error message displays in the status bar.
The realization requires available nodes near the connector position. If sufficient nodes are not available, the created elements are not collinear anymore and the HiLock gets a questionable geometry.
Organization and Definition of HiLock Realization
All HiLock elements (RBARs, CBARs, CBUSHs) created during the realization process are organized into a component named HiLock.
- HiLock_PBAR_<diameter>
- Created with the PBAR card associated with it. The RBAR elements reference this property. The attributes are calculated depending on the diameter specified in the Spot panel during realization.
- HiLock_PBUSH_<translational stiffness>_<rotational stiffness>
- Created with the PBUSH card associated with them. The CBUSH elements reference this property. The attributes are calculated depending on the chosen HiLock material and the properties and materials of the connected shells (PSHELL and/or PCOMP).
- HiLock_SPC6
- SPCs are created for each HiLock are moved into it.
- HiLock
- Systems created during the realizations will be moved into this collector. If this system collector already exists, any newly created systems will be moved into the same collector.
- HiLock_MAT1
- This material will be assigned to the PBAR cards, and can be found in the following folder of the installation directory: [hm_scripts_dir]/connectors/HiLock_Mats.
HiLock Material Option
When defining a HiLock connector, the HiLock Material Option can be selected for individual connectors using the Connector Entity Editor.
- From current model
- Select an existing material from the current model.
- From search folder (default)
- For HiLock realizations the material search folder is HiLock_Mats.
HyperMesh searches for this folder in
the following locations and in the following order:
- Installation: [hm_scripts_dir]/connectors/Hilock_Mats
- User directory: [USER_HOME]/HiLock_Mats
- HyperMesh Configuration Path folder: [HW_CONFIG_PATH]/Hilock_Mats
- Current working folder: [CURRENTWORKINGDIR]/HiLock_Mats
- From connector metadata
- Once a connector is realized with the HiLock Material Option “From Search Folder”, the folder and file name is written as metadata to the connector. Folder data is saved in a relative manner to allow the exact same rerealization in a different work environment as long as the materials are saved in according folders.
Calculation of Bearing Stiffness in Composite Parts
- Combined translational bearing stiffness at composite plate with the fastener contact
- These values are defined for every composite plate in the joint.
- Combined translational bearing stiffness of the joint at ply i location in directions x and y
-
Sixbt=1Cixbt=ti1¯Q(i)11+1EcfSiybt=1Ciybt=ti1¯Q(i)22+1Ecf
- Transformed reduced stiffness in x and y-direction for ply i
-
¯Q(i)11=Q(i)11m4i+2(Q(i)12+Q(i)66)m2in2i+Q(i)22n4i
Where,
¯Q(i)22=Q(i)11n4i+2(Q(i)12+Q(i)66)m2in2i+Q(i)22m4imi=cosθini=sinθi(theta = angle of orientation for ply i)
- Nonzero components of the reduced stiffness matrix for ply i
-
- Angle of ply i orientation in a CQUAD4 element
-
Figure 5. - Material orientation of a CQUAD4 defined by a coordinate system
-
Figure 6. - Rotational bearing stiffness in plate-fastener contact
-
Figure 7.
Calculation of Bearing Stiffness in Metallic Parts
- Combined translational bearing stiffness at metallic plate with the fastener contact
- After summation of bearing stiffness of plies where n = number of plies
in the composite plate:Sxbt=Sybt=t1−v2E+1EcfWhere,
- t
- Thickness of metallic part
- E
- Elastic compression modulus of metallic (isotropic) part
- v
- Poisson's ratio
- Rotational bearing stiffness at metallic plate with the fastener contact
- Sxbr=Sybr=112·t31−v2E+1EcfWhere,
- t
- Thickness of metallic part
- E
- Elastic compression modulus of metallic (isotropic) part
- v
- Poisson's ratio