Rear Linked Solid Axle
The rear linked solid axle is a dependent suspension (the wheels are connected via a solid beam) which is commonly found in off-road vehicles, SUVs, and rear wheel drive vehicles. This suspension is known for its simplicity and low cost. A differential is included when it is a driven axle. Including the track bar (which is used to restrain the lateral movement of the axle) will make this an asymmetric suspension.

- The wheel is connected to the wheel hub with a fixed joint.
- The wheel hub is connected to the axle with a revolute joint.
- The axle is connected to the lower and upper links with bushings.
- The upper links and lower links are connected to a sub frame or the chassis with two bushings.
- One end of the track bar is connected to the axle with a bushing, while the other end is connected to the vehicle body with another bushing.
- All links are modeled as rigid bodies.
- This suspension is asymmetric due to the track bar anchor locations.
Model Use
- The wheel body represents the mass and inertia of the tire and the rim.
- The wheel hub is used to represent the mass of the wheel hub and any other components that rotate with the hub, such as a brake rotor. There are no graphic entities for the wheel hub.
- The front and rear bushings for the respective links are defined such that they aligned parallel to each other.
- The Center of Gravity (CG) of the parts is estimated from the geometry. The formulas are coded into the Point panel and can be seen via the graphical user interface. If exact CG locations are available, they should be entered as X, Y, Z coordinates instead of the estimated number.
- Both the wheel and wheel hub parts use the wheel CG location as the center of gravity.
- When the suspension is built as a kinematic suspension, the track bar is removed since it would over constrain the axle. The bushings on the links are replaced with joints.
- A wide variety of combinations of suspensions and subsystems can be built using the
Assembly Wizard. You are encouraged to build systems and
understand the resulting model using the graphical user interface.
When building a new suspension model, build the model with all of the optional systems (stabilizer bar, etc) included in the model. Immediately turn off the systems using the Project Browser and run an analysis on the base suspension to ensure it solves properly. As data becomes available for the optional systems; activate those systems and populate them with data.
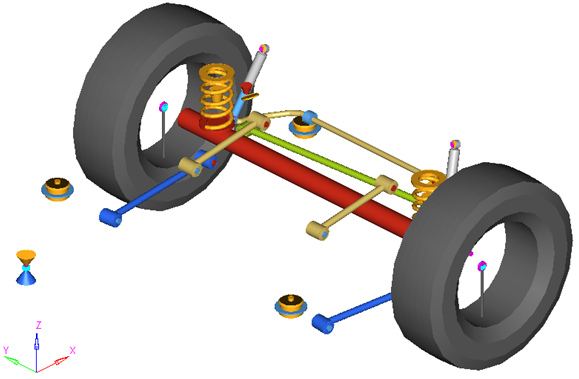
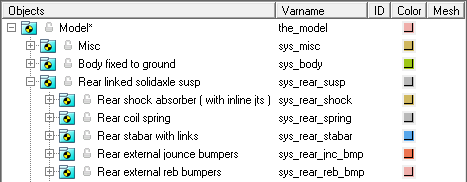
Connections
- The spring connects to the axle and the vehicle body.
- The upper and lower link frame bushings connect to the vehicle body, unless an optional subframe is selected. When the subframe is included, the frame bushings connect to the subframe.
- The jounce and rebound bumpers connect to the shock absorber piston and body when internal jounce bumper and internal rebound bumper are selected.
- The jounce bumper attaches to the vehicle body and axle when external jounce bumper is selected.
- The rebound bumper attaches to the vehicle body and axle when external rebound bumper is selected.
- A differential is included in the model when a drivetrain is selected in the Assembly Wizard.
Points
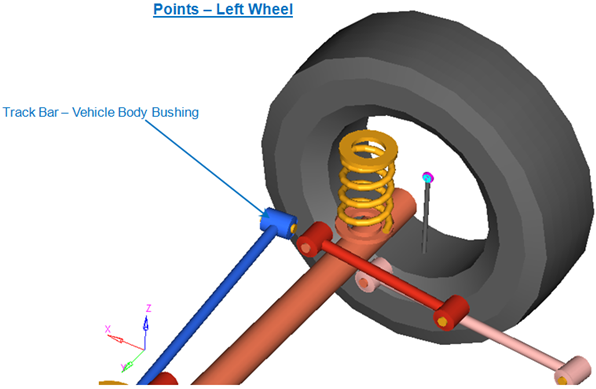
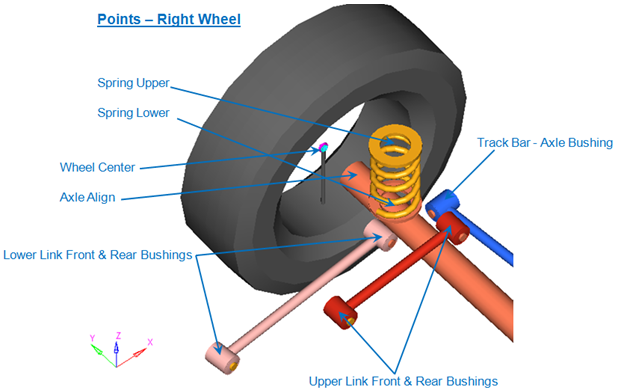
Bodies
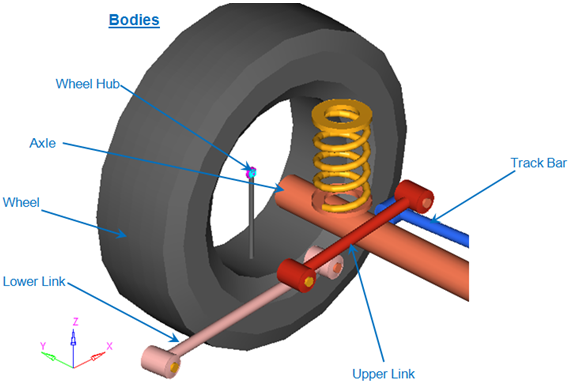
Bushings and Joints
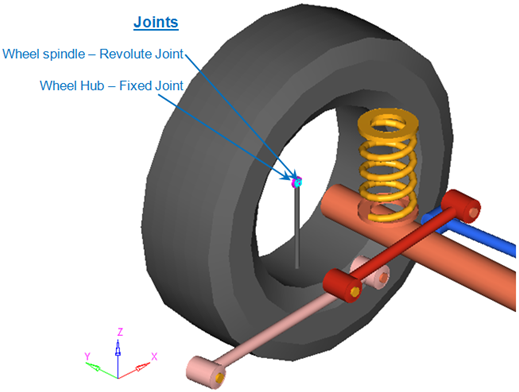
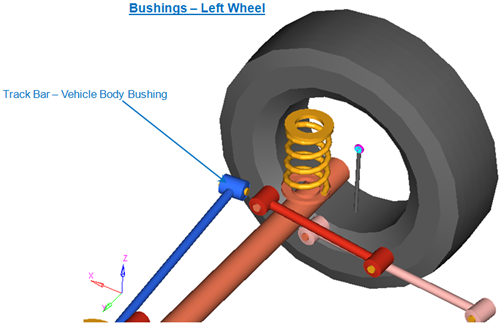
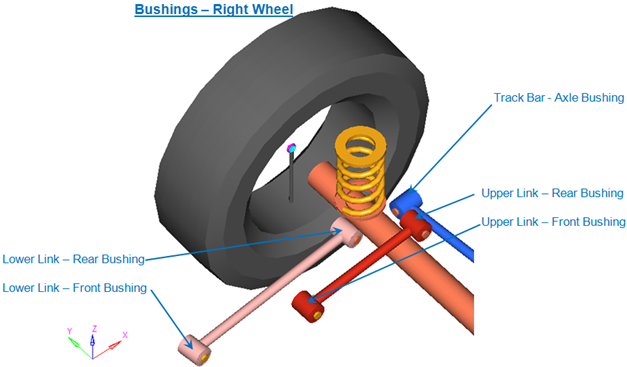
External Files
The jounce bumper curve data and the rebound bumper curve data files are stored in the vehicle library and are referred to by this model. A new file should be created and substituted for these files when actual data is available.
Similar Suspensions
Rear Twist Beam
Rear Solid Axle w/Leafspring