Single Motor Electric Powertrain
Architecture
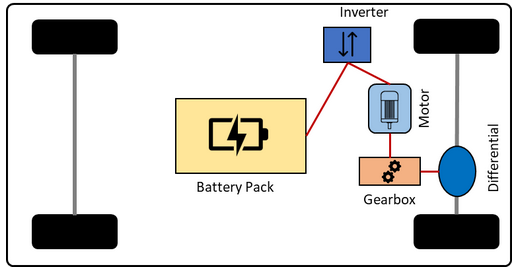
Powertrain Architecture in Twin Activate
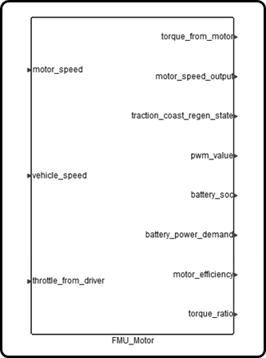

- Permanent Magnet Synchronous Motor
- A comprehensive model of the Permanent Magnet Synchronous Motor (PMSM) is
established based on its speed-torque characteristics and efficiency data. This
information is derived from an external efficiency map file
(.efmp), which contains the torque-speed and
torque-speed-efficiency characteristic curves of the motor. The data is explicitly
obtained through Look-up Tables in the form of .mat files
containing the appropriate variables. This approach allows for the incorporation of
user-defined electric motor data in vehicle simulations and ensures accurate
calculation of power consumption.The Torque-Speed characteristic curve is particularly significant as it delineates the torque boundaries for both the motor's tractive (positive) and regenerative braking (negative) regions, as shown in the figure below. These boundaries illustrate the maximum positive and negative torque that the motor can generate at corresponding speeds. The PMSM motor's characteristics encompass two distinct regions: a constant torque region and a constant power region. The motor can deliver its maximum torque up to its rated speed, and beyond that point, it can supply its maximum power.
Figure 4. Torque-Speed Characteristic Curve The Torque-Speed-Efficiency curve, also known as efficiency map, is responsible for providing the efficiency values for each motor depending on its operating region. It also contains information for the motor’s traction and regenerative braking region as shown in the figure below.Figure 5. Torque-Speed-Efficiency Characteristic Curve - Voltage-Current Controller
- The Voltage-Current controller block is used to control the AC supplied to the
motor. The control voltage depends on the vehicle speed, motor speed, accelerator
pedal input and battery state of charge. To determine the appropriate voltage to apply
to the motor, the controller employs Pulse Width Modulation (PWM) and references
Torque lookup tables. Additionally, the voltage is subject to constraints imposed by
the battery's state of charge (SOC). Notably, when the battery SOC exceeds 80%, the
controller prohibits regenerative braking to safeguard the integrity of the battery
cells, as such braking can potentially inflict damage. Conversely, if the battery SOC
falls below 20%, the battery ceases to supply current, again as a protective measure
for the battery cells.A PWM Look Up table is used to calculate the PWM value using vehicle speed and accelerator pedal input. The PWM value ranges from 0 to 250. The value 50 is used for coasting, that is, at this value the motor will output 0 torque. If the PWM value is less than 50 the motor acts as a generator and is in regenerative mode. A PWM value greater than 50 means the motor is providing positive torque for traction. The coasting region consists of two distinct boundaries, as illustrated in the figure below.
Figure 6. Upper and Lower coasting boundaries vs different vehicle velocities for throttle pedal mapping In the figure above, the region above pcu, is the tractive region and the region below the lower boundary (pcl) is the regenerative region. The coasting band between these boundaries increases with vehicle speed. This expansion is a deliberate design choice aimed at reducing the sensitivity of the accelerator pedal at higher vehicle speeds.
The regenerative torque in the powertrain can be used to brake the vehicle in normal traffic conditions. The motor provides enough negative torque to operate the vehicle with only one pedal in case of city drives 1. At higher vehicle velocities, the regenerative torque alone is not sufficient to stop the vehicle and hence the friction braking should be used. The regenerative torque percentage in this model changes with vehicle velocity as shown in the figure below.Figure 7. Regenerative Torque percentage of motor’s available torque vs vehicle speed To achieve a standstill condition in the case of a fully released accelerator pedal, the regenerative torque is set to 0 at 0 vehicle speed. This is done by setting the value of the first cell in PWM lookup table to 50 which means coasting.
This way, the coasting region and the regenerative torque percentage are directly used to determine the motor’s torque ratio, which is the percentage of motor’s torque utilization and is indited by the following equation:
trm=TmΤmmax(ω)
where:- Tm : motor’s torque
- Τmmax(ω) : motor’s maximum torque as a function of speed
The torque ratio can receive values in the range of [-100, 100], where positive values depict motor operation in tractive mode and negative values regenerative braking mode.
- Inverter/Converter
- The inverter/converter blocks are responsible for modeling the power losses resulting from the frequency conversion process executed by the motor control. It stands in between the motor and the battery pack and provides the final power demand of each motor.
- Battery Pack
- The Battery model receives as input the combined power demand from both motors. It
contains the required information to determine the capacity of the battery pack. It
specifies the charging/discharging losses from the vehicle operation, to estimate the
battery’s state of charge.Note: The complete Twin Activate diagram of the powertrain model can be accessed from: <install_dir>\ hwdesktop\hw\mdl\mdllib\Common\FMU_Library\Motor\FMU_source\Activate_Models.
Powertrain Model in MotionView
In the MotionView MDL system, the motor, inverter, and battery are represented as rigid bodies including their mass and inertia properties, which are a significant portion of BEV’s total mass and inertia. A force under Gearbox system represents the driving torque attached to the driveshaft. Two Solver variables connect the FMU channels to the Altair Driver. Datasets contain crucial information on motor body’s properties. Moreover, each motor’s bushings are provided, that define the positions where the motors are based. Finally, the Altair Driver uses a Feedback Controller for speed and acceleration control.

- Datasets
-
- Motor Properties
-
The real time motor efficiency calculation relies on real motor torque-speed-efficiency data provided by an external efficiency map file (.efmp). This file is a representation of the motors’ Torque-Speed and Torque-Speed-Efficiency characteristic curves. The path pointing to this file is received as input in the Motor Properties Dataset.
- Template
-
- Evaluate Motor Properties
- It is responsible for the initialization of an internal script
(MotorProperties.py) before every simulation, used to:
- Read the Teimorbit format .efmp file.
- Extract motor properties.
- Generate .mat files specific to the .xml file and store them in the run folder.
- Assign the correct .mat file paths/variables in the FMU parameters section.
- Solver Variables
-
Entities Type Description Comments FMU Torque Solver Variable Rear/ Front motor output torques N-mm FMU Omega Solver Variable Rear/ Front motor output wheel velocities rad/s Battery SOC Solver Variable Battery’s State-Of-Charge 0 - 1 Torque Ratio Solver Variable Rear/Front motor speed torque utilization 0-100 Vehicle Longitudinal Velocity m/s Solver Variable Vehicle’s longitudinal velocity m/s Driver Throttle Output Attachment solver variable Throttle signal from driver 0-1 Driver Clutch Output Attachment solver variable Clutch signal from driver Not used in the model but required by the driver’s attachment Driver Gear Output Attachment solver variable Gear signal from driver Not used in the model but required by the driver’s attachment - FMU Entity
- Represents the FMU of the Single Motor Electric Powertrain with inputs, outputs,
parameters, and solver settings. The inputs of the FMU powertrain can be customized
and you are free to change the system, however some inputs and outputs need to be
present to correctly simulate a driver event. The tables show the necessary inputs and
outputs of the FMU powertrain block. The powertrain receives throttle, transmission
input shaft speed, vehicle speed and outputs torque.
- FMU Inputs
-
Connections Description Units Comments Motor speed Gearbox input shaft speed rad/s Vehicle speed Vehicle’s longitudinal velocity m/s Unit conversion required from MV’s mm/s to FMU’s m/s Throttle from driver The accelerator pedal’s input from driver 0-100 Unit conversion required from MV’s 0-1 to FMU’s 0-100 - FMU Outputs
-
Connections Description Units Comments Torque from motor Motor’s output torque N-m Unit conversion required from FMU’s N-m to MV’s N-mm Motor speed output Motor’s shaft speed rad/s Traction Coast Regen State Integer value that shows the operating mode of motor: -1 indicates that powertrain is in regenerative braking mode, 0 means it is operating in coasting band and a value of 1 indicates that the motor is operating in tractive region -1, 0, 1 PWM value It corresponds to the pulse width modulation value which can be converted to voltage applied to the motor 0-250 Battery SOC The state of charge of the battery 0 - 1 Battery power demand Battery power demand from motor Watt Motor efficiency Motor’s efficiency 0 - 1 Torque ratio Motor’s torque ratio 0 - 100 - FMU Parameters
-
Parameters Description Units max_pwm Maximum PWM value pwm_zero_torque PWM value corresponding to 0 torque output matfilename Warning: This parameter is automatically updated, it should not be manually modified.Refers to the motor .mat file’s full path. It appears multiple times in the FMU. matvarname Warning: This parameter is automatically updated, it should not be manually modified.Refers to the .mat file’s variable name, used for data extraction. It appears multiple times in the FMU. pedal_0_regen_percent 1-4 These parameters define the percentage of regenerative braking contribution to total braking as a function of velocity. Specifically, you can specify the regenerative braking percentage to determine the three sections of Figure 7. pedal_0_vx 1-4 These parameters specify the corresponding velocities at specific regenerative braking percentages. Specifically, they are used to define the velocity values that designate the three sections of Figure 7. traction_max Percentage of maximum available torque N-m traction_gamma Polynomial degree to define the correlation between throttle and torque ratio for the traction region max_pedal Maximum throttle value 0-100 regen_psi Order of polynomial to define the correlation between throttle and torque ratio for the regenerative region coast_ch Range of coasting to define pcl and pcu values coast_phi At what pedal value coasting is desired coast_m Polynomial degree to determine coasting region max_vehicle_speed Vehicle’s maximum velocity m/sec battery_discharging_losses Coefficient to determine battery discharging losses while at tractive region SOC_initial Initial State-Of-Charge level (%) num_modules_pack_series Number of module packs rows num_cells_per_module_series Number of cell rows per module nominal_voltage_cell Cell’s nominal voltage V battery_charging_losses Coefficient to determine battery charging losses while at recuperation region capacity_cell Cell’s capacity Amp-hours num_cells_per_module_parallel Number of cells per module in parallel num_modules_pack_parallel Number of module packs in parallel SOC_limit_high Upper limit for SOC SOC_limit_low Lower limit for SOC Path char Warning: This parameter is automatically updated, it should not be manually modified.Mat file path that contains motor characteristics, such as rated and maximum speed, rated torque emotor_efficiency_scale Parameter to enable efficiency scaling inverter_efficiency Inverter’s efficiency value converter_efficiency Converter’s efficiency value
- Motor System
- Includes the integrated motor-inverter unit.
- Bodies
- Motor/Engine - Represents the lumped mass and inertia of each motor in a non-operating condition. The motor’s output shaft is assumed to be hard coupled with gearbox input shaft and hence their speed is going to be the same. The motor’s shaft and its rotation are not modeled. Since the inertia of the rotating shaft is not modeled, this inertia can be added in other rotating elements in the driveline.
- Motor Mounts
- Motors are attached to chassis by four bushings. The mount locations must be provided on the attachment body by specifying the coordinates of the mounts and the orientation of the bushings specified using the vectors corresponding to each mount.
- Solver Variables
-
Entities Type Description Comments FMU Torque Solver Variable Motor output torque from FMU N-mm FMU Omega Solver Variable Motor output wheel velocity from FMU rad/s Throttle input to motor 100 Solver Variable Throttle input from driver 0-100 FMU Power demand motor Solver Variable Motor power output W Traction/Coast/Regen state Solver Variable Integer value that shows the operating mode of motor: -1 indicates that powertrain is in regenerative braking mode, 0 means it is operating in coasting band and a value of 1 indicates that the motor is operating in tractive region -1, 0, 1 PWM value Solver Variable It corresponds to the pulse width modulation value which can be converted to voltage applied to the rear motor 0-250 Motor Efficiency Solver Variable Motor’s efficiency 0-1
- Gearbox System
-
- Bodies
- Gearbox – Contains the mass and inertia properties of gearbox body in a non-operating condition. Gearbox is also assumed to be directly attached to the motor body, with the usage of a fixed joint. The motor’s output shaft is assumed to be hard coupled with gearbox input shaft and hence their speed is going to be the same.
- Datasets
-
- Gear Box Data
-
Label Description Final Drive Ratio Differential’s final stage of gear reduction ratio, used to calculate the final drive torque. Gearbox Efficiency Gearbox’s overall efficiency, used to calculate the final drive torque.
- Solver Variables
-
Entities Type Description Comments Torque from Gear Box Solver Variable Mathematical expression used to calculate gearbox’s final output torque. N-mm Gear Box Input Shaft Speed Solver Variable Mathematical expression used to calculate gearbox’s input shaft speed. rad/s - Forces
- Gearbox Output Torque - Represents the powertrain’s output torque on the differential’s carrier body. The torque is calculated by the ‘Torque from Gear Box’ Solver Variable expression.
- Battery Pack System
- If the battery pack module has been selected from the Assembly Wizard, it can be
found as a separate system, out of the primary Dual Motor Powertrain system. It includes:
- Bodies
- Battery Pack - Represents body's mass and inertia properties.
- Battery Mounts
- Battery is attached to chassis by four bushings. The mount locations must be provided on the attachment body by specifying the coordinates of the mounts and the orientation of the bushings specified using the vectors corresponding to each mount.
Access the Electric Powertrain for Full Vehicle Models
- The Vehicle Tools extension must be loaded.
- From the menu bar, select .
- Load the Vehicle Tools extension by sliding the Load button to the right.The Vehicle tools page is add in MotionView.
Figure 9.
- In the Vehicle Tools ribbon, click the Assembly tool to open the Assembly Wizard.
- Select the Full Vehicle with Driver model and click
Next.
Figure 10. Select Model Type - You can either choose the Front or Rear wheel
drive driveline configuration and then select the Single Motor
Electric Powertrain (FMU), which is listed in the
Powertrain drop-down menu.
Figure 11. - After selecting the vehicle’s powertrain type, you can also opt for a Battery Pack
body.
Figure 12.
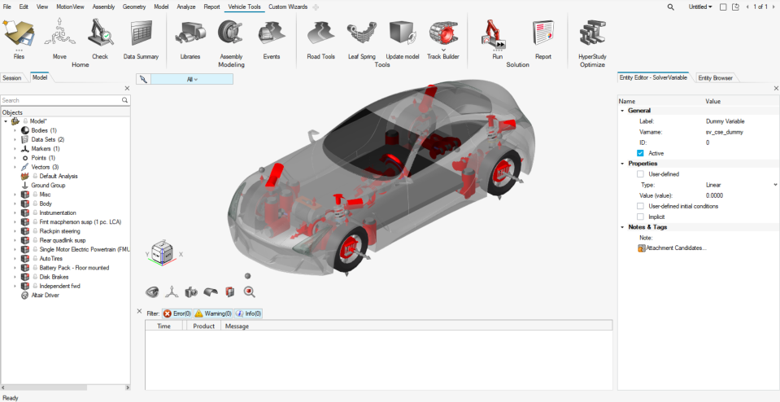
Modifying the FMU Powertrain
You can easily customize the default powertrain specifications to suit a specific requirement by adjusting parameters within the FMU's parameter section. Throttle response, regenerative braking contribution to total braking, and battery’s capacity are the main parameters that can be altered. The vehicle’s behavior parameterization is mainly divided into two main sections regarding motor specifications and regenerative braking.
$---------------------------------------------------------------------ALTAIR_HEADER
[ALTAIR_HEADER]
FILE_TYPE = 'efmp'
FILE_VERSION = 1.0
FILE_FORMAT = 'ASCII'
$--------------------------------------------------------------------------UNITS
[UNITS]
(BASE)
{length force angle mass time}
'm' 'newton' 'degrees' 'kg' 'sec'
(USER)
{unit_type length force angle mass time conversion}
'rpm' 0 0 1 0 -1 6.0
'torque' 1 1 0 0 0 1.0
$-------------------------------------------------------------------------Motor Details
[EFFICIENCY_MAP]
(X_DATA)
{speed}
+0.000000E+00
+8.537861E+01
+3.415145E+02
+7.684075E+02
+1.366058E+03
+2.134465E+03
+3.073630E+03
+4.183552E+03
+5.728759E+03
+7.273966E+03
+8.819173E+03
+1.036438E+04
+1.190959E+04
+1.345479E+04
+1.500000E+04
$-------------------------------------------------------------------------Efficiency
(YZ_DATA)
{a b c d e f g h i j k l m n o p}
+0.000000E+00 +0.000000E+00 +0.000000E+00 +0.000000E+00 +0.000000E+00 +0.000000E+00 +0.000000E+00 +0.000000E+00 +0.000000E+00 +0.000000E+00 +0.000000E+00 +0.000000E+00 +0.000000E+00 +0.000000E+00 +0.000000E+00 +0.000000E+00
+1.218756E+00 +0.000000E+00 +8.323871E-01 +8.348879E-01 +8.207778E-01 +7.975356E-01 +7.686840E-01 +7.357196E-01 +6.984794E-01 +6.564586E-01 +6.174752E-01 +5.872302E-01 +5.100155E-01 +4.613040E-01 +4.190096E-01 +3.827032E-01
+4.875026E+00 +0.000000E+00 +8.814608E-01 +9.318992E-01 +9.365690E-01 +9.319987E-01 +9.231622E-01 +9.104752E-01 +8.949006E-01 +8.728267E-01 +8.505602E-01 +8.328031E-01 +8.007164E-01 +7.678712E-01 +7.359362E-01 +7.055424E-01
+1.096881E+01 +0.000000E+00 +8.376550E-01 +9.363595E-01 +9.546854E-01 +9.582281E-01 +9.565427E-01 +9.522109E-01 +9.459273E-01 +9.365793E-01 +9.269542E-01 +9.121204E-01 +8.934734E-01 +8.735761E-01 +8.534340E-01 +8.334711E-01
+1.950010E+01 +0.000000E+00 +7.779298E-01 +9.228859E-01 +9.543095E-01 +9.639408E-01 +9.664942E-01 +9.656404E-01 +9.628304E-01 +9.575883E-01 +9.519336E-01 +9.419017E-01 +9.290871E-01 +9.152123E-01 +9.008979E-01 +8.863836E-01
+3.046891E+01 +0.000000E+00 +7.155875E-01 +9.027567E-01 +9.474120E-01 +9.628555E-01 +9.686488E-01 +9.702265E-01 +9.695124E-01 +9.667733E-01 +9.626870E-01 +9.544688E-01 +9.441605E-01 +9.329200E-01 +9.210782E-01 +9.086153E-01
+4.387523E+01 +0.000000E+00 +6.563856E-01 +8.792230E-01 +9.373423E-01 +9.584760E-01 +9.673843E-01 +9.709935E-01 +9.718605E-01 +9.707183E-01 +9.671191E-01 +9.594001E-01 +9.499134E-01 +9.392034E-01 +9.267406E-01 +9.036660E-01
+5.056248E+01 +0.000000E+00 +6.314770E-01 +8.682518E-01 +9.322428E-01 +9.559373E-01 +9.662057E-01 +9.706858E-01 +9.721578E-01 +9.716095E-01 +9.679095E-01 +9.601471E-01 +9.505474E-01 +9.390330E-01 +9.168608E-01 NaN
+5.919049E+01 +0.000000E+00 +6.030777E-01 +8.548915E-01 +9.257981E-01 +9.525703E-01 +9.644708E-01 +9.699594E-01 +9.721433E-01 +9.722637E-01 +9.681889E-01 +9.601339E-01 +9.496912E-01 +9.281723E-01 NaN NaN
+7.075054E+01 +0.000000E+00 +5.703066E-01 +8.382680E-01 +9.174994E-01 +9.480588E-01 +9.619707E-01 +9.686980E-01 +9.717496E-01 +9.726024E-01 +9.676793E-01 +9.586062E-01 +9.380106E-01 NaN NaN NaN
+8.699840E+01 +0.000000E+00 +5.315730E-01 +8.168210E-01 +9.063657E-01 +9.418017E-01 +9.583267E-01 +9.666546E-01 +9.708084E-01 +9.720695E-01 +9.655065E-01 +9.453839E-01 NaN NaN NaN NaN
+1.114960E+02 +0.000000E+00 +4.823827E-01 +7.864047E-01 +8.898433E-01 +9.321732E-01 +9.524598E-01 +9.630950E-01 +9.688285E-01 +9.694182E-01 +9.487760E-01 NaN NaN NaN NaN NaN
+1.540854E+02 +0.000000E+00 +4.040688E-01 +7.291549E-01 +8.564716E-01 +9.117700E-01 +9.393322E-01 +9.544374E-01 +9.631752E-01 +9.458014E-01 NaN NaN NaN NaN NaN NaN
+2.104600E+02 +0.000000E+00 +3.119294E-01 +6.435543E-01 +8.010837E-01 +8.758160E-01 +9.149455E-01 +9.372630E-01 +9.507810E-01 NaN NaN NaN NaN
$-------------------------------------------------------------------------ENGINE
[TORQUE_CURVE]
(DATA)
{speed torque}
+0.000000E+00 +2.104599E+02
+8.537861E+01 +2.104600E+02
+3.415145E+02 +2.104600E+02
+7.684075E+02 +2.104600E+02
+1.366058E+03 +2.104600E+02
+2.134465E+03 +2.104600E+02
+3.073630E+03 +2.104600E+02
+4.183552E+03 +2.104600E+02
+5.728759E+03 +1.540854E+02
+7.273966E+03 +1.114960E+02
+8.819173E+03 +8.699840E+01
+1.036438E+04 +7.075054E+01
+1.190959E+04 +5.919049E+01
+1.345479E+04 +5.056248E+01
+1.500000E+04 +4.387523E+01
+1.500000E+04 +0.000000E+00
Throttle response within the traction region is influenced by two key parameters: ‘traction_gamma’ and ‘traction_max’. The right setting should offer correct balance between smoothness and responsiveness. Fine-tuning these settings can result in an improved driving experience by providing the desired balance between these two factors.
You can also determine the vehicle’s regenerative braking amount by handling the relevant parameters. The equations that determine the regenerative braking amount are derived by 1. Regenerative braking distribution is fixed by default to ’60-40’ front-rear. The traction, coasting and regeneration region for motor mapping are described in detail in 1. Vehicle’s coasting boundaries ‘ pcl ’ and ‘ pcu ’ are defined by the parameters ‘ coastm ’,, ‘ coastphi ’, ‘ coastch ’ and vehicle’s maximum velocity ‘ max vehicle speed ’. Vehicle’s regenerative amount for different speeds is determined by a map used as a Look-up table. ‘ pedal_0_regen_percent ’ and ‘ pedal_0_vx ’ are the parameters responsible for the speed – regenerative braking mapping. Finally, ‘ regenpsi ’ is used to define the correlation between throttle and output torque.
Limitations
- The rotational inertia of the motor’s shaft should be added in the rotating bodies in the driveline.
- The default motor configuration assumes that the motor regenerative region is the same as tractive, in terms of efficiency mapping.