Generate Multi-Sphere Particles from a CAD Template
You can use imported CAD meshes created in other applications as particle templates that provide instructions on how to create a particle whose properties are automatically calculated.
- Go to .
-
Click Import and navigate to the file of your choice.
Any templates used in your model must first be imported here.Note: It is recommended to use a template if your model uses Multi-Sphere particles.
-
Select
to display the imported template.You can also choose from the Templates option when a particle shape is selected.
-
Create spheres to match the template outline.
CAUTION: Data related to the particle template is stored in the
*.ptf
file. If you delete this file, the template information will no longer be stored within the model.
Generate Particles from a Template
You can create complex particle shapes based on a CAD template.
-
Import a template from the Options menu (from the
Particle Template) or click Edit to view the
Particle Display menu.
The Generate Particle from Template dialog box uses an imported mesh template of the particle and adds spheres to fill the volume generating a Multi-Sphere particle. -
Click Import and navigate to the file of your choice.
Any templates used in your model must first be imported here.
Generate a Grid
You can generate a grid around the imported template.
Smooth Values
After all spheres are generated, you must perform optimization to remove unnecessary spheres.
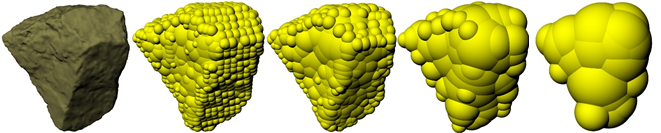
Smoothing Factor | Number of Spheres | Smallest Sphere(mm) |
---|---|---|
1 | 835 | 56 |
2 | 263 | 75 |
5 | 69 | 131 |
10 | 22 | 224 |
Set the Minimum Particle Size
You set the minimum particle size to ensure that there are no particles in the Multi-Sphere which are excessively small.
Use the Hard Template Boundary
You use the hard template boundary option to scale particles towards the center of the template.
- You must use this option when using a large smoothing value. The smoothing value will grow particles outside the template boundary. The smoothing value increases the size of the spheres used to populate the particle, and can lead to a particle that is much larger than the template it was created from.
- Do not use this option in instances where the center of the shape’s bounding box is outside the template, such as toroid, as the particles will scale towards that point.
The GEMM Database
The GEMM database addresses one of the most difficult aspects of DEM modeling by obtaining the appropriate material inputs for a precise representation of bulk materials.
The GEMM database contains thousands of Multi-Sphere material models that represent a variety of materials, including rocks, soils, and ores. It is suitable for engineers working in mining, construction, and agriculture who design large machinery to handle such materials.
The GEMM Material Wizard
You can access the rich material information in the GEMM database to explore example materials and get input decks for use in their EDEM simulation.
-
In the Creator Tree, right-click the Bulk Material or
Equipment Material section and select Open
GEMM Wizard.
Note: The GEMM Database contains only Multi-Sphere models. - On the Welcome screen, select the Search by Material Properties option and click Next.
-
Answer the following questions on the particle Bulk Material behavior:
- What scale is your application?
The GEMM Database comprises numerous material sets that are intended to cover a wide range of material sizes. Each has a size distribution centered on a median value.
Start with the largest size and test it on the application if you are unsure about the size distribution. Working with a test case in which the particles are too large is faster than working with a scenario in which the particles are too small. Since the particle count is lower in a large size material, the simulation progresses faster. If the particles are too small, the time it takes to fill a volume can be slowed instead of moving with the simulation.The actual size ranges used in the GEMM database are: - What is the Bulk Density of your particle
material?
Material Bulk Density is the mass of the material (+ moisture content)' / 'volume of the material as a whole':
- If the interface allows you to select a material's Bulk Density from a list.
- If the real particle material's Bulk Density is close to the
margin of one of the ranges, you may adjust it after the
material file is generated.
You can use the provided GEMM material as a starting point for a small study with variations in the material solids density if a closer match to the bulk density is necessary.
- What is the angle of repose of your material?The angle of repose is a frequently used measure of material that appears in standard test data. Even though such information is not included in current material data reports, it can still be measured in a fairly simple manner without specialized tools (for example, by monitoring the angle of a stockpile). Finally, it is a quantity that is relatively simple to estimate using engineering expertise if there is no access to any testing reports or on-site data.Note: Because measuring an angle of repose with great accuracy is difficult, it is usually viewed as an approximation to the material behavior rather than describing it completely. As a result, the GEMM Database material model should be used as a guide or starting point, and you should be aware that changes in behavior may still exist.The Angle of Repose test is demonstrated in the following example:
The Angle of Repose has a maximum value of 60 degrees in the GEMM database, and any materials with angles greater than this should be calibrated separately. The smallest angles are between 20 and 30 degrees.
-
After you have answered these three questions, a list of ten materials that are the closest matches based on your responses is displayed.Note: You can select one of these materials.
- The top material corresponds to the input angle of repose the best. You can, however, choose different materials from the list.
- The Particle to Particle values of Restitution, Static Friction, and Rolling Friction are referred to as P to P.
- The JKR number represents the material's cohesive energy. Even if both materials have the same angle of repose, a sticky substance will have a greater JKR value than a non-sticky material.
- To avoid overly damped simulations, high JKR cohesion
values should be matched with larger coefficients of
restitution.
Once you have selected a material, the material details including the measured material Bulk Density value are provided.
Alternatively, to retrieve bulk material that you have already searched for, select Search by Material Name and specify the ID number of the GEMM material.
- What scale is your application?
-
Select any of the Equipment Interactions for this material:
- Low Friction
- Medium Friction
- High Friction
-
Select Finish to add the Bulk Material to the
simulation.
This material is added to the following areas:
- Bulk Material
- Properties
- Shape
- Size Distribution
- Interactions (Bulk Material - Bulk Material and Bulk Material - Equipment Material)
Medium friction is designed around a material such as Steel and Material friction is based on an Inclination Test.
A sample of the Bulk Material is placed on a flat plate, which is subsequently inclined until the material slides. A low Bulk Material Angle of Repose will slide at a lower inclination angle than a high Bulk Material Angle of Repose. As a result, the Bulk Material is classified as Low Angle (less than 35 degrees), Medium Angle (more than 35 degrees but less than 45 degrees), and High Angle (greater than 45 degrees).
The Geometry Interactions are then provided using the following table:Material Type Geometry Type Static Friction (p-g) Rolling Friction (p-g) JKR Cohesion (p-g) Inclination Test Results (average results) Low Angle Low Friction 0.3 0.15 0 21 Low Angle Medium Friction 0.45 0.15 0 27 Low Angle High Friction 0.7 0.15 0 34 Medium Angle Low Friction 0.45 0.15 0 28 Medium Angle Medium Friction 0.7 0.15 0 35 Medium Angle High Friction 1 0.15 0 39 High Angle Low Friction 0.7 0.15 0 37 High Angle Medium Friction 1 0.15 Low 46 High Angle High Friction 1.7 0.15 High 49
The Powders Database
The EDEM Powders database is a collection of EDEM material models for powders that includes the static Angle of Repose and the steady-state Shear Stress responses.
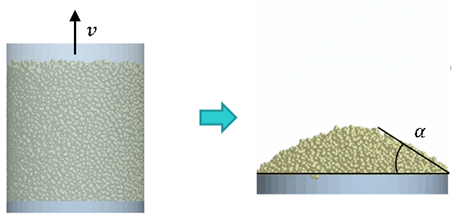
The following figure describes the direct Shear test under constant normal stress. The measurement of the steady-state Shear Stress corresponds to the pre-shear stage of a Shear Cell test performed according to ASTM 6128 or ASTM D6773. Steady-state Shear Stress results are available for 1kPa and 5kPa normal stresses.
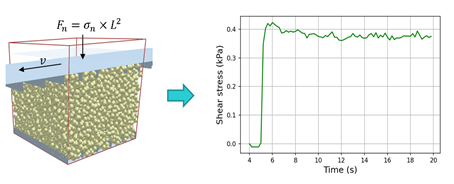
In the interest of computational efficiency, a meso-scopic modeling approach is adopted for the EDEM powder models.
The two-sphere particle shape shown in Figure 3 and the normal relative particle size distribution described in the table are adopted to capture shear dilation effects and avoid non-physical packing states (Härtl, J., & Ooi, J. Y., 2011). The standard particle diameter in the database D_max is 1.5 mm, but different values can be used in certain cases.
The interaction forces at the meso-contact scale are described in the Edinburgh Elastic-Plastic-Adhesive (EEPA) and Type C Rolling Friction models.
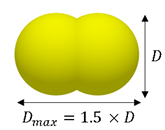
Particle Size Distribution | |||
---|---|---|---|
Type | Dmin/D50 | Dmax/D50 | ơ/D50 |
Normal | 0.85 | 1.15 | 0.15 |
Fixed Parameter Space | |
---|---|
Particle Poisson’s ratio v | 0.25 |
Particle Shear Modulus G (Pa) | 1e+7 |
Particle solid density ρs (kg/m3) | 1000 |
Particle coefficient of restitution e | 0.1 |
Particle – geometry coefficient of static friction μg | 0.5 |
Particle – geometry coefficient of rolling friction μrg | 0.1 |
EEPA tangential stiffness multiplier ktan | 0.667 |
EEPA loading exponent n | 1 |
EEPA tensile exponent kadh | 3 |
Variable Parameter Space |
---|
Particle – particle coefficient of static friction μs |
Particle – particle coefficient of rolling friction μr |
EEPA constant pull-off force f0 |
EEPA surface energy γ (J/m2) |
EEPA contact plasticity ratio λ |
- The static Angle of Repose
- The steady-state Shear stress at 1 kPa normal stress
- The steady-state Shear stress at 5 kPa normal stress
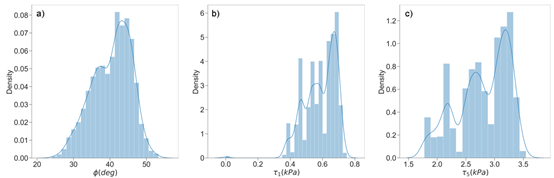
The database can be searched using multiple responses at the same time, and the results are sorted based on the total relative error between the requested response values and the database results.
- The bulk cohesion and compressibility, which are qualitatively categorized using
the bond number and the EEPA contact plasticity ratio respectively.
- The bulk density, which his captured via particle solid density and Bond number scaling of the baseline values in the data set, and has variable ranges for the different bulk cohesion levels.
- The mean particle diameter, which is available as an input if the search includes only steady-state Shear responses. The scaling rules proposed by Thakur et.al are applied to compute the relevant parameter values in this case.
The EDEM Powders Wizard
The EDEM powders database is a collection of EDEM material models for powders that includes the static Angle of Repose and the steady state Shear Stress responses.
-
In the Creator Tree, right-click the Bulk Material or
Equipment Material section and select Open
Powders Wizard.
-
Follow the steps in the wizard and specify the input parameters for the Powders
database.
-
In the Confirm Search Parameters dialog box, verify the
parameters and then click Next.
EDEM populates the material and model parameters.