Higher Pair Constraints
Tutorial Level: Intermediate In this tutorial, you will learn how to model point-to-curve (PTCV) and a curve-to-curve (CVCV) joint.
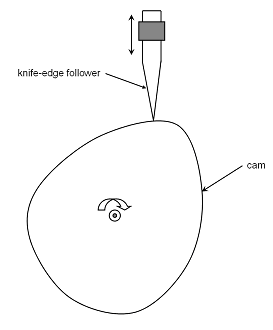

In this tutorial, you will model a roller type cam-follower mechanism first using a PTCV and later a CVCV constraint.
Open and Review Model
In this step, you will review the cam-follower roller model.
- Start a new MotionView session.
-
From the Geometry ribbon, select the
Open tool.
Figure 3. -
Browse to your working directory, select
CamFollower_start.mdl, and click
Open.
The model opens in the modeling window.
Figure 4. Model Overview -
Review the model. It consists of:
- A Cam, a FollowerRoller, and a FollowerShaft body
- A CamPivot joint of type Revolute with Ground Body
- A FollowerTransJoint, which is a Translation joint connecting FollowerShaft with Ground Body
- A FollowerRoller joint, which fixes the FollowerRoller to the FollowerShaft
- A point FollowerPoint at the location where the roller sits on the cam
- Graphics Cam of type CADGraphics
- Other graphics and points
Create Markers
In this step, you will create markers for the cam-follower model.
-
Select the Markers tool in one of the following
ways.
- From the Model Browser, right-click on Model and select from the context menu.
- From the Geometry ribbon, select the
Markers tool.
Figure 5.
-
Create the CamMarker.
-
Create the FollowerMarker.
Create Curves
In this step, you will learn how to extract a curve from the Cam graphics and define the follower roller’s curve using a math expression.
-
Create a Cam curve.
-
Create the roller curve.
Note: The roller curve will be created as a circle using the sin and cos functions in the Y-Z plane.
-
Configure the roller curve.
-
From Geometry ribbon, select the
Graphics tool to open the Add
CADGraphic dialog.
Figure 16. -
From the Type section of the Add CADGraphic dialog, select
Curve from the drop-down menu.
Note: The title of the Add CADGraphic dialog will change to Add CurveGraphic upon selecting Curve.
-
Enter FollowerRollerProfile for Label.
Figure 17. - Click OK to create the FollowerRoller’s curve graphic and exit the dialog.
- From the General section of the FollowerRollerProfile curve graphic's Entity Editor, verify type is set to Body/Point.
-
Click the Ground Body field and select the
FollowerRoller by clicking on it in the modeling window or using the Advanced Selector
.
-
Click the Global Origin field and select the
FollowerRevJoint point from the modeling window or using the Advanced Selector
.
-
Select the Unresolved field and click
to open the Select a curve dialog.
-
From the Select a curve dialog, select the
FollowerRollerProfile curve under .
Figure 18. Figure 19. Cam and FollowerRoller graphic's curves - From the menu bar, click and save the file as CamFollower_PTCV.mdl.
Create the PTCV Joint
In this step, you will create the point-to-curve (PTCV) joint.
-
Enter the Advanced Joints context through one of the
following:
- From the Model Browser, right-click on
Model and select .
OR
- From the Model ribbon, select the
Advanced Joints tool.
Figure 20.
- From the Model Browser, right-click on
Model and select .
-
Create the PointToCurve advanced joint.
-
From the Entity Editor, edit the Properties of the PTCV
advanced joint.
- From the General section, enter PTCV for Label.
-
Select the Ref Marker collector and click twice
on the Advanced Selector
to open the Select a Marker dialog.
- From the Select a Marker dialog, select CamMarker under and click OK.
-
From the guide bar, click
Cancel
to exit the Advanced Joints context.
Note: Choosing the correct reference markers will cause the automatic selection of the corresponding bodies, as shown in Figure 23.Figure 23. Advanced joint Entity Editor selections
Specify the Cam Motion
In this step, you will specify a motion for the cam using an expression.
-
Enter the Motion context through one of the
following:
- From the Model Browser, right-click on
Model and select .
OR
- From the Model ribbon, select the
Motions tool.
Figure 24.
- From the Model Browser, right-click on
Model and select .
- From the guide bar, verify that the Joint option is selected.
-
From the modeling window, select the
CamPivot joint.
Figure 25. -
From the microdialog, click
Create
.
- From the General section of the Entity Editor, enter CamMotion for Label.
- Verify that Property is set to Displacement.
-
From the Properties section, set Type to Expression and
enter
`PI*TIME`
in the Expression field. -
From the guide bar, click Cancel
.
Figure 26. Cam motion Entity Editor parameters
Specify Gravity
In this step, you will specify gravity for the model in the negative Z direction.
-
From the Geometry ribbon, select the
Gravity tool from the Setup group.
Figure 27. - From the microdialog, verify that the Enabled check box is selected.
- Verify X is set to 0.
- Verify Y is set to 0.
-
Verify Z is set to -9810.
Figure 28.
Specify Output Requests
In this step, you will specify output requests.
-
Enter the Output context through one of the
following:
- From the Model Browser, right-click on
Model and select .
OR
- From the Analyze ribbon, select
the Requests tool from the Outputs tool
group.
Figure 29.
- From the Model Browser, right-click on
Model and select .
- From the guide bar, click the Displacement drop-down menu and select Expressions.
-
Click the Create and Edit icon
.
- From the General section of the Entity Editor, enter PTCV Reaction for Label.
-
From the Properties section, select the field next to F2
and click
to open the Expression Builder dialog.
-
From the Expression Builder, enter
`PTCV({aj_0.idstring},0,2,0)`
.Figure 30. - Click OK.
-
Repeat steps 5 - 7 for F3, F4, F6, F7, and F8 by changing the third parameter in the expression
to 3, 4, 6,
7, and 8 accordingly.
Figure 31. Note: The PTCV (id, jflag, comp, ref_marker) function returns the reaction on the PTCV joint:- id
- ID of the PTCV joint
- jflag
- 0 returns reaction on the I-marker and 1 on the J-marker of the joint.
- comp
- Component of the reaction
- 1
- Force magnitude
- 2
- Force in X
- 3
- Force in Y
- 4
- Force in Z
- 5
- Torque magnitude
- 6
- Torque in X
- 7
- Torque in Y
- 8
- Torque in Z
- ref_marker
- Reference marker (0 implies Global Frame).
-
Right-click in the empty space of the modeling window
and select
to exit the Output tool.
-
Save the model
.
Run the Model
The PTCV Cam follower model is ready to solve.
- From the Model Browser, select Default Analysis.
- From the Analysis Parameter section of the Entity Editor, enter 4 seconds for End Time.
-
From the Analyze ribbon, select the
Check Model tool to check the model for errors.
Figure 32. -
From the Analyze Ribbon, select the Analysis settings
tool from the Run tool group to open the Run Motion
Analysis dialog.
Figure 33. -
From the Run Motion Analysis dialog, configure the Motion
Analysis settings.
View Results
In this step, you will learn how to view the animation and plot the vertical displacement of the follower roller.
-
Once the solver has finished and the Review Run Results
context is active
, navigate to the Animation toolbar and click Play
to start the animation.
-
From the Run Status dialog, click
Plot to open HyperGraph in a new page.
The Create Curves by File dialog opens with the result CamFollower_PTCV.abf file pre-selected.
-
Plot the vertical displacement of the follower roller.
- Under Types, select Body.
- Under Request, select Part/30103 FollowerRoller.
- Under Component, select Z.
- Click Plot to plot the Z profile of the center of mass of the follower roller.
Figure 35. Create Curves by File -
Once the plot is created, click Cancel.
The profile for the Z displacement of the follower is displayed as in Figure 36.
Figure 36. Follower body Z-displacement plot
Check the Model for Potential Lift-Off
In this step, you will check the cam-follower mechanism for potential lift-off by plotting the Z profile of the PTCV reaction on the follower roller.
In some cases, the dynamics of the system may cause the follower to lose contact with the cam. This is called "lift-off." In such cases, modeling the system with a PTCV will give you incorrect results because the joint constrains the follower point to always be on the curve (and hence cannot model lift-offs). For such cases, you must use contact modeling. However, you will want to start with a PTCV model since it is a lot easier than modeling contact. Given this scenario, model the system using a PTCV joint and monitor the PTCV joint reaction. If the reaction on the follower is a ‘pulling’ reaction, this indicates lift-off would have occurred and you must switch to a contact model. Otherwise, the contact model is unnecessary. Now, you will check the model you used in the tutorial. The follower is moving along the Z-axis, so any negative reaction along the Z-axis is a 'pulling' reaction.
-
From the Page Controls toolbar, click
and then
to enable a vertical 2 window layout.
Figure 37. Two windows are shown side by side.
- Click on the right window to set it as active.
-
From the Line Chart ribbon, click the Open icon
to open the Create Curves by File dialog.
-
Configure the Create Curves by File dialog settings.
- Under Types, select Expressions.
- Under Request, select REQ/7000000 PTCV Reaction.
- Under Component, select F4.
-
Click Plot and then Cancel.
The Z profile of the PTCV reaction on the follower roller is as shown in Figure 38.
Figure 38. Z profile of the PTCV reaction on the follower roller The Z component of the PTCV reaction on the Follower Roller is almost always positive. Therefore, only a very slight tendency for lift-off is evident in the simulation, so the PTCV model is deemed partly acceptable for analyzing this mechanism.
Modify Joint to Enable Follower-Roller Rotation
In this step, you will prepare the model for simulating the cam follower with the CVCV (curve-to-curve) joint.
- Return to the MotionView model page.
- From the Model Browser, select the FollowerRollerJoint under to display its properties in the Entity Editor.
- From the General section of the Entity Editor, set Type to Revolute.
- From the Orientation section, verify Method is set to Vector.
-
Click the Global Z field and then
to open the Select a Vector dialog.
- From the Select a Vector dialog, select the Global X vector under and then click OK.
Create CVCV Joint
In this step, you will create the CVCV (curve-to-curve) joint.
-
Enter the Advanced Joints
guide bar by doing one of the
following:
- From the Model Browser, right-click on
Model and select .
OR
- From the Model ribbon, select the
Advanced Joints tool.
Figure 39.
- From the Model Browser, right-click on
Model and select .
-
From the guide bar, click the
PointToCurve drop-down menu and select the
CurveToCurve option.
Figure 40. - From the modeling window, select FollowerRollerProfile for Curve 1.
- Select CamProfile for Curve 2.
-
From the microdialog, click
Create
to set up the Advanced Joint and open the Entity Editor.
- From the General section of the Entity Editor, enter CVCVfor Label.
-
Click the Global Frame field next to Ref marker 1 and
then
to open the Select a Marker dialog.
- From the Select a Marker dialog, select FollowerMarker under and click OK.
- Repeat steps 7 and 8 for Ref marker 2 and select CamMarker instead of FollowerMarker.
-
From the guide bar, click
Cancel
to exit the Advanced Joints guide bar.
-
Create output for CVCV.
- Deactivate the PTCV joint and output.
Run the Model
In this step, you will run the cam-follower roller model.
-
From the Model ribbon, select the Check
Model tool and check the model for errors.
Figure 42. -
From the Analyze ribbon, select
Save to save the model before running the
analysis.
Figure 43. -
From the Analyze Ribbon, select the
Analysis settings tool from the Run tool group to
open the Run Motion Analysis dialog.
Figure 44. -
From the Run Motion Analysis dialog, configure the Motion
Analysis settings.
- Enter CamFollower_CVCV for Run name.
- Set Output directory to your <working directory>.
- Click Run to initiate a live simulation, the progress of which can be viewed from the Run Status dialog.
View Results
Review and compare the results.
- Once the solver has finished, navigate to the previously created plot window for roller Z displacement in HyperGraph.
- Click on the left window to set it as active.
-
From the Line Chart ribbon, select the Open file icon
and, from the Create Curves by File dialog, click
next to Choose Data File.
- Navigate to your working directory and select the CamFollower_CVCV.abf file.
-
Plot the Z displacement of the FollowerRoller.
- Under Types, select Body.
- Under Requests, select Part/30103 FollowerRoller.
- Under Components, select Z.
- Click the right window to set it as active.
-
Overlay the reaction force of the CVCV joint with that of the PTCV joint in the
other window.
- Under Types, select Expressions.
- Under Request, select REQ/7000000 PTCV Reaction.
- Under Component, select F4.
Figure 45. Z profile of the PTCV reaction on the follower roller - From the menu bar, click and save the file as sess_cam_follower.mvw.