Oka Wear Model
The Oka or Impact Wear contact model extends any Base Model to give an estimation of erosion depth for Geometry surfaces due to particle impacts.
The wear depth is determined as follows:
Where dw is the wear depth, α is the particle impact angle, g(α) is the impact angle dependence of normalized erosion, E(α) is the wear volume per unit mass, mp is the mass of the particle and A is the Geometry element area.
The wear volume per unit mass is defined as:
Where W is the materials wear constant, v is the particles impact velocity, Hv is the Vickers hardness of worn material, D is the particle diameter and k1 is an experimentally derived coefficient.
The impact angle dependence of normalized erosion is defined as:
Interaction | Configurable Parameters | Position |
---|---|---|
Particle to Geometry | Assign a wear constant, the Vickers Hardness value for each Equipment Material-Particle interaction and Scaling Factor (if Deformation enabled). | Last |
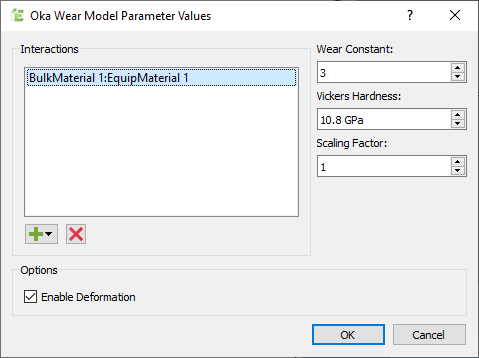
- Select the Enable Deformationcheck box to enable Geometry deformation.
- If you select Enable Deformation, you must specify the Scaling Factor which allows the deformation results to be scaled as desired.
Material | WOka | Vickers Hardness (GPa) |
---|---|---|
Carbon Steel | 3 | 0.54 - 1.18 |
Stainless Steel | 10 | 1.770 |
Aluminum | 1000 | 0.36 |