Autobox
Autobox will create a voxel design space so that topology optimization can be performed on a part or subsystem.
Additional capabilities include the ability to manage and connect to hard point locations.
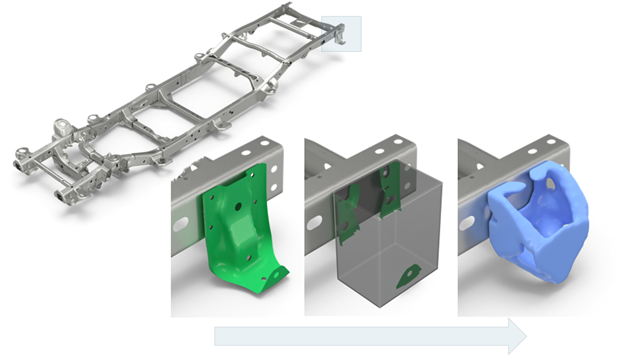
The workflow requires that the voxel design space size is specified along with the RBE3 connection tolerance. Once defined, the initial selected input can be components, parts, or elements. Once the selection has been made, a bounding box will be previewed. The bounding box preview shows where the design space will be created.
The bounding box can be moved to a new position or resized. The last option can be used to locate the bounding box globally or aligned to the principal axis; depending on the input, one may be better than the other.
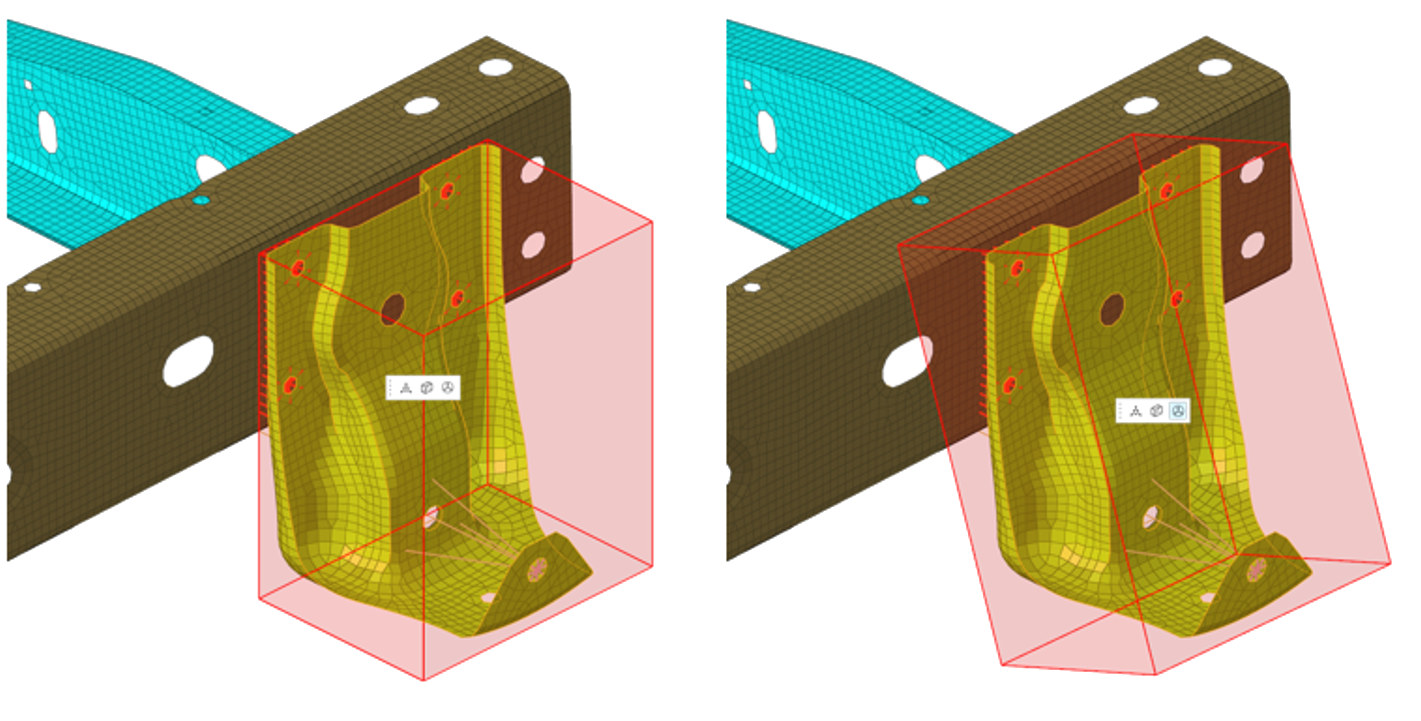
If Connect All is active, individual hard points will not be considered and the whole design space will be connected via RBE3’s to the initial selected input.

If Connect All is inactive, it is possible to select individual nodes which are defined as hard points and the RBE3 connectivity will connect to the local surrounding elements. The number of rows of connected elements can be controlled, default is two rows. In Figure 4, all five hole hard point locations are selected.

Upon creation, the voxel design space is created along with the design variable (DTPL) and PSOLID property. Once the responses, objectives, and constraints are defined, the topology optimization can be performed.
- Left: full design space, solid with symmetry
- Center: manually reduced design space, solid with symmetry
- Right: full design space, stamp thickness with symmetry
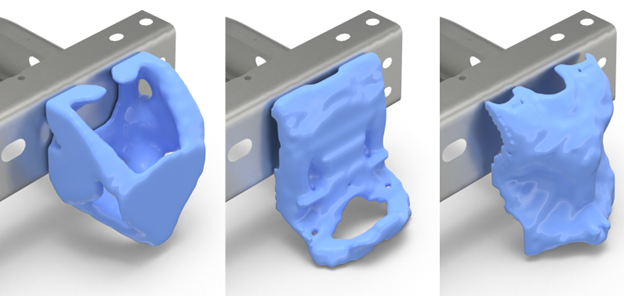