Seam Weld Fatigue
The seam weld fatigue implemented in SimSolid is based on linearization of stress in the conjunction with Volvo method and following that it predicts fatigue damage and life. Linearized stress decomposes a through-thickness elastic stress field into equivalent membrane and bending.
This method determines the contribution of bending to the total stress, and from this determines whether the weld is essentially stiff or flexible. The method typically requires two S-N curves. One is a bending S-N curve which is dominated by bending stress, and the other is a membrane S-N curve which dominated by membrane stress. Interpolation is made between the bending and membrane SN curves based on the degree of bending.
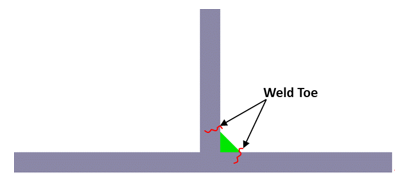
Weld Stress Calculations
- If the local X-axis is not parallel to the global Y-axis:Zlocal=Xlocal*YglobalYlocal=Zlocal*Xlocal
- If the local X-axis is parallel to the global Y-axis:
Local Y-axis ( Ylocal ) is negative of global-X if local-X is along positive global-Y, and vice versa.
Zlocal=Xlocal*Ylocal
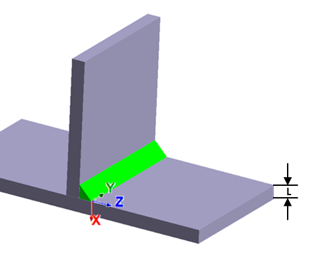
- σmi is equal to the ith component of membrane stress.
- σi is equal to the ith component of extracted stress value.
- σbiS is equal to the ith component of bending stress at the entry.
- σbiE is equal to the ith component of bending stress at the exit.
- L is equal to the ith Length of the stress linearization segment.
- x is equal to the position of a point along the segment.
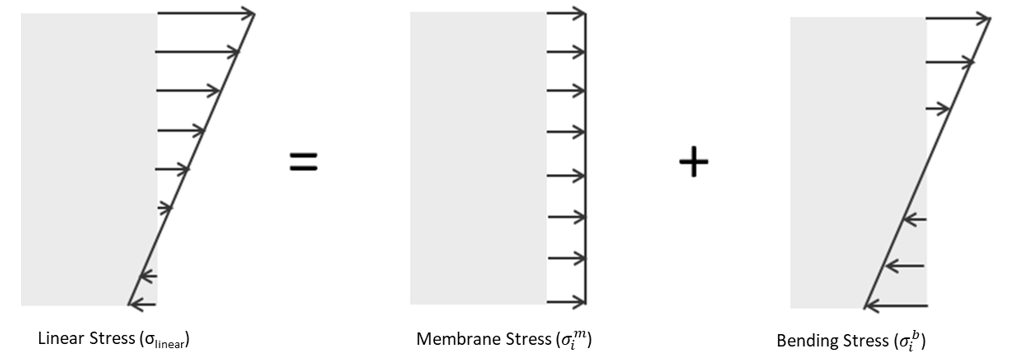
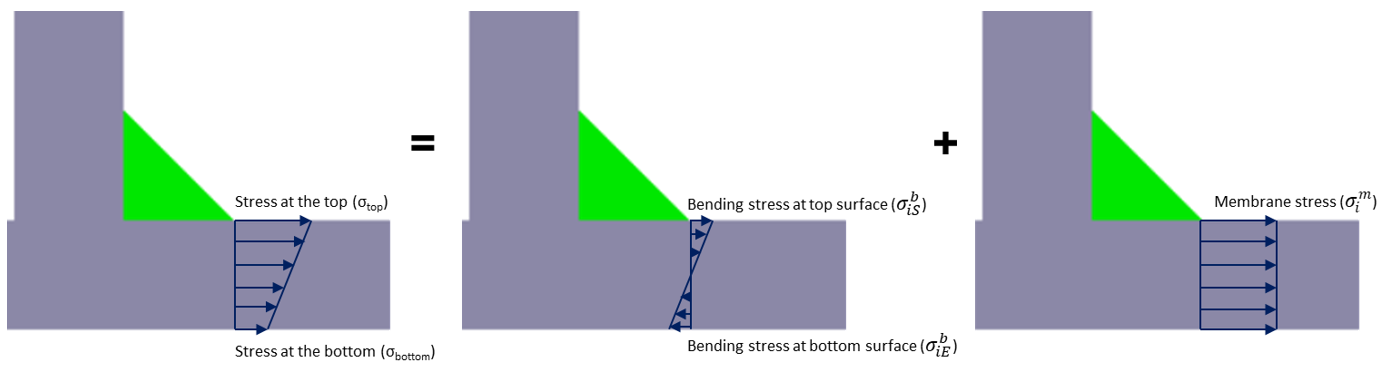
Bending Ratio (r)
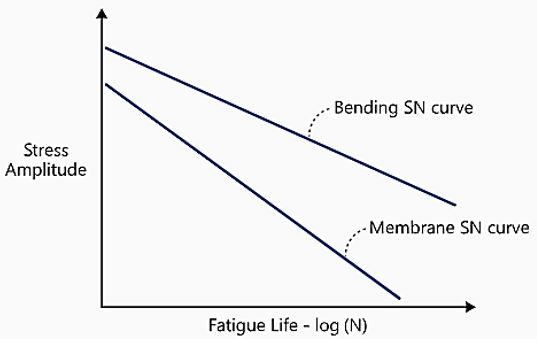
- σbi is the maximum bending stress equal to 6T2∫T/2−T/2σixdx .
- σmi is the maximum membrane stress equal to 1T∫T/2−T/2σidx
- σ2TOP is the square of the maximum stress at the top surface when the damage is calculated, that is, at weld toe.
- r is the bending ratio.
It is the weighted average of the bending ratio over all points in the loading time history.
An interpolation factor (IF) is now defined as:
Interpolation between Membrane and Bending S-N Curves
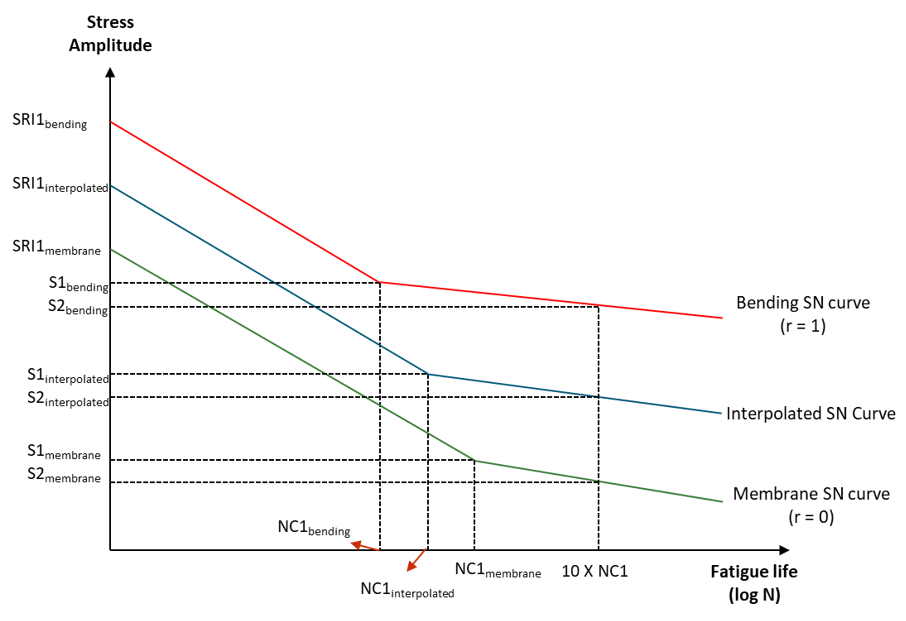
This defines the stress level at Nc1interpolated cycles. These two points define the first section of the curve up to Nc1interpolated cycles. The last section is defined by finding a third point as follows. A life value is defined being 10 times greater of the Nc1 values for the stiff and flexible curves. From these, we can calculate S2bending and S2membrane. From these, we can interpolate to get S2interpolated which defines the high cycle part of the curve.
Thickness
Optionally, a thickness (size effect correction) may be applied, based on thickness t of the part. It operates as follows:
There is no effect if t≤Tref (the reference thickness or threshold can be specified in the fatigue solution settings).
The fatigue strength is reduced by a factor of (Treft)n , where n is the thickness exponent, if t>Tref , at all lifetimes (used as a factor to up the stress).
Mean Stress Correction
FKM mean stress correction is supported for seam weld fatigue. Stress sensitivity can be defined in the fatigue solution settings dialog via the mean stress correction field. Mean stress correction for seam weld fatigue can be enabled through the seam weld fatigue solution settings dialog.
Based on FKM-Guidelines, the Haigh diagram is divided into four regimes based on the Stress ratio (R=Smin/Smax) values. The corrected value is then used to choose the SN curve for the damage and life calculation stage.
- Regime 1 (R>1.0): SAe=Sa(1−M)
- Regime 2 ( −∞≤R≤0.0 ): SAe=Sa+M*Sm
- Regime 3 (0.0<R<0.5): SAe=(1+M)Sa+(M/3)*Sm1+M/3
- Regime 4 ( R≥0.5 ): SAe=3Sa(1+M)23+M
- SAe is the stress amplitude after mean stress correction (Endurance stress).
- Sm is the stress amplitude, and M is the mean stress sensitivity.
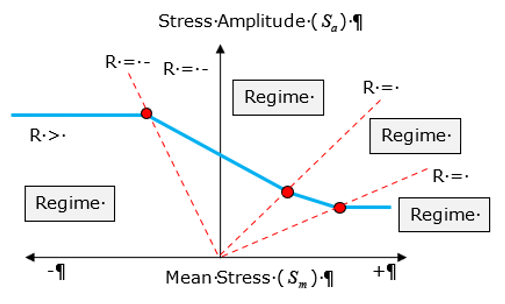