FMVSS 201 U – Upper Interior Head Impact
Use the Fmvss201U Marking tool to streamline the vehicle marking process by incorporating necessary input data for vehicle parts.
Simultaneously, the Fmvss201U Positioning tool efficiently handles the positioning of impactors and exports solver decks with minimal input from you. This not only simplifies the processing of this intricate regulation but also expedites the initiation of simulations, saving valuable time. This tool supports both left and right-hand drive vehicles.
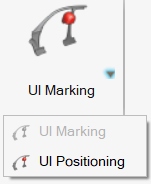
The FMVSS 201U tool exports the primary file automatically for each chosen impact point, seamlessly integrating the impactor include file and transformation cards. It is essential to pre-prepare the main files for each impact load case with the required include files, excluding the impactor include, as part of the preliminary setup.
FMVSS 201 U Marking

- Method
- Marking methods:
- Testing Side
- Marking can be done on both sides of the vehicle, either the left or right side.
- Vehicle Front Axis
- Orientation of the vehicle -X or +X.
- H-Point Offset
- Method to define the seat reference point offset:
- Weather Stripping offset
- If weather stripping is not available in the vehicle model, you can add the offset value for it, which can affect the APR point calculation.
- Windshield offset
- If the vehicle model does not include any windshield frame parts, you can provide a windshield offset value, which will be utilized to calculate the APR.
- Import Selections
- You can conveniently retrieve previously selected essential data from a saved CSV file, thus saving valuable time that would otherwise be spent repeating the selection process.
- Save Directory
- Directory for saving the selection in CSV format.
Automatic Marking
-
Select the standard impact point areas where impact points marking will be done
with automatic marking.
Figure 2. - AP – A Pillar
- UR – Upper Roof Area
- BP – B Pillar
- OP – Other Pillar
- RP – Rear Pillar
- FH – Front Header
- RH - Rear Header
- SR – Side Rail Area
By default, AP and UR are selected as further point selection is dependent on the APR point and upper roof area marking.
-
Enter seating reference points.
- Enter SgRP Front and SgRP Rear points coordinates.
- Select the point location in the modeling window.
Figure 3. Figure 4.
The points CG-F1 and CG-F2 are calculated with reference to SgRP Front and CG-R is calculated with reference to SgRP Rear. -
On the guide bar, click
and
to navigate through the selections for the different windows and frames.
-
Select several required areas/parts of the vehicle mentioned in FMVSS201
regulation to achieve correct result.
- Exterior Parts: Selection of outside BIW parts above Pillars and the Roof parts.
- Interior Parts: Selection of all Pillar trims, Headliner parts.
- Windshield: Selection of Windshield and the trim surrounding it.
-
Select the trim parts to which impact points will be marked.
Selection is disabled until you select the required parts.
- Select A Pillar parts for marking of AP1, AP2 and AP3 legal impact points.
Figure 5. AP1 or APR is computed based on vehicle data in accordance with regulations, utilizing selected parts. If Windshield offset and/or Weather stripping offset are entered in the hamburger menu, the APR is then determined by the provided values. AP2 and AP3 points are contingent upon APR, with no additional definitions needed for AP2.
For AP3 points, you must input the highest point of intersection between the instrument panel and the A Pillar trim. This can be achieved by selecting a point or using advanced selection methods.Figure 6. -
Once all definitions are completed in this microdialog,
click Mark to start the automatic calculation of design
points.
The design points display in the Model Browser.
Figure 7. Construction entities
Upon marking in compliance with regulations, geometric generation of points, lines, and planes takes place. You can utilize the legends available under the context guide bar to display and verify the construction of design points.Figure 8. Figure 9. -
Upper Roof Zone is to be marked by selecting only interior roof parts. As per
the regulation with the use of APR, UR zone will be marked on interior roof
parts with the Center M marking.
Figure 10. -
Next is the selection of B Pillar area for marking. In the microdialog associated with it select two centerline nodes to
define centerline. Additionally, highest point of front door opening is needed.
With this input you can mark BPR (B Pillar Reference point) BP2 can be picked up
anywhere on seat belt anchorage.
Figure 11. -
For BP3 point Lowest point of door opening reference needs to be selected. For
BP4 point no extra input is needed.
Figure 12. -
If the vehicle model contains other Pillars (C or D Pillar) besides B Pillar
and rear Pillar you can select the Pillar and define the impact points with the
similar workflow inputs as B Pillar as shown in following microdialog.
Figure 13. -
The RP1 point for Rear Pillar needs only Rear Pillar parts to be selected. If a
seat belt anchorage is located on the Rear Pillar, then RP2 can be selected
anywhere on seat belt anchorage.
Figure 14. Figure 15. -
For the identification of FH1 and FH2 on the front header, no special
definition is necessary. If the vehicle is equipped with a sunroof, select
Sunroof Parts in the selection.
FH2 will be appropriately marked on the sunroof opening.
Figure 16. Figure 17. -
For calculating RH1 point on rear header no further definition is required.
Activate the checkbox for RH1 and click Mark.
Figure 18. Figure 19. -
After switching to side rail marking, for side rail targets min. required
definitions are APR and UR lines. No further definitions are required for
SR1.
There are two SR2 targets. One is behind APR (v) and another is front of BPR (h) and can be calculated when APR, BPR and UR lines are available. SR3 points prerequisites BPR, which will be marked behind B Pillar automatically. If there is seat belt anchorage or grab handle located on the side rail you can select SR3 point anywhere on those parts.
Figure 20. Figure 21. - You can click Mark All at the end of the workflow, instead of clicking Mark for all the targets.
-
Click the Save icon
to save all of these selections and reference points.
Selections will be saved in the .csv file in the working directory specified in the hamburger menu. You can retrieve these selections by importing this file if the model is the same with minor changes. -
Click the arrow next to the Save icon to redirect to the FMVSS 201U Positioning
workflow.
Each designated impact point can be accessed in the Design Points entity listed in the Model Browser providing comprehensive data on the point, including its structural properties.
Figure 22. Positional parameters according to the regulation are important for positioning the headform within the allowable approach angles and move back angle allowed. Under positioning results, achieved approach angles, point of contact on forehead, move back angle achieved, headform shot direction data achieved after the positioning are inputted by the tool.
Manual Marking
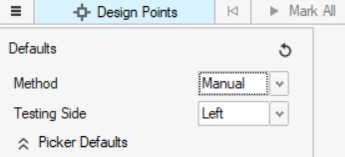
- Select the impact location from the guide bar.
-
Click Mark All to automatically generate the Design
Point entities.
Figure 24.
Test Lab Marking
Test Lab marking allows you to directly read a CSV file containing the information for the impact locations that a test laboratory can provide.
- Select the CSV file from the options menu options.
-
Click Mark to automatically create the Design Point
entities at the defined locations.
Figure 25. Here is an example of a CSV file:Figure 26.
FMVSS 201 U Positioning
- Vehicle model with target impact points marked on interior areas of interest.
- Free motion Headform (FMH) model with Forehead impact zone marked with designated part.
- Main input file ready with required include files referenced.
After importing the vehicle model and FMH you can start the positioning workflow.
-
Click
on the guide bar to define positioning options.
- Vehicle Front Axis
- Orientation of the vehicle -X or +X.
- Positioning Method
-
- Automatic
- Default way of positioning the FMH automatically.
- Manual
- Manipulate the FMH and position it.
- Offset
- Offset value of FMH from the impact point.
- Velocity
- Impact velocity.
- Section cut in design point review
- Review positioned FMH in section cut.
- Export Parameters
-
- Transformation Type
- Choose between the following solver transformation
definitions for the impactor position.
- LS-DYNA
- *NODE_TRANSFORM
- *INCLUDE_TRANSFORM
- Radioss
- /GRNOD
- //SUBMODEL
- PAM-CRASH
- TRSFM/
- LS-DYNA
- Main File
- File path to the main input deck to be used for the generation of the decks.
- Headform File
- File path to the headform input deck to be used as the include file in the main input deck.
- Output Directory
- Directory where all solver decks for the selected impact locations to be simulated are created.
- Design Point name for directories and include file names
- This option takes the name of the Design Point entity for the creation of sub-folders and solver deck names.
- Create a folder for each design point in Export Directory
- When activated, this option creates a sub-folder per the selected target point in the Output Directory location. When not activated, all main decks and includes are written in the Output Directory location.
-
Select the entities required.
On the guide bar, click
and
to cycle through the entity types of the positioning process.
The tool will attempt to automatically position the headform based on the specified horizontal, vertical, and backward angle in the positioning parameters for each point.Figure 31. Automatic Positioning of FMH on Trim If a suitable position is identified, the Auto checkbox will be marked, and the configuration will be saved. Automatic Positioning: Initially, the FIZ node at the center of the Forehead Impact Zone aligns with the target impact point, and the FMH is positioned to ensure alignment of the FIZ normal vector with the normal of the target point. The distance between them is minimized, taking into account any specified offset in the hamburger menu. The specified range of horizontal and vertical approach angles, as outlined in the regulation, is honored.Figure 32. Positioning Parameters According to Regulation The microdialog for positioning will also include manual positioning tools. If automatic positioning is unsuccessful, the headform will return to its initial position, with the Trim node and FIZ node normals aligned to each other.Figure 33. Microdialog for Positioning You can navigate through design points using the arrows and observe whether they are automatically positioned or not.- Rotate Headform
- Manual rotation of FMH in horizontal and vertical direction.
- Translate in shot direction
- You can translate the FMH in shot direction, that is, in X
direction of FMH system to verify first point of contact to the
trim surface.
Figure 35. Translate in Shot Direction - Initial Position
- Reset FMH at initial position at target point.
- Store Position
- Store the auto/manual FMH position to export.
Figure 36. Metadata Stored for Positioned Impact Point
When you click Store position, the design point will be saved along with its position metadata, which can be exported. If this option is not enabled during manual positioning, the information will not be included in the export.
FIZ node selection – Select FIZ node on forehead for positioningFigure 37. FIZ Node Selection During manual positioning, you attempt to identify the appropriate position by adjusting the node on the Forehead Impact Zone (FIZ), while adhering to the allowable angles. To facilitate this, incremental shifting of nodes is enabled through the use of vertical and horizontal node selection arrows.
-
After successfully positioning the FMH, click Export to
export the impact point positions.
This will export solver decks for all stored/auto positioned design points.
Before performing this operation, you should ensure that the Export Parameters mentioned in the hamburger menu are correctly configured.
If you want to export the headform deck, you can use the Transformation type *INCLUDE_TRANSFORM in the LS-DYNA profile and //SUBMODEL in Radioss. Another option is to export the headform data using NODE_TRANSFORM in LS-DYNA and /GRNOD in the Radioss profile. For PAM-CRASH, the default transformation type is TRSFM/. In the later case you need to select the parts of the headform which are needed for the export.Figure 38. Export of Positioned Impact Points

Pre-Requisites on the Headform Model
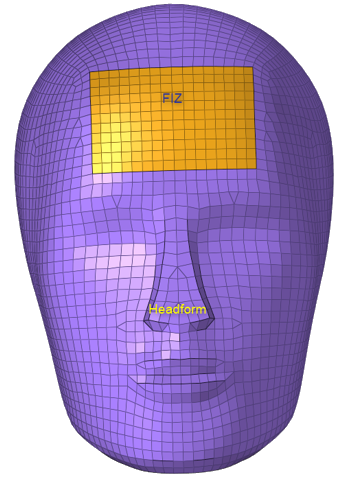
Export Solver Decks
This tool enables you to export ready-to-run solver decks for all of the impact locations.
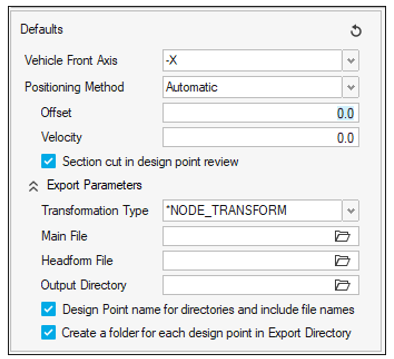
The Main File is the user-defined main input deck containing the include structure of the final model (Upper Interior model, contacts, controls, boundary conditions, …)

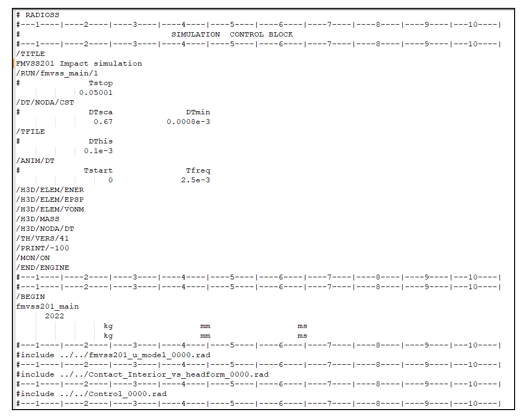
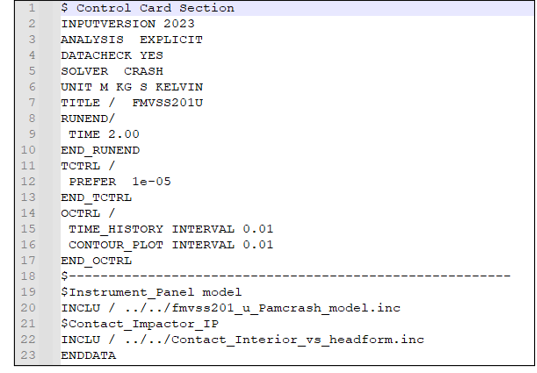
Headform File should point to the headform model that the tool will define as an include in the Main File during the export of the decks.
The Output Directory is the location where all of the solver decks for each impact location are written out.
During the export process, the tool generates an additional include file containing the transformations to apply on the impactor using the Transformation Type.
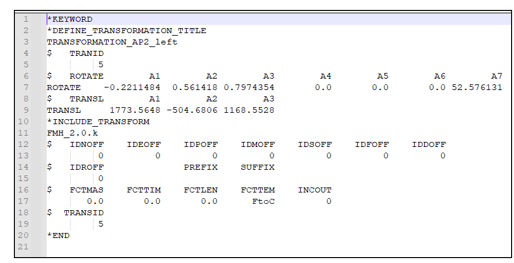
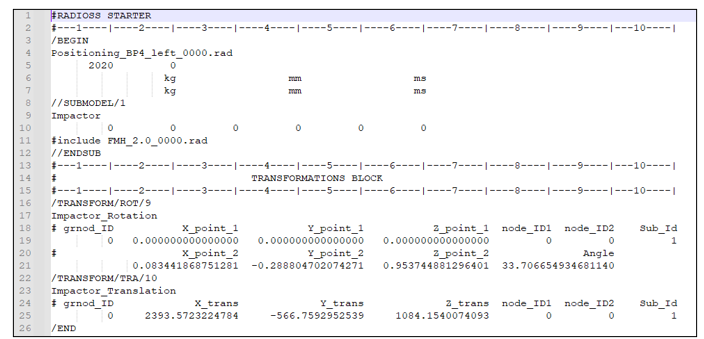
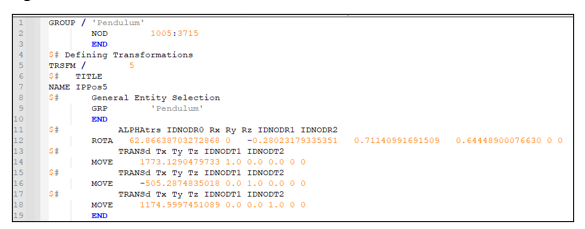
Finally, the positioning file is automatically added as an include file in the Main File. The resulting model files for each impact location look as follows:
- AP1_left.k
- FMH_2.0.k
- Positioning_AP1_left.key
- AP1_left_0000.rad
- FMH_2.0_0000.rad
- Positioning_AP2_left_0000.rad
- AP1_left.pc
- FMH_2.0.inc
- Positioning_AP1_left.inc