OS-E: 0855 Reliability-based Topology Optimization of a Plate
A Reliability-based Topology Optimization (RBTO) of a 2D plate is demonstrated, using OptiStruct.
RBTO is a subset of Reliability-based Design Optimization (RBDO), which can be used to provide optimum designs in the presence of uncertainty. A two-phase approach is implemented in OptiStruct to solve RBDO problems efficiently, while preserving accurate reliability assessment of the final design. The design variables, constraints, and objective are tested for reliability based on user-defined reliability requirements.
The objective is to conduct a Reliability-based Topology Optimization of the 2D plate which is undergoing vertical loading (force applied in negative Y-direction). Design space is in blue in Figure 1.
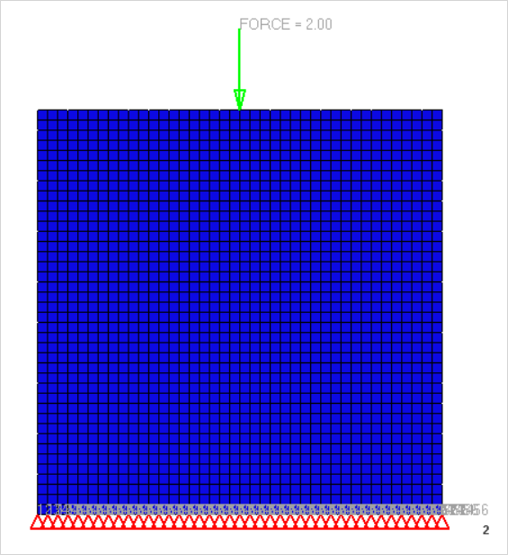
Model Files
Model Description
The DVLREL1 entry is used to define loading in the X-direction as a designable load. The DESVAR entry defines the DVLREL1 loading as a random design parameter (normal distribution with standard deviation of 0.3). The presence of Random input loading in the X-direction drives the design to account for this randomness. Additionally, the objective is to minimize compliance with a probability of 95% reliability, and the volume fraction is constrained to 0.3.
Random Parameters and Random Design Variables are two options that are available for design variables to include the effect of randomness. The Random Parameters option is activated by using RANP continuation line on the DESVAR entry and the Random Design Variables option is activated using the RAND continuation line on the DESVAR entry. In this problem, use the RANP continuation line to identify that the Loading in the X-direction is a random parameter. The difference between Random Parameter and Random Design variable options is that for RANP, the randomness of the design variable is accounted for from its specified initial value or mean. The mean value will not change during the optimization process. Whereas, for RAND, the design variable mean value is also varied in addition to accounting for the randomness (similar to RANP). In this example, the RANP option is used to only account for the randomness of the X-direction load.
The presence of 95% reliability probability setting for the compliance implies that you are trying to minimize the 95 percentile value of the compliance distribution obtained based on your randomness in the X-direction load. For more information, refer to Reliability-based Design Optimization in the User Guide.
Additionally, a Deterministic Topology Optimization run is also performed wherein the random parameters are excluded.
- Element Types
- CQUAD4
- Property
- Value
- Young's Modulus
- 2.1E7 PA
- Poisson's Ratio
- 0.3
Results
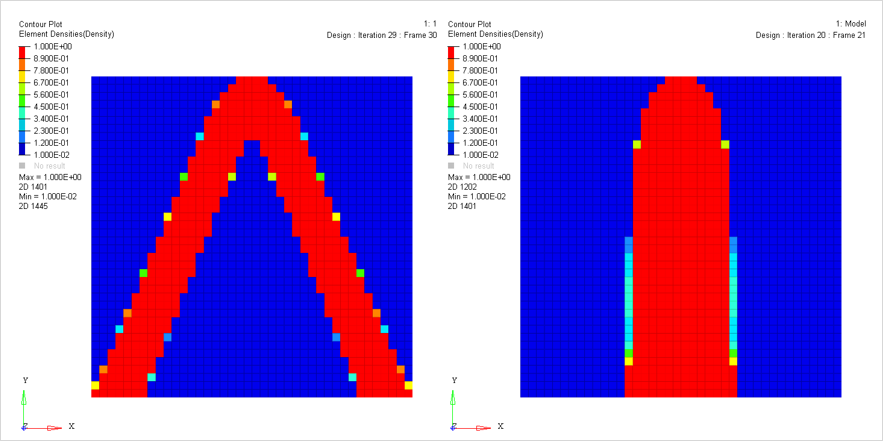