Calibration of Indoor Propagation Models
WinProp allows the automatic calibration of nearly all available propagation models based on measurement data. Additionally some propagation models support the calibration of material properties and of clutter / land usage databases. The following table shows an overview of the models and the features:
Scenario | Model | Material calibration | Clutter calibration |
---|---|---|---|
Indoor | One slope model | no | not applicable |
Motley Keenan model | no | not applicable | |
COST 231 model | yes | not applicable | |
Dominant path model | no | not applicable | |
Standard ray-tracing | yes | not applicable | |
Intelligent ray-tracing | yes | not applicable | |
Urban | Knife edge model | no | not applicable |
Dominant path model | no | not applicable | |
Intelligent ray-tracing | no | not applicable | |
Rural | Empirical two way model | n/a | yes |
Deterministic two ray model | n/a | yes | |
Dominant path model | n/a | no |
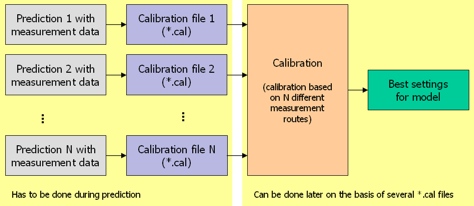
During the prediction, calibration files are written to the hard disk. The calibration is done afterwards based on the calibration files (.cal).
Generation of WinProp Measurement Files
Measurement files in WinProp file format (.fpp, .fpl, .fpf) have to be created prior to the calibration. This means the raw measurement data has to be imported from simple ASCII files into the WinProp software. See Import Prediction Data for more information.
Assignment of Measurement Files to Transmitters
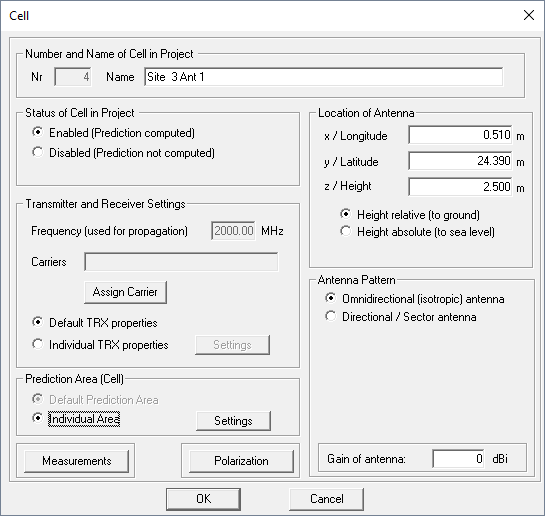
The Measurements button is used to assign a measurement file
(.fpp, .fpl, .fpf
files are supported) to the selected transmitter. The measurement file must contain
measured data from the selected transmitter only. Superposed measurement data from
several transmitters is not supported. When the measurement data is in path loss
format (.fpl) cable loss must not be included. In contrast to
this, cable loss is expected as included
when measurement data is available
in field strength or power file format. Antenna gain is always expected as
included
.
Computation of Propagation Prediction
After the assignment of the measurement files to the transmitters is completed, the wave propagation prediction can be launched as usual. The propagation paths output needs to be activated, otherwise no .cal files will be generated.
For each transmitter (with measurement data assigned) a calibration file (.cal) is written to the hard disk. If the files are missing, click the Prediction tab, under Additional Prediction Data... and select the Propagation Paths check box.
Calibration Computation
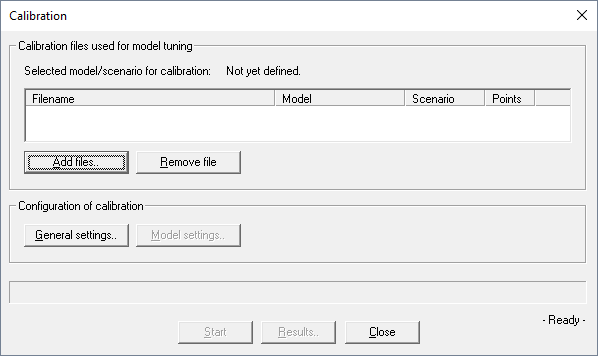
Files can be added by clicking Add files. They can be deleted by clicking on Remove file.
The settings can be adapted to your needs by clicking General settings. This allows you to influence the selection of the measurement points, for example, only points in a given power (dBm), path loss (dB) or distance (m) range will be considered.
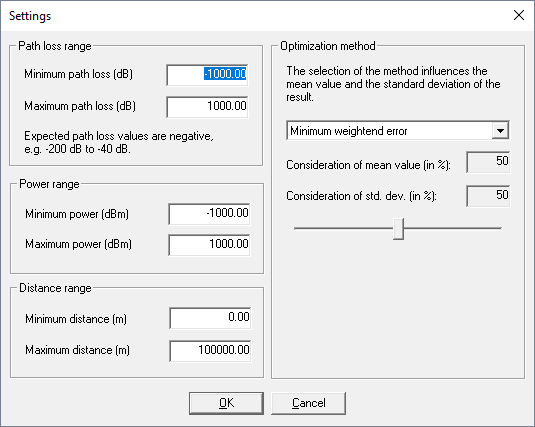
- Minimum mean error: The goal of the optimization is to achieve a minimum mean error (nearest to zero). The standard deviation is not considered and as a result might be larger.
- Minimum mean squared error: The goal of the optimization is to achieve a minimum mean squared error. The standard deviation is not considered and as a result might be larger.
- Minimum standard deviation: The goal of the optimization is to achieve a minimum standard deviation. The mean error is not considered and as a result might be larger.
- Minimum weighted error: The goal of the optimization is to find the best combination of minimum mean error and minimum standard deviation. The weighting between mean error and standard deviation can be modified.
The range of the model parameters can be defined in the Model settings tab. As larger the range is, as longer the calibration will take. The model parameters depend on the selected propagation model (each model offers individual model parameters).
Depending on the propagation model the material database or the clutter/land usage database can be calibrated additionally.
After clicking on Start, the calibration begins and the progress is shown with a progress bar. In some cases the calibration process does take up to 1 hour.
Calibration Result

The model parameters listed in the table can now be transferred manually into the project settings of ProMan and the project can be recomputed to achieve better results based on the new model parameters. By clicking on Apply, the material properties (as far as they have been calibrated) are applied to the vector / material database.
The message box shown above gives also information about mean value and standard deviation from measurements to predictions before and after the calibration. Depending on the optimization method different results can be obtained.