Defining VTS Data, Billet Taper, HTC, and Symmetry BC
Use the Process Data tool to define the variable time step (VTS) data, billet taper, and heat transfer coefficient.
Defining the Variable Time Step Automatically
- Ram speed
- Ram acceleration time
- Upset billet length
- Butt length
-
From the Extrusion ribbon, Process Data tools, click VTS.
The Time Step Data dialog is displayed. - In the Billet Length field, set the length of the upset billet. This value should match the length of the billet created. You can measure and verify this.
- In the Butt Length field, set the length of the butt. This value is typically 1-inch. For shorter billets, if actual value is not known, use 1-inch or 10% of the billet – whichever is smaller. For example if the billet length is only 5 inches, specify 0.5 in as the butt length.
- In the Ram Speed field, enter the speed at which the punch (also referred to as dummy block or ram stem) moves.
- Select either Auto or Manual for the Time Step. Auto is preferred.
Defining the Variable Time Step Manually
The Manual option in the Time Step Data dialog is used to control and change the time step for a transient problem. This allows you to define up to five different time step sizes during the cycle (referred to as zones).
Inspire Extrude automatically estimates the cycle time. You can reduce this cycle time to solve for less than full cycle analysis.
-
From the Extrusion ribbon, Process Data tools, click VTS.
The Time Step Data dialog is displayed. - In the Billet Length field, set the length of the upset billet. This value should match the length of the billet created. You can measure and verify this.
- In the Butt Length field, set the length of the butt. This value is typically 1-inch. For shorter billets, if actual value is not known, use 1-inch or 10% of the billet – whichever is smaller. For example if the billet length is only 5 inches, specify 0.5 in as the butt length.
- In the Ram Speed field, enter the speed at which the punch (also referred to as dummy block or ram stem) moves.
- Select Manual for the Time Step.
- To reduce the number of cycle times, enter a new value.
-
Select the number of time zones.
- For each time zone, you can change only the End Time and Num Of Steps. The rest of the data is automatically computed.
-
Click OK.
The following image shows how the time step size in four zones in the table above correspond with the load curve. When the solver is computing the solution, between 0 – 5.0 s, it uses a time step size of 1 second. That is, you will be able to inspect the solution in the post-processor after every second. Then between 5.0 and 15.0 second, it will advance the time in 2 s steps. That is, it will move from 5.0, 7.0, 9.0, 11.0., 13.0, and 15.0. In the same way for the remaining two time zones it will 2.5 and 3.0 s as time step sizes. Inspire Extrude allows you to have from 1 to 5 time zones in defining the time step. It should be noted that the quality of the solution computed is not affected by the size of the step.
Setting Up the Billet Taper
- Axial taper
- Lateral taper
- Radial taper
-
From the Extrusion ribbon, Process Data tools, click Billet
Taper.
The Billet Taper Data dialog is displayed. -
In the Cycle No column, specify the number cycles to
perform the analysis. Inspire Extrude limits the number of cycles to
a maximum of 5.
However, the solver places no limit on this value for simulation. Solvers have a limit that is based on different starter billets and tapers that can vary from cycle to cycle. Taper data used for cycles 1 to 5 can be different from each other; after that, the solver will use the 5th cycle data for rest of the cycles. Computational time for each cycle will be approximately five times the CPU time of steady state analysis, which should be kept in mind when doing a large multi-cycle analysis. In this release, if you would like to do more than 5 cycles, you will have to manually modify the *.hx file and increase this parameter.
- Complete the rest of the fields as required.
- Click OK.
Billet Taper Examples
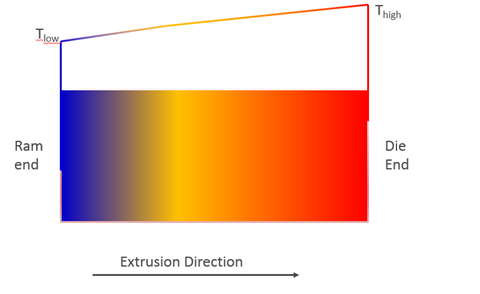
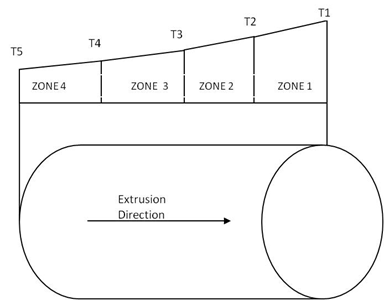
Lateral Taper
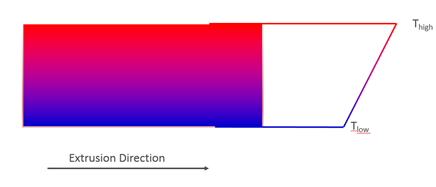
Radial Taper
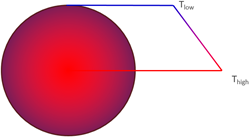
Defining Heat Transfer Coefficient
Select faces to specify heat transfer boundary conditions.
-
From the Extrusion ribbon, Process Data tools, click the HTC
tool.
-
Select a surface to apply the HTC boundary condition.
Press Ctrl and click surfaces on the model to add or remove boundary conditions by toggling between selected and unselected.
-
Enter the values in the microdialog to assign its heat
transfer properties.
Note: Apply the HTC on either selected surfaces or the entire part. If you select Part, the HTC will be applied on all of the surfaces of the part.
Defining Symmetry Boundary Conditions
Symmetry is used for specifying the symmetry planes.
-
From the Extrusion ribbon, click the Process
Data icon.
-
Click Symmetry.
-
Select the Symmetry surfaces