OS-T: 6100 Seam Weld Fatigue with RPC-based Load History Input using Fatigue Process Manager (FPM)
The method is a hot-spot stress approach applicable to thin metal sheets.
Hot spot stress is calculated from grid point forces at weld line. The method showed a good agreement with laboratory test results for sheet thickness between 1.0 mm and 3.0 mm. The method typically requires two SN curves. One is a bending SN curve which is dominated by bending stress, and the other is a membrane SN curve which dominated by membrane stress.
- Modeling seam welds uses a CQUAD4 element formulation.
- “Volvo Method” or “Hot Spot” Stress approach is used to calculate the hot spot stress from the nodal force at weld line.
- Force equilibrium at weld line holds true regardless of weld shape.
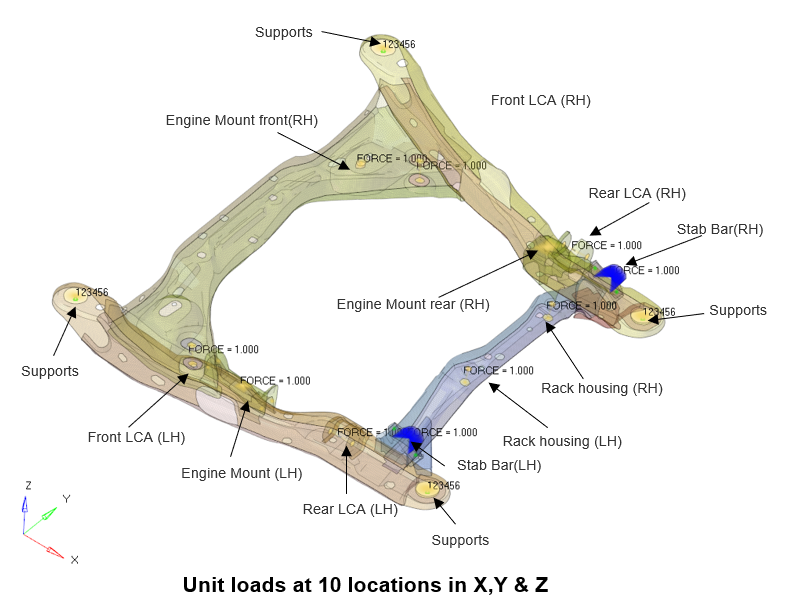
- Launch Fatigue Process Manager
- Import a model
- Create fatigue subcase
- Define fatigue analysis parameters
- Define fatigue elements and SN properties
- Define load-time history and loading sequence
- Submit the job
- View results summary and launch HyperView for post-processing
Launch HyperMesh and Set the OptiStruct User Profile
The model being used for this exercise is that of an automotive frame (Figure 1). The input file consists of 3 static loadsteps to which the frame is subjected to – Frontal torsion, Rear torsion and the Vertical bending.
-
Launch HyperMesh.
The User Profile dialog opens.
-
Select OptiStruct and click
OK.
This loads the user profile. It includes the appropriate template, macro menu, and import reader, paring down the functionality of HyperMesh to what is relevant for generating models for OptiStruct.
- Click .
- For New Session, enter a name in your working directory folder.
-
Click Create.
This creates a new file to save the instance of the currently loaded fatigue process template.
Import the Model
-
Click
.An Import tab is added to your tab menu.
- For the File type, select OptiStruct.
-
Select the Files icon
.
A Select OptiStruct file browser opens. - Select the cradle_seamweld_fatigue_startup.fem file you saved to your working directory.
- Click Open.
-
Click Import, then click Close to
close the Import tab.
The outline of the Fatigue Analysis setup to be achieved in the following steps.
Figure 2. Fatigue Setup - Fillet Seam Welds
Set Up the Model
Create Fatigue Subcases
Make sure the task Fatigue Subcase is selected in the Fatigue Analysis tree.
- In the Create new fatigue subcase field, enter Fatigue_SeamWeld.
- Click Create.
-
For the Select existing fatigue subcase, select the newly created fatigue
subcase Fatigue_SeamWeld.
Fatigue_SeamWeld is selected as the active fatigue subcase. Definitions in the following processes (analysis parameters, fatigue elements and properties, loading sequences, etc.) will be for this subcase.
-
Click Apply.
This saves the current definitions and guides you to the next task Analysis Parameters of the Fatigue Analysis tree.
Define Fatigue Parameters
- In the Model Browser, right-click and select .
- For Name, enter fatparam.
- For Card Image, select FATPARM.
- Verify TYPE is set to SN.
- Set STRESS COMBINE to SGVON (Signed von Mises).
- Set STRESS CORRECTION to GOODMAN.
- Set STRESSU to MPA (Stress Units).
- Set RAINFLOW RTYPE to LOAD.
- Set GATEREL to 0.0.
- Set CERTNTY SURVCERT to 0.001.
-
Check the box beside SMWLD and select the following options:
METHOD = VOLVO
Mean Stress Connection = NONE
SURVCERT = 0.0
THCKCORR = YES
-
Click Apply.
This saves the current definitions and guides you to the next task Elements and Materials of the Fatigue Analysis tree. For details, refer to the Altair HyperWorks 2024 help.
Define Fatigue Elements and Materials
Make sure the task Elements and Materials is selected in the Fatigue Analysis tree.
-
Click Add Material.
A Material Data window opens.
Figure 3. Material Data Definition
- For Material name, select Steel_Base_material_340Mpa_SAE960X.
- Verify that Stress unit is set to MPA.
- For UTS, enter 600.
-
Check box next to Seam Weld Material Properties and then click Seam
Weld Material Properties.
The Seam Weld Material Properties dialog opens.
-
Enter the values for Mean Stress Sensitivity, MSS2, Structural SN Curve along
with bending and membrane SN curve material values, as shown below.
Figure 4. Seam Weld Material Definition
- Click OK to close the Seam Weld Material Properties dialog.
- Click Save to save and close the Material Data dialog.
Define Properties
-
Click Add Property.
A Property Data window opens.
-
For Property Type, select Property-PSHELL.
Figure 5. Fatigue Property Data
- Click Close.
Define FATSEAM Load Collector
FATSEAM helps to select the seam weld type.
In this case it is the fillet weld.
- In the Model Browser, right-click and select .
- For Name, enter FATSEAM_OVRLAP_1.
- For Card Image, select FATSEAM.
- Set WTYPE to OVLAP.
- Set NUM_FATSEAM_PSHELL_PIDS to 7.
-
Click the table icon
next to Data: PID and select 7 different PSHELL IDs for all the 7 PID rows in the table, in the pop-out window.
- Click Close twice to close the table dialog, as well as FATSEAM dialog.
-
Follow the steps above to create 4 more FATSEAM cards, as
shown in the images below. The FATSEAM cards can be named as: FATSEAM_OVERLAP_2,
FATSEAM_FILLET_1, FATSEAM_OVERLAP_3 and FATSEAM_OVERLAP_4
Note: Confirm WTYPE is set to FILLET when defining the FATSEAM_FILLET_1 card.
Figure 6. FATSEAM (FATSEAM_OVERLAP_1) Definition
Figure 7. FATSEAM (FATSEAM_OVERLAP_2) Definition
Figure 8. FATSEAM (FATSEAM_FILLET_1) Definition
Figure 9. FATSEAM (FATSEAM_OVERLAP_3) Definition
Figure 10. FATSEAM (FATSEAM_OVERLAP_4) Definition
Define PFATSMW Property
- In the Model Browser, right-click and select .
- For Name, enter PFATSMW.
- For Card Image, select PFATSMW.
- Set BRATIO to 0.6.
- Set TREF to 1.1.
- Set TREF_N to 0.1.
- Click Close.
Update FATDEF Cards
-
Click Update next to FATDEF.
The FATDEF Entity Editor dialog opens.
- Verify that the FATSEAM option is checked and FATDEF_FATSEAM_NUMIDS= field is set to 5.
-
Click the table icon
next to Data: FATSEAMID and from property selector, select the property PFATSMW for all FATSEAMID, as shown below.
Figure 11. FATDEF Dialog
- Click Close to close the FATDEF dialog.
- Click Close button to close the Property Data dialog.
Load Time History Definition
Make sure the task Load-Time History is selected in the Fatigue Analysis tree.
- Toggle check box next to Read RPC & DAC files using ASSIGN.
-
Click Read RPC & DAC files using ASSIGN.
A dialog pops up.
- For Time series folder, select the directory where the RPC files are located.
-
Enter the values, as shown below.
Figure 12. Read RPC using ASSIGN Card Dialog
-
Click Apply.
This creates two include files (one with ASSIGN cards and the other with FATLOAD and FATEVENT cards) in the output folder for all the channels in all RPC files in the selected Time series input folder.Note: The RPC and DAC files are now supported in FPM. You must make sure to use HyperMesh Desktop application for this.
Load Sequences Defintion
This step is not required to be defined since FATLOAD and FATEVENT definition was defined using ASSIGN cards in the previous step.
Define FATPARM1 Load Collector
This step is required since it is not possible to define seam weld options for EN method in fatigue process manager template currently.
-
In the Model Browser, expand Load
Collector, click on the FATPARM1
material.
The Entity Editor opens.
- Set type to EN.
- Set MAXLFAT to NO or blank.
-
Verify the following are set:
- COMBINE is set to SGVON.
- UCORRECT is set to SWT.
- PLASTI is set to NEUBER.
- SURFSTS is set to blank.
-
Verify the following:
- SMWLD check box is ON.
- METHOD is set to VOLVO.
- UCORRECT and THCKCORR are set to OFF.
Define Output Requests
Before exporting the Solver deck, select the output request first. Follow the steps below.
-
In the Model Browser, expand Load
Steps, select Fatigue_Seamweld.
The Entity Editor opens.
- Select check boxes for OUTPUT > DAMAGE.
- Set FORMAT to H3D.
- Set TYPE to EVENT.
-
Set OPTION to ALL.
This will write out damage results for each event in the h3d results file.
- Similarly, select check box for LIFE under OUTPUT option under fatigue load step.
- Set FORMAT to H3D.
- Set OPTION to ALL.
Submit the Job
Make sure the task Submit Analysis is selected in the Fatigue Analysis tree.
- From the Analysis page, enter the OptiStruct panel.
-
Click save as following the input file field.
The Save As dialog opens.
-
For File name, enter the name cradle_seamweld_fatigue_export.fem.
Note: Make sure to select the same directory where ASSIGN and FATLOAD include files were written out above.
- Click Save.
-
Click OptiStruct to submit
the analysis.
An FYI dialog pops up. As per the message, the Solver deck will be exported, and the session will be cleared.
Define FATSEQ Load Collector
It is required to update the FATSEQ card with number of repetitions (N#) for each fatigue event created.
- Open the exported Solver deck in a text editor, or
- Import it back into HyperMesh
When updating the FATSEQ card in an HyperMesh session, follow the below steps.
- In a new session, import the OptiStruct Solver deck (exported in previous step) by selecting Include files set to “Merge”.
-
In the Model Browser, expand Load
Collector and select the FATSEQ1 card.
The Entity Editor opens.
-
Click the table icon
next to Data: FID and enter appropriate Repeat value N for all fatigue events, as shown below.
Figure 13. FATSEQ Card Update Dialog
Export Solver Deck
If you are using OptiStruct version 2019.1 or below, then you must edit the exported Solver deck before submitting the job. Remove “NORMAL” string from SMWLD line under each MATFAT.
-
Export a final OptiStruct solver deck.
This exported file is ready for job submission.
- Upload Solver deck along with all RSP files for job submission, if you plan to run the job on an HPC cluster.
Post-Process
Once the job is completed successfully, check the directory to make sure the .out and .h3d files are available.
- Load the results file (.h3d) into HyperView to post-process.
- Select Subcase 71 (Fatigue_SeamWeld) from the subcase dropdown.
- Go to the Contour panel and select Damage result type.
-
Click Apply.
Figure 14. Damage Contour in HyperView