Couple MotionSolve with EDEM
MotionSolve can interface with Altair EDEM, a state-of-the-art bulk material simulation tool.
EDEM is based on the Discrete Element Method (DEM), a numerical method that computes the motion and effect of a large number of small particles. It is commonly used to model the bulk behavior of granular materials. The method assumes that the material consists of separate, discrete particles. These particles may have different shapes and properties.
- Bulk materials in storage silos, like cereal.
- Granular matter, like sand.
- Powders, like toner.
- Blocky or jointed rock masses.
See the Altair EDEM documentation for more information about this method.
The Value of Discrete Element Simulation in MotionSolve
- Design systems that include complex interactions with bulk material.
- Accurately predict forces acting on equipment interacting with bulk materials.
- Predict component durability using the computed forces.
- Identify excessive wear zones on equipment.
- Optimize material distribution and detect “dead zones”.
- Quantify system power requirements.
- Understand vehicle behavior on soft soil.
- Evaluate traction control system on soft soil.
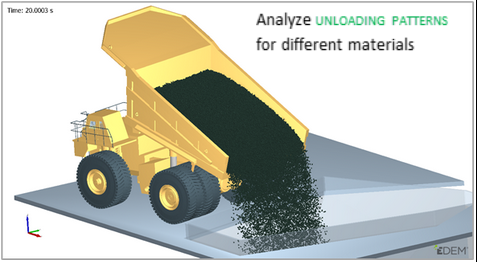
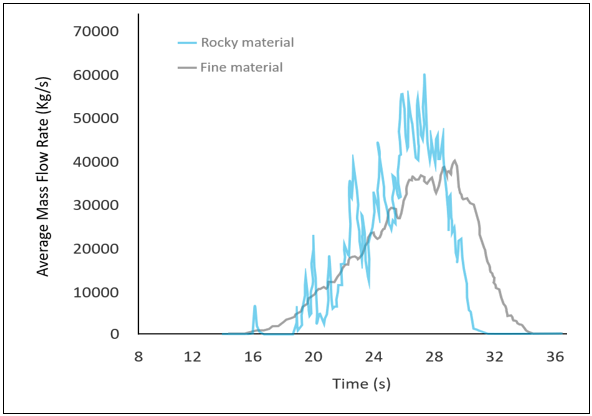
Implement Coupling
The coupling between MotionSolve and Altair EDEM is achieved via co-simulation between the two products. In this co-simulation, MotionSolve models the mechanical system interacting with the bulk material. For example, this could be earth moving machinery or an ATV going over sandy terrain. EDEM, on the other hand, models the bulk material. Both products run in separate processes so you can run them on the same or different machines. Cross-platform is supported as well, meaning MotionSolve can run on Windows while EDEM runs on the Linux operating system and vice versa. Socket (TCP/IP) is used as the communication methodology when MotionSolve and EDEM run on two different machines. A PIPE or Socket is used as the communication methodology when MotionSolve and EDEM run on the same machine.
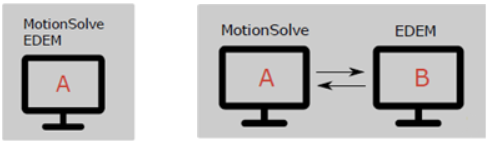
MotionView can be used as a user interface to set up a coupling between MotionSolve and EDEM more intuitively. More information on how to use MotionView for the MotionSolve and EDEM coupling can be found in the Bulk Material Interaction and EDEM Menu topics. The tutorial MV-7021: MotionSolve/EDEM Co-Simulation explains how to set up and run the MotionSolve and EDEM co-simulation.
The basic structure of the interaction between MotionView, MotionSolve, and EDEM is shown in below.
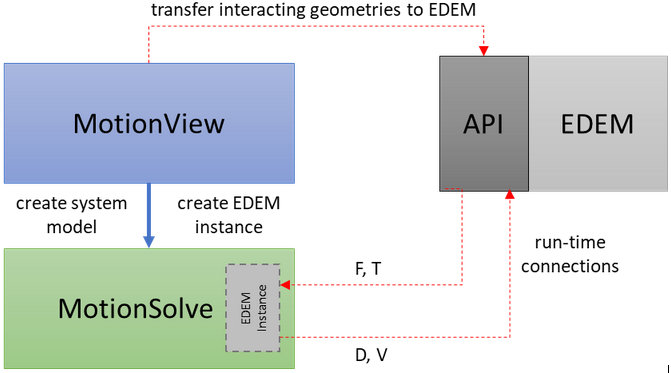
The EDEM solution has a dedicated API that MotionView and MotionSolve communicate with to establish a coupling.
In MotionView, you can select a set of geometries or bodies that should interact with the bulk material. Rigid and CMS-based flexible bodies are supported. The geometries or bodies are then transferred to EDEM and imported as one or more EDEM instance(s) into a MotionSolve system model. For flexible bodies, a triangularized mesh from the body (skin) surface is being used. Then, at run-time, the MotionSolve system model communicates to EDEM. At each point in time, MotionSolve provides EDEM the position and velocities of the selected bodies (both rigid body and nodal in the case of flexible bodies). In response, EDEM returns the forces exerted by the bulk material on the various bodies that interact with the bulk material. For rigid bodies, EDEM sums all particle forces and torques acting on each body and returns the net force and torque acting at the center of mass coordinate system of each interacting body. For flexible bodies, MotionSolve converts the mesh nodal particle forces and torques into modal forces and applies them to each interacting body. The coupling also supports co-simulation with the Pratt-Miller Flex Tire in EDEM. Please reach out to the Altair Partner Alliance for more information on the Pratt-Miller Flex Tire in EDEM.
Applications of MotionSolve and EDEM Co-simulation
MotionSolve, together with the Altair EDEM, can be used in a variety of industries for many applications. Four applications in diverse industries are presented below.
Operational Behavior of Heavy Equipment
- Dump truck bodies
- Excavators and diggers
- Grab buckets and more
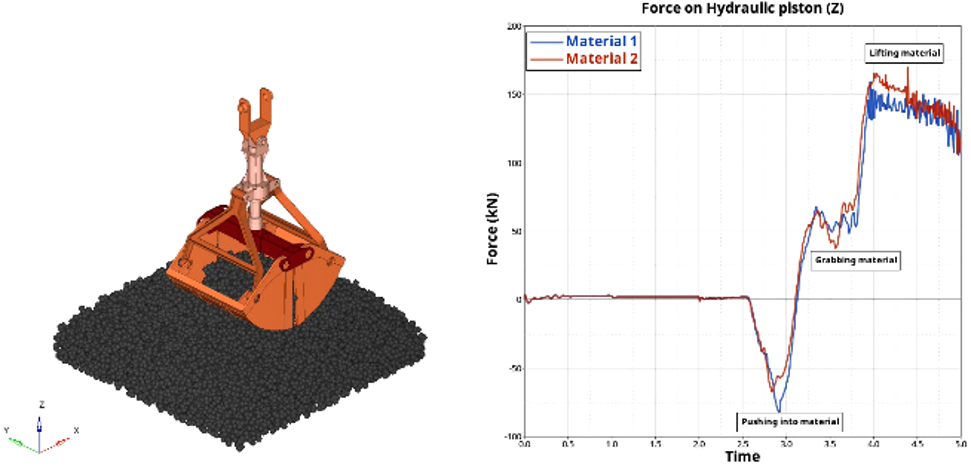
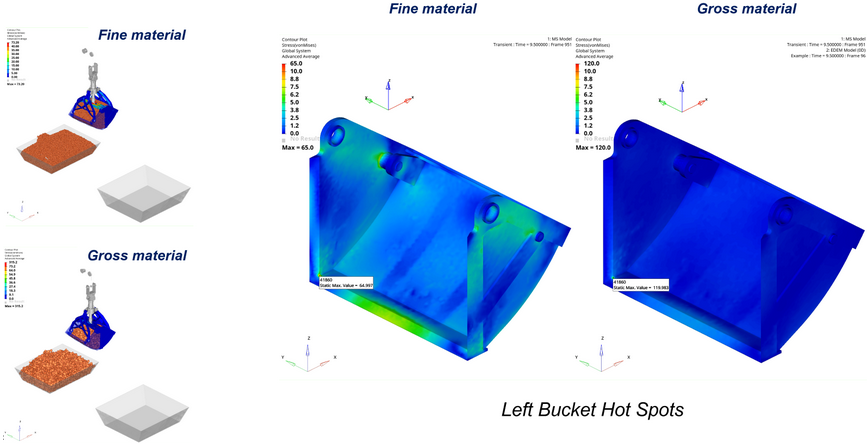
Mining and Construction
- Transfer chutes
- Bucket conveyor systems
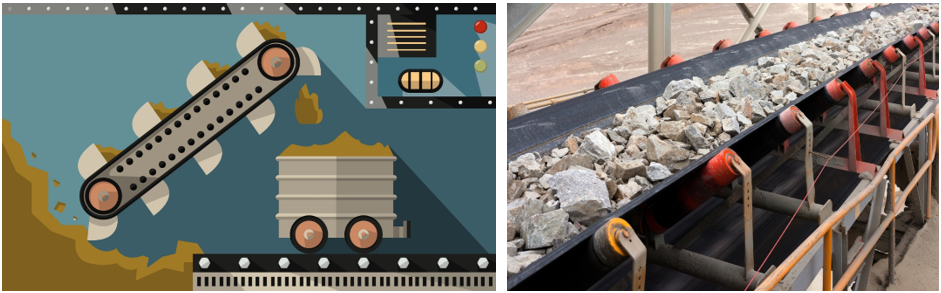
Agricultural Machinery
- Combine harvesters
- Feeders
- Tractors and tillage equipment
- Tire–soil interaction
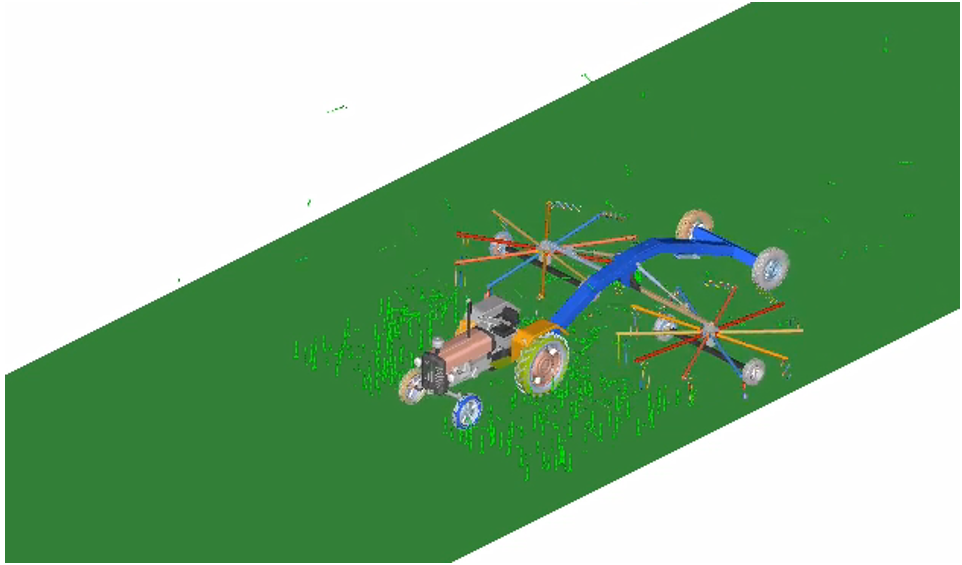
Pharmaceuticals and Chemicals
- Hopper discharge with bridge breakers
- Powder raking and spreading
- Wet mixing of aggregate fractions
- Dry mixing of aggregate fractions
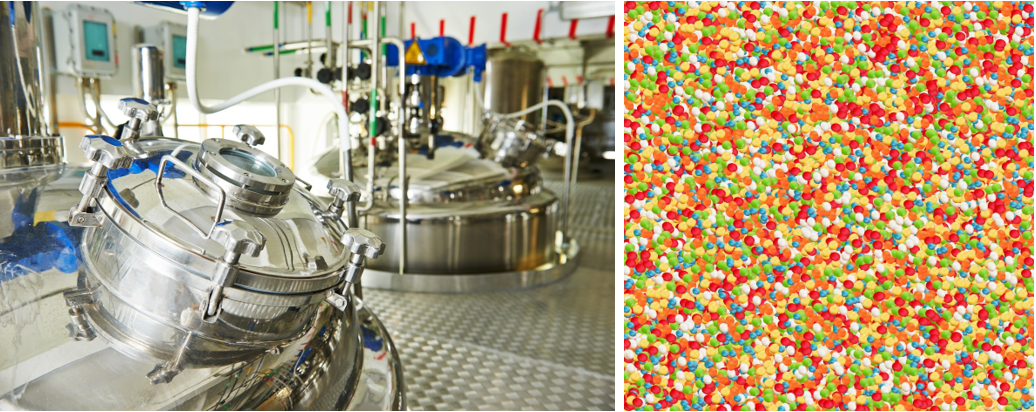