ACU-T: 6105 Single Particle Sedimentation – Effect of Lift and Torque
Tutorial Level: Intermediate
Prerequisites
This tutorial demonstrates the effect of lift and torque forces on a non-spherical particle falling through a fluid using AcuSolve-EDEM bidirectional coupling. Prior to starting this tutorial, you should have already run through the introductory tutorial, ACU-T: 1000 Basic Flow Set Up and ACU-T: 6100 Particle Separation in a Windshifter using Altair EDEM, and have a basic understanding of HyperMesh CFD, AcuSolve, and EDEM. To run this simulation, you will need access to a licensed version of HyperMesh CFD, AcuSolve, and EDEM.
Problem Description
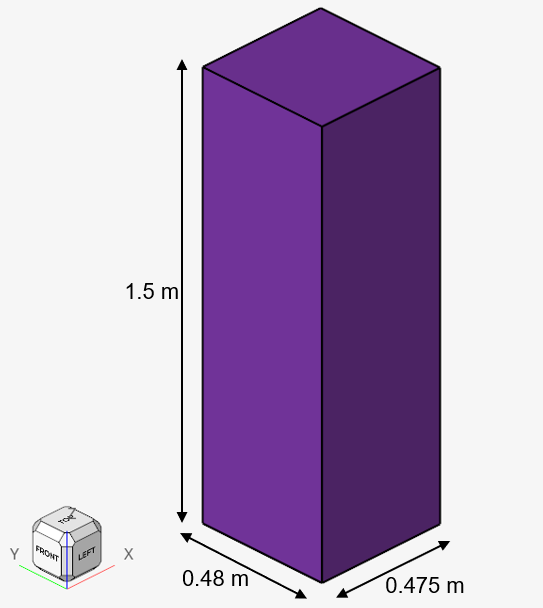
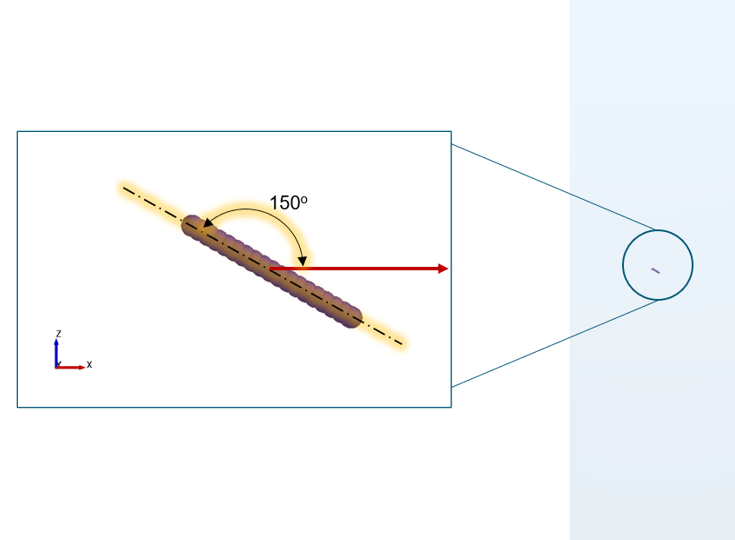
AcuSolve-EDEM bidirectional coupling is used to model the interaction between the fluid and particle. In this tutorial, the Rong drag model in conjunction with the Ganser non-spherical drag-coefficient model is used such that the effect of non-spherical shape is considered. The length scale used for factoring in the shape of the particles is the aspect ratio. A cylindrical particle with an aspect ratio of 9.242 (L/D = 0.05 m/0.00541 m) is used for this simulation.
This tutorial also introduces you to the concept of generating particles in EDEM at a specific location and with a specific orientation. When defining the particle factory, you have the option to define certain properties of particles such as velocity, angular velocity, position, orientation, temperature, and so on. Properties such as orientation and position can be defined by you or set to random. The steps listed below illustrate the general process for calculating the orientation matrix required in EDEM for creating particles with a specific orientation.
- Generating particles at a certain orientation requires an orientation matrix that transforms the particle relative to the initial orientation specified during the particle shape definition. For rotation about an axis ( ) by an angle ( ), the orientation matrix ( ) is given by
-
- Where,
and a, b, c are the components of the unit
vector of the axis of rotation,
.Note: The right-hand thumb rule is used for determining the sign of the angle of rotation where the thumb points towards the axis of rotation and the curl of the fingers points towards the positive direction of the angle of rotation.
- In the current example, the particle should be rotated by an angle of 30o about the y-axis. Therefore, =30o, =0.133974596, a=0, b=1 and c=0. By substituting these values, you get the following orientation matrix:
-
-
Figure 3.
Part 1 - EDEM Simulation
Start Altair EDEM from the Windows start menu by clicking .
Open the EDEM Input Deck
- From the menu bar, click .
-
In the dialog, browse to your problem directory and open the
cylinder.dem file.
The geometry and the materials are loaded.
Figure 4.
Review the Bulk Material and Particle Shape
In this step, you will define the material models for the bar and sphere-shaped particles.
- In the Creator Tree, expand .
-
Click cylinder and verify that the properties are set as
shown below.
Figure 5.
-
Click Properties under New particle 1.
Observe that the particle shape is created using multiple spheres aligned along the x-axis.Note: When defining non-spherical shapes, you need to make sure that the principal axis of the particle is aligned with the x-axis, as shown in the figure below.
Figure 6.
The length (L) and diameter (D) of the particle are 0.05 m and 0.00541 m respectively. Therefore, the aspect ratio (= L/D) of the particle is 9.242.
-
Observe the mass and volume of the particle in the Creator Tree.
Figure 7.
Define Geometries and Factories
- In the Creator Tree, expand Geometries.
-
Click Tank and verify that the type is set to
Physical.
Figure 8.
- Right-click Tank and select Add Factory.
- Right-click New Factory 1 and select Change Factory Type.
-
Verify that the Factory Type is set to static and set the particle generation
parameters as shown in the figure below.
Figure 9.
-
Under Parameters, set the Position option to cubic and
then click
.
Figure 10.
-
In the dialog, enter the position parameters as shown in the figure below and
then click OK.
Figure 11.
-
Under Parameters, set the Orientation option to fixed
and then click
.
-
Enter the values for the orientation matrix as shown in the figure below.
Figure 12.
- Click OK.
Define the Environment
In this step, you will define the extents of the domain for the EDEM simulation and the direction of gravitational acceleration.
- In the Creator Tree, click Environment.
-
Activate the checkbox for Auto Update from Geometry (if
not already selected).
When a moving particle touches the bounding faces of the domain (environment), it will be removed from the simulation.
- Activate Gravity and set the z-value to -9.81 m/s2.
- Save the EDEM deck.
Define the Simulation Settings
-
Click
in the top-left corner to go to the EDEM Simulator tab.
- In the Simulator Settings tab, set the Time Integration scheme to Euler and de-activate the Auto Time Step checkbox.
-
Set the Fixed Time Step to 1e-5 s.
Note: Generally, a value of 20-40% of the Rayleigh Time Step is recommended as the time step size to ensure stability of the DEM simulation.
- Set the Total Time to 5 s and the Target Save Interval to 0.01 s.
-
Set the Cell Size to 2.5 R min.
Generally, a value in the range of 2-6 Rmin is recommended as the optimum cell size.
-
Set the Selected Engine to CPU Solver and set the Number
of CPU Cores based on availability.
Figure 13.
- Once the simulation settings have been defined, save the model.
Part 2 - AcuSolve Simulation
Start HyperMesh CFD and Open the HyperMesh Database
- Start HyperMesh CFD from the Windows Start menu by clicking .
-
From the Home tools, Files tool group, click the Open Model tool.
Figure 14.
The Open File dialog opens. - Browse to the directory where you saved the model file. Select the HyperMesh file ACU-T6105_cylinder.hm and click Open.
Validate the Geometry
The Validate tool scans through the entire model, performs checks on the surfaces and solids, and flags any defects in the geometry, such as free edges, closed shells, intersections, duplicates, and slivers.

Set Up Flow
Set the General Simulation Parameters
-
From the Flow ribbon, click the Physics tool.
Figure 16.
The Setup dialog opens. - Under the Physics models setting, select the Multiphase flow radio button.
- Change the Multifluid type to Bidirectional EDEM Coupling.
-
Click the Eulerian material drop-down menu and select Material
Library from the list.
You can create new material models in the Material Library.
-
In the Material Library dialog, select EDEM 2 Way
Multiphase, switch to the My Materials
tab, and then click
to add a new material model.
- In the microdialog, click EDEM Bidirectional Material in the top-left corner and change the name to Water-Particle.
- Set the Carrier field to Water.
- Set the Particle Shape to Non-Spherical.
- Set the Drag model to Rong.
- Set the Non spherical drag coefficient model to Ganser.
-
Click the table icon beside the drag coefficient model drop-down.
Figure 17.
-
In the new dialog, enter the values for Aspect Ratio and Volume as shown in the
figure below.
Figure 18.
Note: Since you have only a single type of particle in this simulation, you don’t need to specify the volume of the particle. But, in the case of multiple particles, the volume of each particle should be specified, which can be obtained from EDEM. - Press Esc to close the dialog.
- Set the Lift model to Nonspherical lift.
-
Set the Torque model to Pitching Rotational
Torque.
Figure 19. - Close the material model and Material Library dialogs.
- In the Setup dialog, set the Eulerian Material to Water-Particle.
- Set Time step size and Final time to 0.001 and 5, respectively. Select Spalart-Allmaras for the Turbulence model.
- Verify that Gravity is set to 0, 0, -9.81.
-
Set the Pressure scale to Absolute.
Figure 20.
-
Click the Solver controls setting and set the Maximum
stagger iterations to 2.
Figure 21.
- Close the dialog and save the model.
Assign Material Properties
-
From the Flow ribbon, click the Material tool.
Figure 22.
-
Verify that Water-Particle has been assigned as the material.
If not assigned, click the tank geometry and select Water-Particle from the microdialog.
-
On the guide bar, click
to exit the tool.
Define Flow Boundary Conditions
Since the domain doesn’t have any openings, there is no need to explicitly define a surface boundary condition as HyperMesh CFD assigns a no-slip wall boundary condition to all the surfaces by default.
Generate the Mesh
-
From the Mesh ribbon, click the
Volume tool.
Figure 23.
The Meshing Operations dialog opens. - Set the Mesh size to Average size and change the Maximum element size to 0.07.
-
Deactivate Curvature-based surface refinement and then
click Mesh.
Figure 24.
- Once the meshing process is complete, save the model.
Define Nodal Outputs
Once the meshing is complete, you are automatically taken to the Solution ribbon.
-
From the Solution ribbon, click the Field tool.
Figure 25.
The Field Output dialog opens. - Check the box for Write initial conditions.
- Uncheck the box for Write results at time step interval
- Check the box for Write results at time interval.
-
Set the Time step interval to 0.01.
Figure 26.
- Close the dialog and save the model.
Submit the Coupled Simulation
-
Start the coupling server by clicking Coupling Server in
EDEM.
Figure 27.
Once the Coupling server is activated, the icon changes.Figure 28.
- Return to HyperMesh CFD.
-
From the Solution ribbon, click the Run tool.
Figure 29.
The Launch AcuSolve dialog opens. - Set the Parallel processing option to Intel MPI.
- Set the Number of processors to 6.
- Expand Default initial conditions, uncheck Pre-compute flow and set the velocity values to 0. Uncheck Pre-compute Turbulence.
-
Click Run to launch AcuSolve.
Figure 30.
Once the AcuSolve run is launched, the Run Status dialog opens. -
In the dialog, right-click the AcuSolve run and
select View log file.
If the coupling with EDEM is successful, that information is printed in the .log file.
Figure 31.
Once the simulation is complete, the summary of the run time is printed at the end of the .log file.Figure 32.
Analyze the Results
AcuSolve Post-Processing
-
In HyperMesh CFD, right-click the AcuSolve run in the Run Status
dialog and select Visualize results.
Figure 33.
The results are loaded in the Post ribbon. -
Click the Slice Planes tool.
Figure 34.
-
Select the x-z plane as highlighted in the figure below.
Figure 35.
-
In the slice plane microdialog, click
to create the slice plane.
- In the display properties microdialog, set the display to volume fraction edem particle and activate the Legend toggle.
- Change the bounds of the legend to 0 and 0.001.
-
Click
and set the Colormap name to Rainbow Uniform.
Figure 36.
- Click the Vector Display tab.
- Activate the Display toggle and set the variable to velocity.
- Set the size to 0.05 and the Color to Constant.
-
Click
and set the Vector length to Uniform.
Figure 37.
-
Click
on the guide bar.
-
In the Post Browser, turn off the visibility of
Flow Boundaries by clicking on its icon.
Figure 38.
-
Select the Left face on the view cube to align the model
to the x-z plane.
Figure 39.
-
Click
on the animation toolbar to view the animation.
Figure 40.
EDEM Post-Processing
-
Once the EDEM simulation is complete, click
in the top-left corner to go to the EDEM Analyst tab.
- In the Analyst Tree, expand Tank. and then select
-
Verify that the Display Mode is set to Filled and set
the Opacity to 0.2.
Figure 41.
- In the Analyst Tree, click Particles.
- Set the coloring to Contact Default.
-
Click Apply All.
Figure 42.
-
On the menu bar, set the time to
0 by clicking:
Figure 43.
-
Set the View plane to + Y.
Figure 44.
-
In the Viewer window, set the Playback Speed to 0.2x and
then click
to play the particle flow animation.
Figure 45.
Observe that the particle rotates and translates as it falls down. Without lift and torque, you will not see this phenomenon.
Summary
In this tutorial, you learned how to set up and run a basic AcuSolve-EDEM bidirectional (two-way) coupling problem with non-spherical particles. You learned how to create particles in EDEM with a specific orientation and position. Next, you set up the AcuSolve model to consider the effect of the lift and torque forces. Once the simulation is complete, you learned how to post-process the AcuSolve results using HyperMesh CFD and EDEM.