Co-Simulating an SPM Motor with Flux 2D
Tutorial Level: Advanced Create a Twin Activate model that supplies a three-phase bridge current into a Flux 2D model of a Surface Mounted Permanent Magnet (SPM) motor, and co-simulate the models.
The co-simulation process includes four basic steps:
- Create a Flux model. For this tutorial, a Flux model of an SPM motor is provided for you.
- Generate the Flux coupling component required for Twin Activate to read in the Flux model data.
- Create a Twin Activate model and include the Flux block for reading in the Flux coupling component.
- Co-simulate the models in Twin Activate.
Files for This Tutorial
SPM_Activate_Regulation.F2STA (the coupling file exported from Flux), SPM_Activate_RegulationF2STA.FLU (the Flux model file), SPM_Regulation_No_load.scm (the Twin Activate model file)
Overview of the Flux SPM Motor
The Flux model is a brushless, AC, Surface Mounted Permanent Magnet motor applicable for electric vehicles.
- Fixed part (stator) including yoke, slots, and windings
- Air gap
- Moveable rotor with embedded magnets
The SPM motor is driven with a three-phase bridge current (the freewheeling diodes are neglected). The constant speed operation of the motor at 1000 rpm with inverter driver is simulated to yield motor torque, speed, position and phase current. The inverter switching scheme is rotor-position dependant.
The inputs for the SPM motor are defined as multi-physical parameters and include:
- I1: Physical quantities: μr, Bs, Br
- I2: Electrical quantities: resistance, voltage, current
- I3: Mechanical quantities: position, speed, resistant force, resistive torque
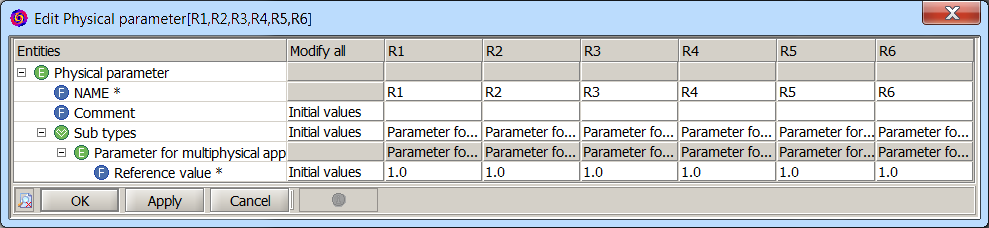
The outputs for the SPM motor are scalar I/O settings that retrieve values through the sensors, formulas (forces and couples) and parameters (position, speed, acceleration).
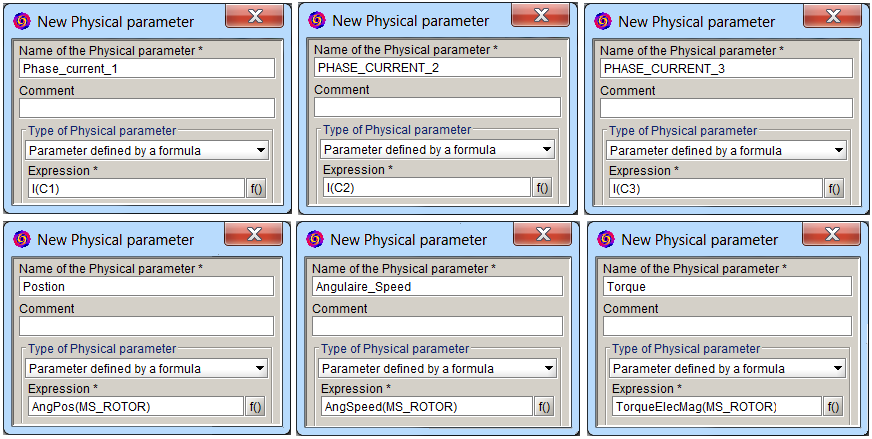
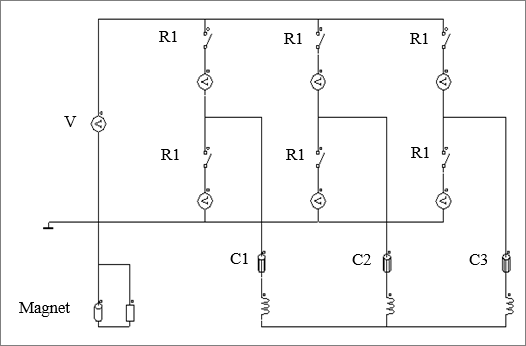
Generating the Coupling Component in Flux
Load the Flux model and generate the coupling component with the required inputs, outputs and parameters.
-
Launch Flux, and from your working directory, open the project,
SPM_Activate_Regulation.F2STA.
The model loads and looks something like this:
Figure 2. Cross-Section View of SPM Motor - From the Flux 2D toolbar, select .
-
In the dialog, enter the following information for the component:
- Enter the name for the component: SPM_Activate_Regulation.
- Enter the path to your working directory: <name_without_spaces>.
- Select the input (geometric I/O parameters) for the component: R1, R2, R3, R4, R5, R6.
- Select the output: PHASE_CURRENT_1, PHASE_CURRENT_2, PHASE_CURRENT_3, POSITION, SPEED and TORQUE.
The dialog should look something like this:
-
Click OK.
The coupling component is saved to your working directory as SPM_Activate_Regulation.F2STA.
Creating the Twin Activate Model
Create a model to feed a three-phase bridge circuit.
-
From Twin Activate, create a new model and save it to your working directory as
SPM_Regulation_No_load.scm
Alternatively, load the model: <installation_directory>/Tutorial Models/Flux_SPM/SPM_Regulation_No_load.scm and skip this section of the tutorial.
- From the Palette Browser, select , and drag and drop one Flux block into your diagram.
- Double-click the Flux block, and in the block dialog, for Flux to Activate input filename, enter the path to the coupling component you generated from Flux: <working_directory>/SPM_Activate_Regulation.F2STA.
-
Click OK.
The Flux block populates with the model data from the Flux coupling component.
-
On the Flux block dialog, do the following:
- For Numerical memory (MB), enter 2154.
- For Character memory, enter 200.
- For Minimal input variation %, enter 0.
- Select the options: Flux console display and Break algebraic loop.
-
Click OK.
The Flux block dialog should look something like this:
-
In the diagram, to the left of the Flux block, create a super block for
Position regulation:
Table 1. Blocks Required for Position Super Block Add these blocks to the super block Enter parameter values or keep default values as indicated 1 Constant block Default 1 Modulo block Function = Remainder 1 Input block Note: The Input block (Rotor position) feeds into the Modulo block.Outport size = [-1;-2] 1 LastInput block Default 2 Sum blocks Default 8 LookupTable blocks - For all 8 LookupTable blocks:
Y = [1,1]
Interpolation method = ZeroOrder (ceiling)
Output datatype = "double"
- For the X vector, enter:
block 1, X = [15,75]
block 2, X = [45,105]
block 3, X = [75,135]
block 4, X = [105,165]
block 5, X = [0,15]
block 6, X = [135,180]
block 7, X = [0,45]
block 8, X = [165,180]
2 Sum blocks Default 6 Output blocks Note: The Output blocks correspond to the 6 input ports "R1" through "R6" of the Flux block in the main diagram.Default Scope Default Assemble the blocks in the super block like this:Figure 3. Position Super Block - For all 8 LookupTable blocks:
-
In the diagram, add three Scope blocks to the right of the Flux block. The
Scope blocks plot the following results: current (A) in each phase, position and
speed, and torque.
Define Scope 1 Scope 2 Scope 3 Block name 2_1_2 2_1_2_1 2_1_2_1_1 Number of inputs 3 2 1 -
Assemble and connect the Flux co-simulation block, super block and scope blocks
as you see in the following figure, and save the model.
Figure 4. Flux Block Assembled with Inputs and Outputs The Twin Activate model is now complete and configured to supply the Flux model of the SPM motor with a three-phase bridge circuit. The Twin Activate model is also configured to calculate the phase current, position, speed and torque.
Co-Simulating the Twin Activate and Flux Models
During co-simulation, the Twin Activate model supplies a three-phase bridge current into the Flux model of the SPM motor. The simulation results show the performance of the SPM motor including position, speed and torque.
-
On the ribbon, select Setup.
- On the dialog that appears, select the Simulation Time tab.
- For Final Time, enter .01499, which is the signal period. Keep the defaults for the remaining fields.
-
Select the Solvers tab, enter the following values, and
click OK:
-
On the ribbon, select Run.
The simulation results show the currents fed into the motor and the motor performance.
Table 2. No Load Test with Constant Speed (N=1000 rpm) Property Value Unit Moment of inertia 0 Kg.m2 Constant friction coefficient 0 N.m Viscous friction coefficient 0 N.m s/deg Friction coefficient proportional to the square speed 0 Speed 1000 Tr/min Position at time 0 0 Deg Figure 5. Current (A) in Each Phase Figure 6. Position (deg/s) and Speed (rpm) Figure 7. Torque (N.m)