Explore Three Coupling Methods with Flux
Tutorial Level: Advanced Compare three coupling methods between Twin Activate and Flux using co-simulation, lookup tables and FMUs.
- Co-Simulation Method
- This is a dynamic approach in which Flux and Twin Activate run simultaneously to produce very accurate results at the cost of a longer run time. The co-simulation is initiated from Twin Activate between the Twin Activate model Actuator_Coupling.scm and the 2D transient magnetic Flux model MultiPhysics.FLU. The co-simulation is dependent on the kinematics that is defined in Flux 2D through the analysis option, multi-physics position. The Flux model provides values to the Twin Activate model including force, current and speed through the Flux block in the coupling component. In Twin Activate, the Flux block is defined to receive values for position and voltage as input.
- Lookup Table Method
- This approach includes two separate simulations: The first includes opening the FEA model Static_no_solved.FLU in Flux and running an analysis in magneto-static mode. Simulation results for Current, Position and Flux are produced as .oml script files. A second simulation is performed in Twin Activate where the Flux results are read in from the .oml script files by way of a Lookup Table ND in the Twin Activate model.
- FMU Method
- This approach includes two separate simulations: The first includes opening the FEA model Static_no_solved.FLU in Flux and running an analysis in magneto-static mode. Simulation results for Current, Position and Flux are exported as Functional Mock-up Unit files. A second simulation is performed in Twin Activate where the Flux results are imported from the .fmu files by way of an FMU Import block.
Files for This Tutorial
Primary files include: MultiPhysics.FLU (the Flux contactor model file), Actuator_Coupling.scm (the Twin Activate model file) and Static_no_solved.FLU (the Flux lookupND table)
Overview of the Flux Projects
The Flux projects with all of the required files for each of the simulation methods discussed in this tutorial are available from the Demo Browser: /Tutorial Models/Flux_Actuator/.
- Flux Applications
-
- Magneto Static
- Transient Magnetic
- Flux Main Functions
-
- Translation motion, Mechanical set (For more details, see Flux Supervisor examples in the Flux help)
- Kin. = multi-static application and multi-physics position
- Generate OML
- Generate Twin Activate coupled component
- Generate FMU
- Flux Post-Processed Quantities
-
- Magnetic quantities
- Kinematic quantities
- Circuit quantities
- 2D curve analysis
- Flux Contactor (Trident) Model
- The main Flux contactor model MultiPhysics.FLU is comprised of
three main components:
- A lower grip, ferromagnetic fixed part
- An upper grip, ferromagnetic (laminated) moving part assembled on springs
- A coil placed around the central tooth
- Python Files for Flux Projects
- The Flux project folders contain the completed Flux results for all three
simulation methods. If you want to experiment with launching the simulations on
your own or if you want to use your own coupling file, the Python files for you
to do so are available in the Flux projects for all three simulation methods:
- Co-simulation = Coupling_Component.py
- OML = Generate_OML.py
- FMU = Generate_fmu.py
Overview of the Twin Activate Model Files
- Twin Activate Coupling Model
-
Figure 1. Actuator_Coupling.scm
- Electric Circuit
- The purple CIRCUIT super block in the coupling model is comprised of four main
components:
- a controlled switch that opens and closes based on voltage
- a resistor that serves to prevent short circuiting
- a current and voltage input
- a voltage output sensor
- Regulation Command
-
A simple regulation command in the coupling model is included in the light green Hysteresis block. Here the model is dependent on the active regulation of time.
- Active Regulation
- In the red ACTIVE REGULATION super block, we compare two values and use this to
activate the Hysteresis regulation.
- Mechanical Equation
- The bright green super block, MECHANICS, includes Modelica blocks to simulate
the mechanical part of the device and position the actuator.
- ElectroMag Super Block
-
The ElectroMag super block (yellow) of the Twin Activate Coupling model (Actuator_Coupling.scm) contains the electromagnetic component of the model and consists of the Include Diagram block (red) and three additional super blocks: Cosimulation with Flux (blue), Lookup TableND from Flux (green) and FMU from Flux (pink) that you see in the following diagram. The Include Diagram block defines which super block to call into play depending on which simulation method you specify through the Mode variable. The super blocks are inactive otherwise.
Model Variants
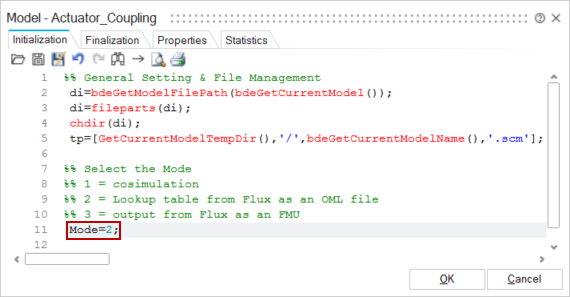
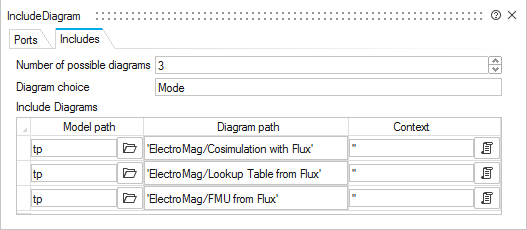
Co-Simulation Method
In the super block Cosimulation with Flux, the Flux block performs the co-simulation by reading in the coupling component that was generated using the Flux 2D transient application file MultiPhysics.F2STA.
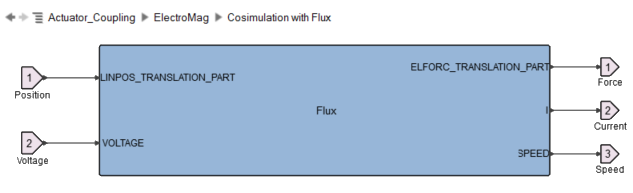
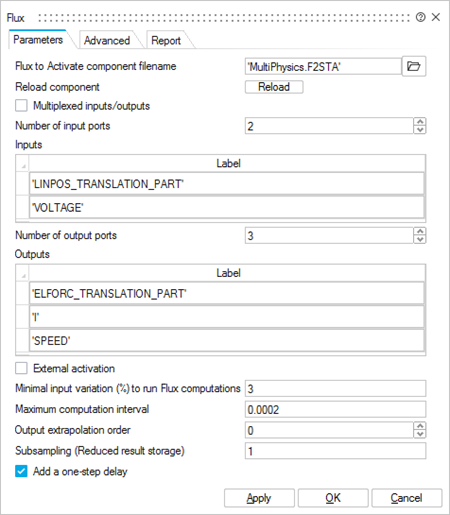
Look-Up Table Method
The super block
includes a context to read in the results exported from a magnetostatics simulation in Flux.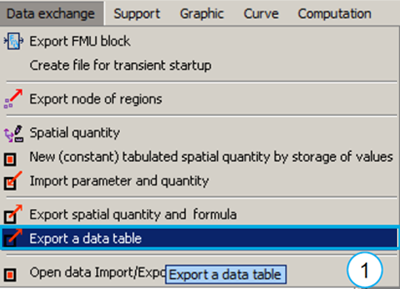
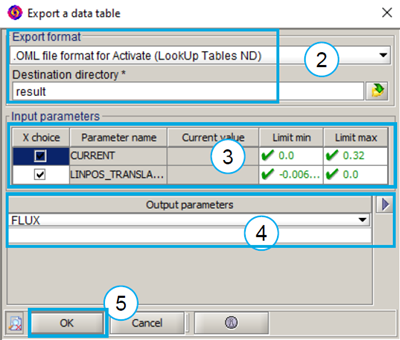
The Flux results are exported as two .oml files FLUX.oml and FORCE.oml. These files are available in the Flux project folder and are directly read in from the Twin Activate model. In the following image, the super block Lookup Table from Flux includes the yellow blocks LookupTableND and LookupTableND_1 which load FLUX.oml and FORCE.oml respectively.
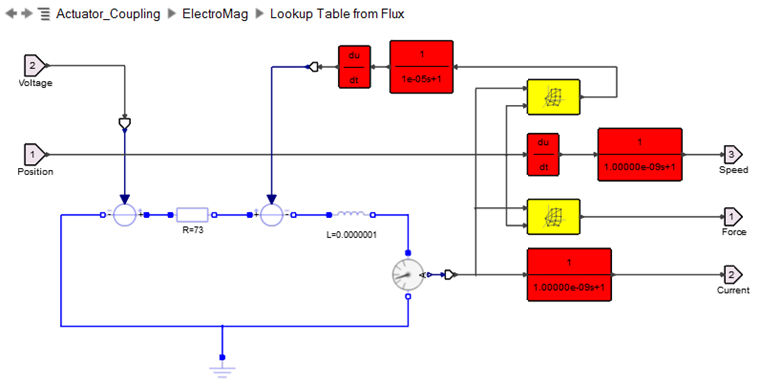
The context of this diagram includes the directions for the FLUX.oml and FORCE.oml files to be read into the super block.
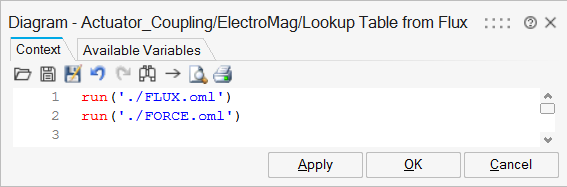
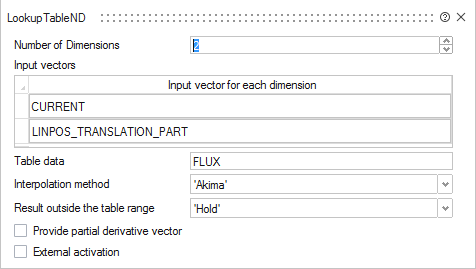
FMU Method
The super block
includes a context to read in the results exported from a Flux 2D magnetostatics simulation.The Flux results are exported as two .fmu files: FLUX.fmu and FORCE.fmu. The steps in Flux to export the .fmu files are indicated in the following dialogs:
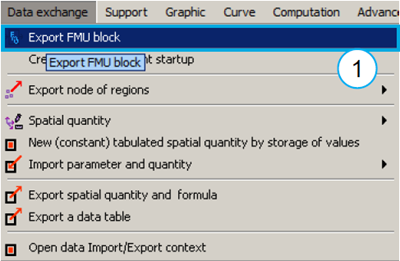
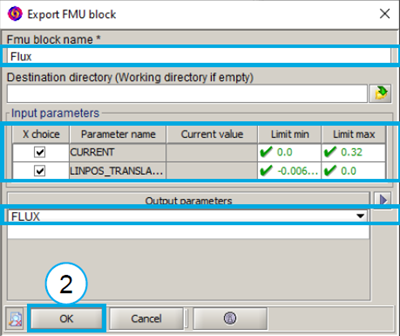
The .fmu files are available in the Flux project folder and are directly read in from the Twin Activate model. In the super block FMU from Flux, the yellow blocks are FMU and FMU_1 that load FLUX.oml and FORCE.oml respectively.
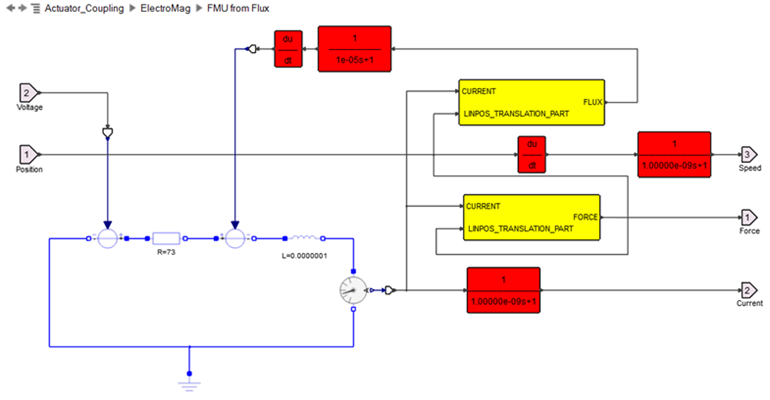
The Functional Mockup Interface standard is an important gateway to other products. In this tutorial, the use of either a Lookup Table or an FMU are almost identical and are meant to illustrate various features of Flux and Twin Activate.
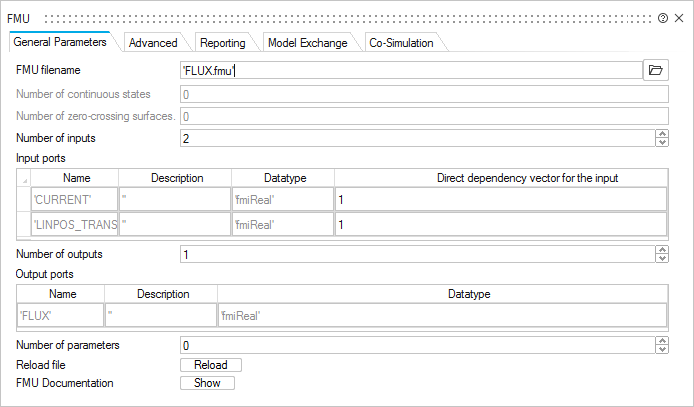
Simulation Results
Mode 1: Co-Simulation Method
With the co-simulation method, a Flux transient (dynamic) analysis is run directly from Twin Activate through the coupling component from Flux. This type of simulation is slow but can account for Eddy current effects in massive iron conductors. The added value of the Flux-Twin Activate co-simulation coupling is the accuracy of the results with the inclusion of the Eddy currents. In this case, the type of kinematics in the mechanical rotor is multiphysics position. Note that the value of the initial position must be determined in order to obtain the correct results.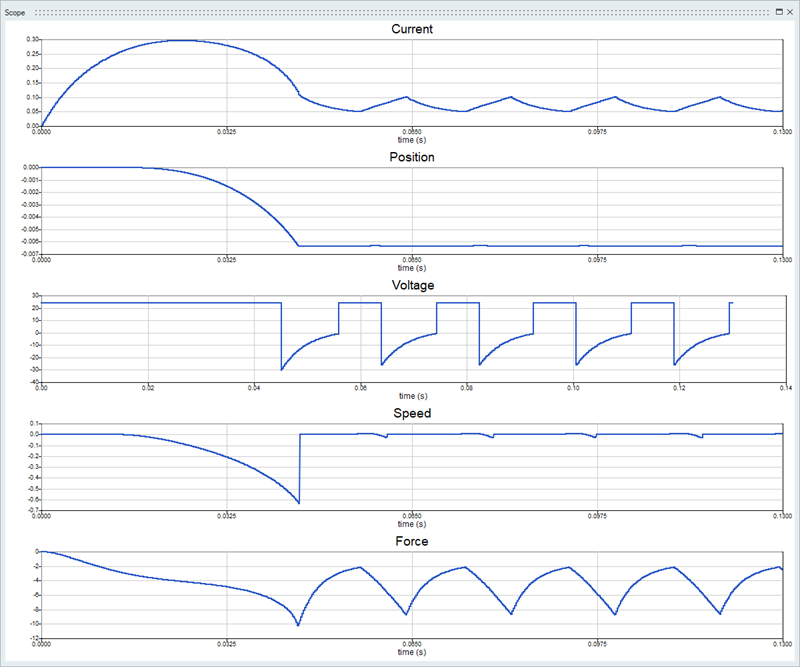
Mode 2: OML Method
The aim of this method is to build an accurate reduced model (based on the Finite Element model) of the linear actuator. Accuracy and quick simulation with Twin Activate are the biggest advantages of this approach. The linear actuator behavior is represented by the flux in the coil and the force which are calculated with a finite element method. First, through the Flux simulation, the response surface of flux and force is computed. In a first approximation, the variation parameters are Current and Position. This response surface is used in Twin Activate.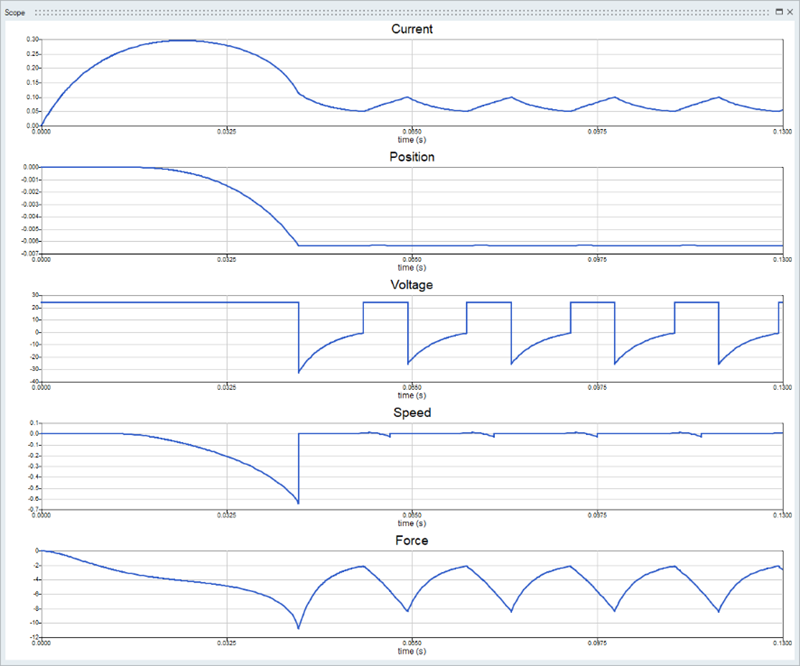
Mode 3: FMU Method
The FMU block enables the import and simulation of an FMU as a Twin Activate block. The FMU can be of type Model-Exchange (ME) or Co-Simulation (CS). Both version 1.0 and 2.0 are supported. Inputs and outputs can be of Real, Integer, Boolean or String data types. Only scalar input and output are supported. The aim of this method is to build an accurate reduced model (based on the Finite Element model) of the linear actuator. Accuracy and quick simulation with Twin Activate are the biggest advantages of this methodology. The linear actuator behavior is represented by Flux in coil and force which are calculated with a finite element method. In Flux, a simulation is run with a finite element method to compute the response surface of the flux and force. In a first approximation, the variation parameters are Current and Position. Once the simulation is finished, an FMU file is generated. This FMU is then used in Twin Activate.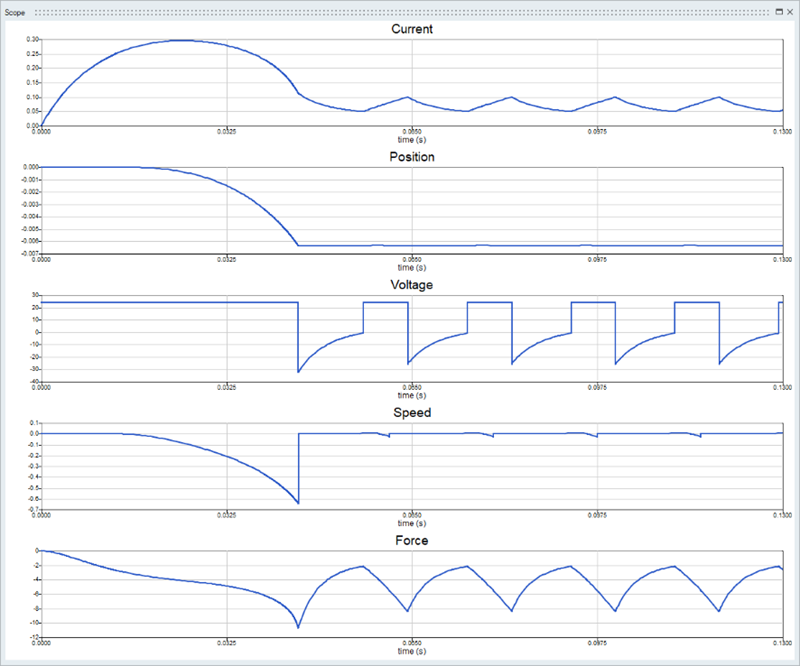
Results Comparison
Aside from the varying peaks between the three methods: co-simulation in blue, OML in red and FMU in turquoise, the results are very similar. The small variance is due to the different interpolation methods applied to run simulations on reduced models for the OML and FMU methods.
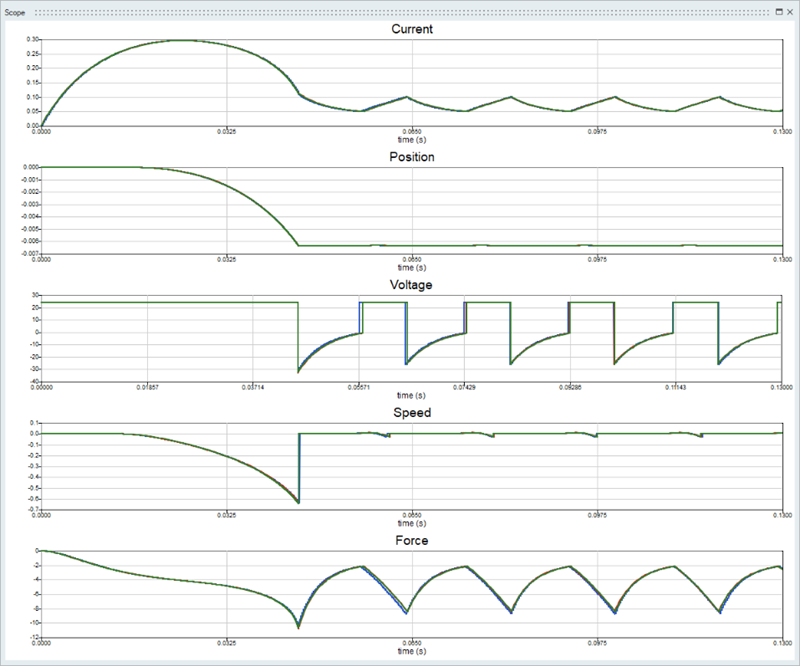