OS-E: 3020 Two-Layer Stamped Control Arm
An automobile control arm is manufactured by using two stamped plates joined at the seam.
Model Files
Model Description
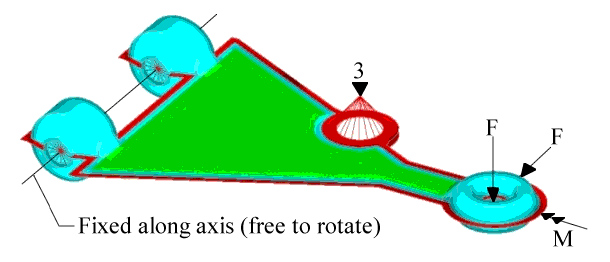
(1) | (2) | (3) | (4) | (5) | (6) | (7) | (8) | (9) | (10) |
---|---|---|---|---|---|---|---|---|---|
DTPG | 2 | DVGRID | 1 | ||||||
+ | 15.0 | 60.0 | YES | ||||||
PATRN | 10 | 4184 | 1211 |
The plane of symmetry is normal to the vertical axis and is positioned running through the center plane of the model.
The optimization objective function is simply defined as minimizing the sum of the weighted compliance of all three load cases.
Results
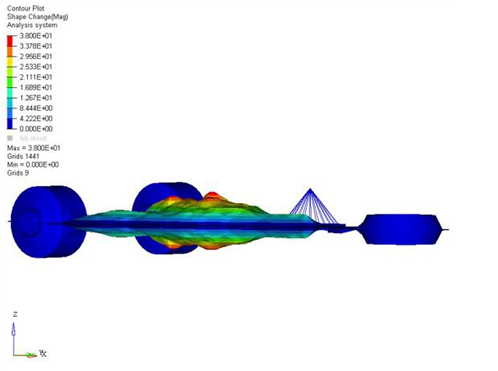
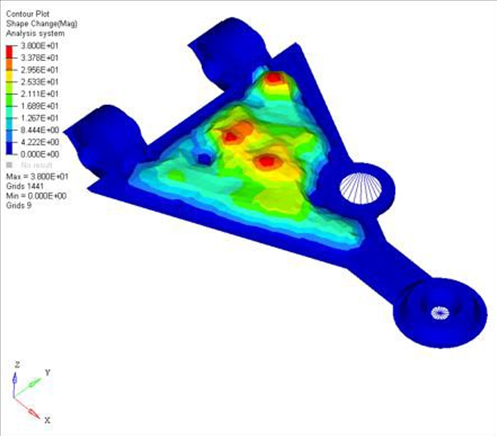
The solution shows the importance of adding vertical bending stiffness in the area around the shock absorber attachment point. OptiStruct creates a large bead running from the upper frame attachment point, past the shock attachment, and up to the spindle attachment (Figure 3).
This bead supports most of the bending load. In addition, there is vertical bending which runs in the perpendicular direction. OptiStruct creates a bead running from the shock attachment point to the lower frame attachment (Figure 3). This second bead is not as pronounced because there is less bending in that direction compared to the primary direction.