ACU-T: 2400 Supersonic Flow in a Converging-Diverging Nozzle
Tutorial Level: Advanced
Prerequisites
Prior to starting this tutorial, you should have already run through the introductory tutorial, ACU-T: 1000 Basic Flow Set Up
Problem Description
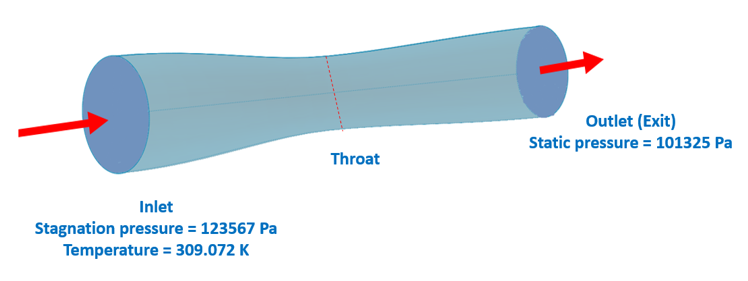
The exit to throat area ratio of the nozzle is 1.5. The radius at the inlet is 0.892 m, while the radius at the outlet is 0.691 m. The inlet stagnation pressure and the inlet temperature are 123,567 Pa and 309.072 K, respectively. The static pressure at the outlet is set to 101,325 Pa. The fluid in this problem is air, where the flow is assumed inviscid (viscosity and conductivity are zero) and density is based on the ideal gas model.
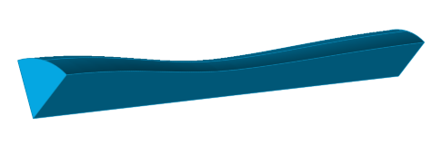
The AcuSolve simulation will be set up to model a transient supersonic flow where the flow variables reach an asymptotic state to determine the stable flow solution.
Start HyperMesh CFD and Open the HyperMesh Database
- Start HyperMesh CFD from the Windows Start menu by clicking .
-
From the Home tools, Files tool group, click the Open Model tool.
Figure 3. The Open File dialog opens. - Browse to the directory where you saved the model file. Select the HyperMesh file ACU-T2400_CD_Nozzle.hm and click Open.
- Click .
-
Create a new directory named CD_Nozzle and navigate into this directory.
This will be the working directory and all the files related to the simulation will be stored in this location.
- Enter CD_Nozzle as the file name for the database, or choose any name of your preference.
- Click Save to create the database.
Validate the Geometry
The Validate tool scans through the entire model, performs checks on the surfaces and solids, and flags any defects in the geometry, such as free edges, closed shells, intersections, duplicates, and slivers.

Set Up Flow
Define Material Properties
-
From the Flow ribbon, click the Material Library tool.
Figure 5. The Material Library dialog opens. - Under Settings, click Ideal Gas, and then click the My Material tab.
-
Click
to add a new ideal gas model.
- Keep the default values for the Gas constant and the Specific heat and set the Viscosity and Conductivity values to 0.
-
Rename the model to Air Ideal Inviscid.
Figure 6.
Set Up the Simulation Parameters and Solver Settings
-
From the Flow ribbon, click the Physics tool.
Figure 7. The Setup dialog opens. -
Under the Physics models setting:
- Select the Supersonic radio button under Single phase flow.
- Set the Ideal gas model to Air Ideal Inviscid.
- Set the Time step size to 0.000125.
- Set the Final time to 0.3125.
- Verify that the Turbulence model is set to Laminar.
Figure 8. - Click the Solver controls setting.
-
Set the Transient update factor to 0.5.
Note: Since we are interested in a solution that reaches a steady state, the transient update factor can be set to a non-zero value without affecting the solution accuracy.
-
Set the Maximum stagger iterations to 5.
Figure 9. - Close the dialog and save the model.
Verify the Material Selection
-
From the Flow ribbon, click the Material tool.
Figure 10. - Verify that the Air Ideal Inviscid material has been assigned to the volume domain.
-
Click
on the guide bar.
Define Flow Boundary Conditions
-
From the Flow ribbon, Pressure
tool group, click the Stagnation Pressure tool.
Figure 11. -
Click on the inlet face highlighted in the figure below.
Figure 12. -
In the microdialog, enter the following values for the
stagnation pressure and temperature.
Figure 13. -
On the guide bar, click
to execute the command and exit the tool.
-
Click the Outlet tool.
Figure 14. -
Select the face highlighted in the figure below, enter the
101325 as the static pressure value, and then click
on the guide bar.
Figure 15. -
Click the Slip tool.
Figure 16. -
Select the face highlighted in the figure below and then click
on the guide bar.
Figure 17. -
Click the
tool.
Figure 18. -
Select the face highlighted below as the Source.
Figure 19. -
Click Target on the guide bar
then select the opposite face.
Figure 20. -
Click
on the guide bar.
Generate the Mesh
-
From the Mesh ribbon, click the
Volume tool.
Figure 21. The Meshing Operations dialog opens.Note: If the model has not been validated, you are prompted to create the simulation model before running the batch mesh. - Check that the Average element size is 0.1 and the Mesh growth rate is 1.3.
-
Accept all other default parameters.
Figure 22. -
Click Mesh.
The Run Status dialog opens. Once the run is complete, the status is updated and you can close the dialog.Tip: Right-click on the mesh job and select View log file to view a summary of the meshing process.
Run AcuSolve
-
From the Solution ribbon, click the Run tool.
Figure 23. - Set the Parallel processing option to Intel MPI.
- Optional: Set the number of processors to 4 or 8 based on availability.
- Expand Default initial conditions and enter the values as shown below.
-
Leave the remaining options as default and click
Run to launch AcuSolve.
Figure 24. The Run Status dialog opens. Once the run is complete, the status is updated and you can close the dialog.Tip: While AcuSolve is running, right-click on the AcuSolve job in the Run Status dialog and select View Log File to monitor the solution process.
Post-Process the Results with HM-CFD Post
In this step, you will check the contours of pressure on a mid slice plane.
- Once the solution is completed, navigate to the Post ribbon.
- From the menu bar, click .
-
Select the AcuSolve log file in your problem
directory to load the results for post-processing.
The solid and all the surfaces are loaded in the Post Browser.
Figure 25. -
Move the animation slider to the end to load the last time step data.
Figure 26. -
Click the Slice Planes tool.
Figure 27. - Select the x-y plane in the modeling window.
-
In the slice plane microdialog, click
to create the slice plane.
- In the display properties microdialog, set the display to pressure and activate the Legend toggle.
-
Click
and set the Legend location to Upper Center, the Legend Orientation to Horizontal, and the Colormap name to Rainbow Uniform.
Figure 28. -
Click
on the guide bar.
-
In the Post Browser, hide the Flow
Boundaries surfaces to display the pressure contours on the
slice plane.
Figure 29. Similarly, you can display the Mach number contour.Figure 30.