Material Manager
In Flow Simulator, use the Material Manager option to define a default material for models, either by selecting from the predefined lists or by creating materials. This eliminates the need to select a material through the Property Editor.
All the materials in the Material Manager can be defined as DEFAULT, and can be edited and removed using Apply, Edit, and Remove.
Set a Material as a Default
Materials are grouped under five types: Gas, Liquid, Solid, Emulsion Mixture, and Super-Critical Multiphase. If the default material is listed under any of these groups, click the name of the material to assign DEFAULT to it.
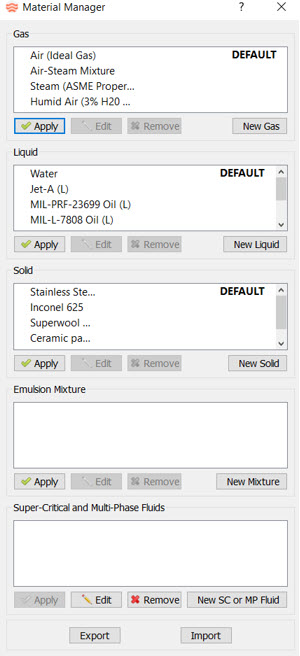
Define New Material in Gas, Liquid, or Solid Phase
- New Gas if the material is gas
- New Liquid if the material is liquid
- New Solid if the material is solid
- New Mixture if the material is emulsion mixture, and so on.
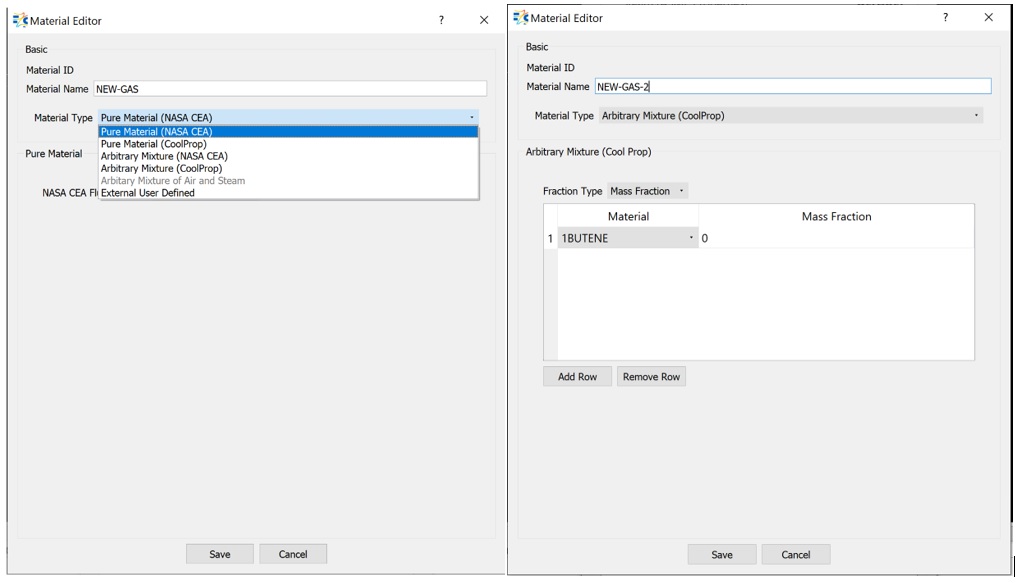
In the New Gas and New Liquid menus, many materials are listed under the following headings:
- Pure Material (NASA CEA)
- Pure Material (CoolProp)
- Arbitrary Mixture (NASA CEA)
- Arbitrary Mixture (CoolProp)
- Pure Incompressible Material (CoolProp)
- Mass Based Incompressible Material (CoolProp)
Select one of these materials, and all fluid and thermal properties (density, viscosity, specific heat, conductivity, and so on) are used from the NASA CEA database or from the CoolProp database, based on your selection.
If Arbitrary Mixture is selected, provide the Mass Fraction or Mole Fraction.
Use the External User Defined option to define your own material, with all required fluid properties provided. The Material ID starts with 1000 for External User Defined materials, and both the ID and the given name are printed in the .flo file. Thus, you can distinguish the user-defined materials in the file.
The user-supplied properties include:
GAS PHASE | LIQUID PHASE | SOLID |
---|---|---|
Gas Constant or Density | Density | (*) Density |
Dynamic Viscosity | Dynamic Viscosity | (*) Specific Heat |
Specific Heat or Specific Heats Ratio | Specific Heat or Specific Heats Ratio | Thermal Conductivity |
Thermal Conductivity or Prandtl Number | Thermal Conductivity or Prandtl Number | (*) Surface Emissivity |
(*) Vapor Pressure or Boiling Condensation Point | (*) Vapor Pressure or Boiling Condensation Point | (*) Melting/Freezing Point |
(*) Melting/Freezing Point | ||
(*) these properties are not required; enable them when you want to use them in your analysis. |
- Constant
- Provide a constant value for the property with its value and unit.
-
Figure 3. - 1D-Curve
- Click Define to display the Static Temperature vs “Selected Property” table.
-
Figure 4. Note: Select Add Row and Remove Row as necessary. - 2D-Table
- Provide Static Pressure vs Static Temperature vs “Selected Property” in the following table:
-
Figure 5. - Enter temperatures in the red column, pressure values in the yellow
rows, and enter property values in the remaining rows as shown
above.Note: To add/remove rows and columns, click the PLUS/MINUS signs in the bottom left corner and top right corner, respectively.
- Use Advanced Options to select options to transform and/or interpolate the provided values.
Define a New Mixture
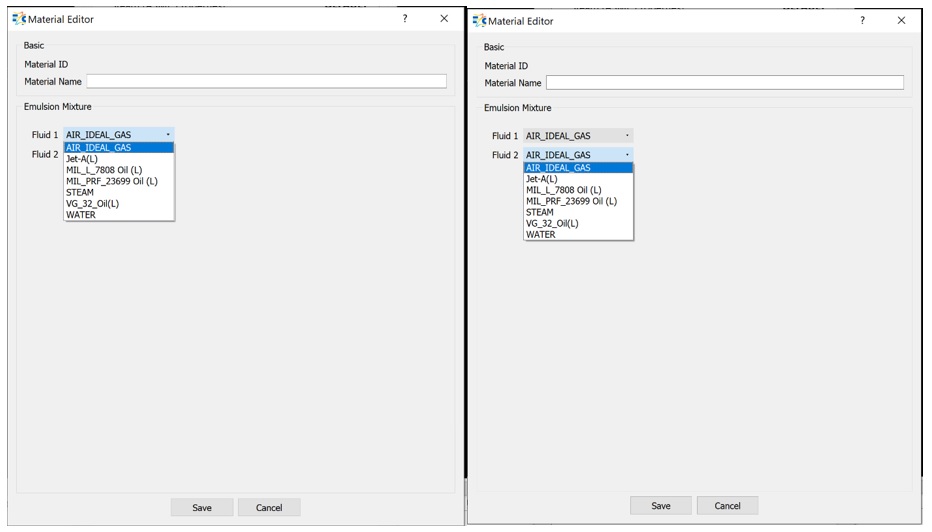
Fluid Property Recommendations
Built-in fluids, such as Air (Ideal Gas), Water, Jet-A (L), and so on, are the fastest source of properties.
NASA-CEA is a good source for gas properties and is typically used for modeling combustion. The gas mixtures from NASA-CEA are more robust than the mixtures from Coolprop. NASA-CEA uses the ideal gas assumption so pressures and temperatures are in the appropriate range.
Coolprop must be used if the fluid is expected to change phase (gas-liquid) or is in the super critical range. Coolprop is a good choice for models using refrigerants or super critical fluids (CO2 or H2). Coolprop does not use the ideal gas assumption, and the compressibility factor, z, from Coolprop is used to modify the Flow Simulator equations that are based on the ideal gas equation for density.
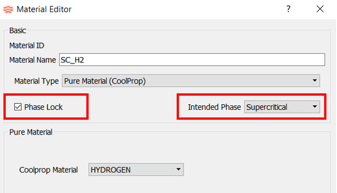
Import/Export Material Property
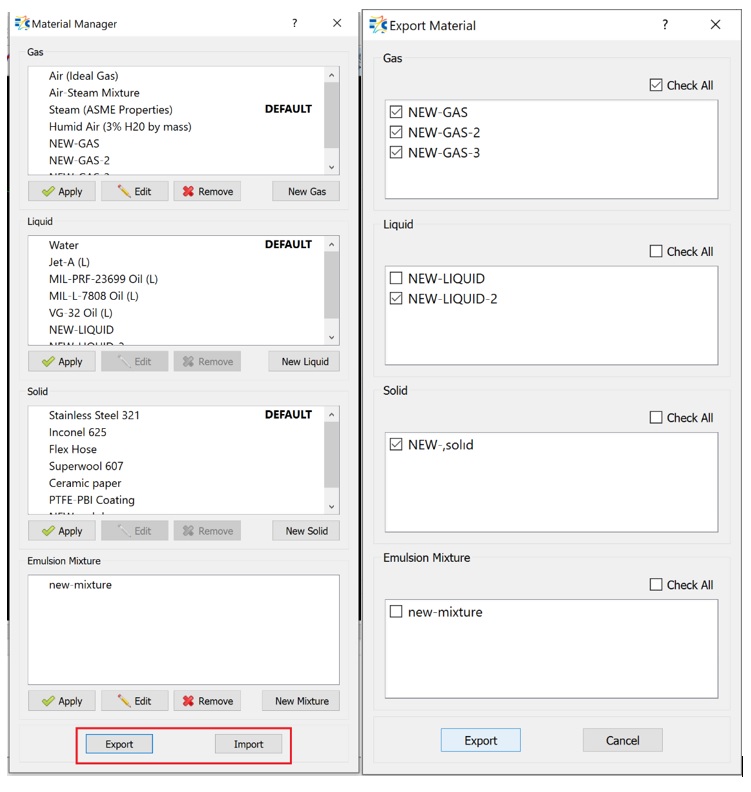
- Check All
- Exports all materials under that phase.