ACU-T: 5000 Centrifugal Air Blower with Moving Reference Frame (Steady)
Tutorial Level: Beginner
Prerequisites
Prior to starting this tutorial, you should have already run through the introductory tutorial, ACU-T: 1000 UI Introduction, and have a basic understanding of HyperMesh CFD and AcuSolve. To run this simulation, you will need access to a licensed version of HyperMesh CFD and AcuSolve.
Problem Description
The problem to be addressed in this tutorial is shown schematically in Figure 1 and Figure 2. It consists of a centrifugal blower with a wheel of forward curved blades, and a housing with inlet and outlet ducts. The fluid through the inlet plane enters the hub of the blade wheel, radially accelerates due to centrifugal force as it flows over the blades, and then exits the blower housing through the outlet plane. Because they're relatively cheaper and simpler than axial fans, centrifugal blowers have been widely used in HVAC (heating, ventilating, and air conditioning) systems of buildings.
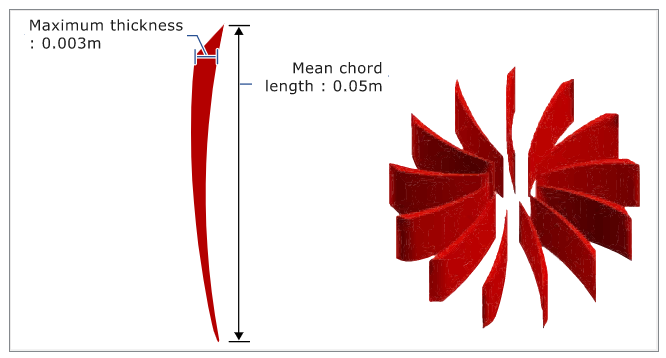
The boundary condition at the inlet is taken as stagnation pressure rather than mass flow rate so that AcuSolve calculates pressure rise based on impeller rotation.
The fluid in this problem is air, which has a density (ρ) of 1.225 kg/m3 and a viscosity (μ) of 1.781 x 10-5 kg/m-sec.
Start HyperMesh CFD and Open the HyperMesh Database
- Start HyperMesh CFD from the Windows Start menu by clicking .
-
From the Home tools, Files tool group, click the Open Model tool.
Figure 3.
The Open File dialog opens. - Browse to the directory where you saved the model file. Select the HyperMesh file ACU-T5000_BlowerSteady.hm and click Open.
- Click .
-
Create a new directory named CentrifugalBlower and navigate into this directory.
This will be the working directory and all the files related to the simulation will be stored in this location.
- Enter Blower_Steady as the file name for the database, or choose any name of your preference.
- Click Save to create the database.
Validate the Geometry
The Validate tool scans through the entire model, performs checks on the surfaces and solids, and flags any defects in the geometry, such as free edges, closed shells, intersections, duplicates, and slivers.

Set Up the Problem
Set Up the Simulation Parameters and Solver Settings
-
From the Flow ribbon, click the Physics tool.
Figure 5.
The Setup dialog opens. -
Under the Physics models setting:
Figure 6.
-
Click the Solver controls setting and verify that the
parameters are set as shown in the figure below.
Figure 7.
- Close the dialog and save the model.
Assign Material Properties
-
From the Flow ribbon, click the Material tool.
Figure 8.
-
Using window selection, draw a box around the entire model.
Both the centrifugal blower and the housing solids are selected.
Figure 9.
- In the microdialog, click the drop-down menu next to Material and select Air.
-
On the guide bar, click
to execute the command and exit the tool.
Define the Reference Frame
In this step, you will create a rotating reference frame for the fluid in the impeller region so that the elements in those regions are solved in the given rotating reference frame and rotational body forces are added to that volume set.
-
Hide the housing solid.
- Set the entity selector to Solids.
- Select the centrifugal housing.
- Right-click and select Hide form the context menu or press H.
Only the solid for the centrifugal blower displays in the modeling window.Figure 10.
-
From the Flow ribbon, click the Reference Frame tool.
Figure 11.
- Make sure the Include bounding surfaces option is active on the guide bar.
-
Select the solid in the modeling window.
Bounding surfaces are automatically selected.
- On the guide bar, click Axis.
-
Define the axis of rotation.
-
On the guide bar, click
to execute the command and exit the tool.
- Right-click in the modeling window and select Show All from the context menu or press A to return to the full model display.
Define Flow Boundary Conditions
-
From the Flow ribbon, Pressure
tool group, click the Stagnation Pressure tool.
Figure 14.
-
Click the face of the inlet.
Figure 15.
- In the microdialog, click the Turbulence tab.
- Set the Turbulence input type to Viscosity Ratio.
-
Set the Turbulence viscosity ratio to 10.
Figure 16.
-
Rename the inlet.
- From the legend on the left side of the modeling window, double-click on Stagnation pressure.
- Type Inlet and press Enter.
-
On the guide bar, click
to execute the command and exit the tool.
-
Click the Outlet tool.
Figure 17.
-
Click the face of the outlet.
Figure 18.
-
In the microdialog, make sure both Static pressure and Pressure loss
factor are 0.
Figure 19.
-
On the guide bar, click
to execute the command and exit the tool.
Generate the Mesh
-
From the Mesh ribbon, click the
Volume tool.
Figure 20.
The Meshing Operations dialog opens.Note: If the model has not been validated, you are prompted to create the simulation model before running the batch mesh. - Check that the Average element size is 0.01061.
-
Accept all other default parameters.
Figure 21.
-
Click Mesh.
The Run Status dialog opens. Once the run is complete, the status is updated and you can close the dialog.Tip: Right-click on the mesh job and select View log file to view a summary of the meshing process.
Define a Surface Monitor and Run AcuSolve
- Set the entity selector to Solids.
- Select the centrifugal housing.
-
Right-click and select Hide form the context menu or
press H.
The solid for the centrifugal blower should be displayed in the modeling window
Figure 22.
-
From the Solution ribbon, click the Surfaces tool.
Figure 23.
-
Select the blower interface and verify that the arrow is heading toward the
blower, as shown in figure below.
Figure 24.
-
On the guide bar, click
to execute the command and exit the tool.
- Rename surface_output to blowerInterfaceFront.
-
From the Solution ribbon, click the Run tool.
Figure 25.
The Launch AcuSolve dialog opens. - Set the Parallel processing option to Intel MPI.
- Optional: Set the number of processors to 4 or 8 based on availability.
- Deactivate the Automatically define pressure reference option.
-
Leave the remaining options as default and click
Run to launch AcuSolve.
Figure 26.
Tip: While AcuSolve is running, right-click on the AcuSolve job in the Run Status dialog and select View Log File to monitor the solution process.
Post-Process the Results with HM-CFD Post
Plot Pressure on a Slice Plane
- Navigate to the Post ribbon.
- From the menu bar, click .
-
Select the AcuSolve log file in your problem
directory to load the results for post-processing.
The solid and all the surfaces are loaded in the Post Browser.
-
Click the Slice Planes tool.
Figure 27.
- Select the x-y plane in the modeling window.
-
In the microdialog, click
and move the plane along its normal direction a distance of -0.07.
Figure 28.
- Press Esc to exit the Move tool.
-
In the slice plane microdialog, click
to create the slice plane.
- In the display properties microdialog, toggle the Legend radio button.
-
Click
and set the Colormap Name to Rainbow Uniform.
Figure 29.
-
On the guide bar, click
to execute the command and exit the tool.
-
In the Post Browser, hide all the Parts and Flow
Boundaries.
Figure 30.
Plot Velocity Streamlines
- Hide the slice plane and show the Inlet and Outlet boundaries in the Post Browser.
-
Click the
tool.
Figure 31.
- Select the x-y plane in the modeling window.
-
In the microdialog, click
and move the plane along its normal direction a distance of -0.07.
Figure 32.
- Press Esc to exit the Move tool.
-
In the slice plane microdialog, click
and set the circle radius to 0.1.
- On the guide bar, click Seeds.
- In the microdialog, set the Generation method to Uniform and set the Point count to 100.
-
Click Calculate.
Figure 33.
- In the display properties microdialog, set the Display to Velocity and set the Colormap Name to Rainbow Uniform.
-
On the guide bar, click
to execute the command and exit the tool.
- In the Post Browser, show the Auto boundary condition, then right-click on Auto and select Edit.
- In the microdialog, adjust the transparency slider until you can see the velocity streamlines.
-
Click
on the guide bar.
Figure 34.
Summary
In this tutorial, you successfully learned how to set up a steady state simulation involving a rotating reference frame in a centrifugal blower. You started by importing the mesh and then once the case was set up, you generated a solution using AcuSolve. Then, you created a contour plot for pressure and velocity streamlines using HyperMesh CFD post.