Find Evaluation Positions
The main objective of this function is to find the evaluation locations or positions for each of the 1D weld elements. The evaluation positions vary for each weld type.
Evaldist
value is used
to find the evaluation positions.The following inputs are required to determine the evaluation positions:
- Evaluation distance
- Weld width factor
- Shell thickness
- Direction vectors for the 1D elements
The calculations to arrive at the evaluations positions for the different types of welds are shown below.
For T and L Welds
- Evaluation Distance
Evaldist = Standard distance from the specification
- Weld Width
Weldwidth = Weld Width Factor * Min Shell Thickness
- Evaluation Position from Weld Element Centroid
(Thickness / 2.0) + Evaldist + Weldwidth
For B and O Welds
- Evaluation Distance
Evaldist = Standard distance from the specification
- Weld Width
Weldwidth = Weld Width Factor * Min Shell Thickness
- Evaluation Position from Weld Element Centroid
Evaldist + Weldwidth
Using this relative evaluation distance and the centroid data of the 1D element, the absolute coordinates of the evaluation positions are determined.
For each of these evaluation positions, the nearest shell element and the closest node of the shell element are determined. These entities will be used to get the stress results.
Evaluation Method
Selection of Evaluation Method, Nominal or Hotspot, calculates evaluation distance with one or two points. Nominal or Hotspot method is regulation independent and can be applied to any regulation (Specification Context) or weldline (Points Context).
Applying Evaluation Method in Specification context, assigns the selected Method, Nominal/ Hotspot, to each weldline in Points context.
Evaluation Distance with 1 Point

Auto evaluation distance calculation
Example: T weld
Method: Auto
L1 = (Shell Thickness / 2.0) + Evaldist 1 + Weldwidth
where,
- Evaldist1
Constant1 * Min Shell Thickness
- Weld Width
Weld Width Factor * Min Shell Thickness
- Stress
- Stress is queried from Element at L1
Evaluation Distance with 2 Points

Auto evaluation distance calculation
Example: T weld
Method: Auto
L1 = (Shell Thickness / 2.0) + Evaldist 1 + Weldwidth
L2 = (Shell Thickness / 2.0) + Evaldist 2 + Weldwidth
where,
- Evaldist 1
Constant1 * Min Shell Thickness
- Evaldist 2
Constant2 * Min Shell Thickness
- Weld Width
Weld Width Factor * Min Shell Thickness
- Extrapolated Stress
Constant2 (Stress at L1) - Constant1 (Stress at L2)
- Stress at L1
- Stress is queried from Element at L1
- Stress at L2
- Stress is queried from Element at L2
- For Manual Distance, L1 and L2 is directly specified by the user.
- When evaluating with element data, the stress is taken from the closest element centroid. This is not necessarily matching the exact evaluation distance.
- For an evaluation of solid welds, an evaluation distance with two points is supported for DVS1608, DVS1612, EuroCode 3, and FKM only.
- The Evaluation distance L1 is bound by the maximum search distance (set in preference). I.e., the default maximum search distance should be reviewed and increased if the required evaluation distance is greater than the assigned evaluation distance.
Evaluation Distance with Corner Data
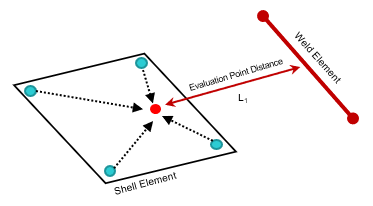
Evaluation Distance per Component
Nominal and Hotspot evaluation distances are exposed for each weld direction/component in Points Context. Stress query for Transverse, Longitudinal and Shear will be based on the total distance calculated from the evaluation distance formulae listed for 1 Point or 2 Point approach.