Seam Weld Fatigue Analysis
Seam Weld Fatigue analysis is available to facilitate Fatigue analysis for seam welded structures. It allows you to simulate the Fatigue failure at the seam weld joints to assess the corresponding fatigue failure characteristics like Damage and Life.
The Volvo method implemented in HyperLife is based on a research paper Fatigue Life Prediction of MAG-Welded Thin-Sheet Structures published by M. Fermér, M Andréasson, and B Frodin. The method is a hot spot stress approach applicable to thin metal sheets. Hot spot stress is calculated from grid point forces at weld line. The method showed a good agreement with laboratory test results for sheet thickness between 1.0 mm and 3.0 mm. The method typically requires two SN curves. One is a bending SN curve which is dominated by bending stress, and the other is a membrane SN curve which dominated by membrane stress.
Implementation
Modeling Requirements
- Weld sections to be analyzed for seam weld fatigue should be meshed with CQUAD4 elements whenever possible. CTRIA3 elements may be used for corner weld if inevitable and for closing the end of weld line, if necessary. Other element types are currently not supported for seam weld fatigue.
- The weld should be modeled by a single or double row of CQUAD4 elements. If a 2 sided fillet is to be modeled, a third row of CQUAD4 may be used.
- The thickness of the weld element is the same as the effective throat.
- The mesh size around the weld should be as regular as possible. Although this method is less sensitive to mesh size, a mesh size of about 10 mm would be a good choice according to Fermér, Andréasson, Frodin. This paper showed that large hot spot stress differences did not exist between mesh size 12 mm and mesh size 5 mm in case of a regular mesh.
- The weld element can be referenced through Sets/Parts. Custom Zones assist in creating user-defined sets in HyperLife.
- The weld element normal direction should point outwards such that the normal direction is toward the weld toe, not toward the weld root. The normal direction of weld element plays a critical role in determining the weld toe and the surface to be examined on the base of the weld.
Weld Basics
- Face
- Toes
- Throat
- Root
- Legs
Good Weld Design Practice
This section provides a basic overview of stress concentrations in welded structures and a few recommendations for good weld design. This section should not be considered as a complete weld design guide and does not cover an exhaustive list of weld design recommendations.
- Weld shape-based stress concentration:Figure 2 shows the stress concentration at the toe of a weld. Its magnitude depends on the flank angle, , local weld toe radius, r, and plate thickness, t. The concept of a weld reinforcement is a misnomer as you can see that the stress concentration actually increases with increasing weld metal, that is, an increase in flank angle, .
Figure 2. Stress Concentration versus Weld Radius and Plate Thickness for Seam Weld Fatigue
- Weld design-based stress concentration:
The second stress concentration comes from the joint design. Stress concentrations arise whenever there is a change in stiffness in the structure. It can result from either an increase of decrease in stiffness. For example, a hole in a plate will have about the same stress concentration as a rigid boss added to the plate. Here are some examples of weld joints contrasting good and poor design practice.
First you need to consider a cover plate welded to a bending beam. A large stress concentration exists at the end of the cover plate because of the large change in stiffness. A better design is shown on the right side where there is a more gradual change in stiffness.Figure 3. (a) Incorrect Weld Design; (b) Correct Weld Design: Gradual Stiffness Gradient
A second source of stress concentration is unintentional bending stresses caused by asymmetric geometries. The design on the left will have larger bending stresses than the double lap joint on the right side.Figure 4. (a) Incorrect Weld Design; (b) Correct Weld Design: Double Lap Joint Symmetric Geometry
Welding plates of differing thicknesses or widths is always problematic. Just as above, the easiest geometry to weld has the largest stress concentration. You should always consider moving the welds to lower stress areas in the structure and have a gradual transition in stiffness such as the joint shown Figure 5(b).Figure 5. (a) Incorrect Weld Design; (b) Correct Weld Design: Gradual Stiffness Transition
Supported Weld Types
HyperLife supports certain types of welds for Seam Weld Fatigue Analysis.
- Only one row of elements can be defined for the weld face elements or either of the weld legs.
- The damage calculation locations are automatically chosen based on the weld type (as explained in Fillet). With the exception of the throat damage location, both the root and toe damage locations are evaluated based on the grid point forces and subsequent stresses induced in the corresponding elements adjacent to the weld elements. For throat damage, the weld element grid point forces, and subsequent stresses are directly considered.
- HyperLife currently supports the following weld types.
Fillet
HyperLife evaluates failures at root and toe when a weld element is CQUAD4. If CTRIA3 is used for a weld element, only toe is evaluated.
T-joint
- One-sided One RowFor a One-sided One Row T-joint, the weld element normal direction should point towards the weld toe. The nodes of the weld element are in line with the weld toes. The length should be determined by the actual dimensions of the weld element (typically L=T1+T2).
Figure 7. Representation of a One-sided T-Joint Fillet Weld with One Row of CQUAD4 Elements
The thickness of the weld element is the effective weld throat (typically it is equal to L/1.414).
- One-sided Two RowMultiple rows are recommended for welds where the weld penetration is high and the weld typically forms the basis for contact between the two plates. Such welds are more rigid compared to welds where the penetration is lower, thereby additional rows of weld shell elements are required to capture the behavior. In Figure 8, the weld has penetrated more than the weld in Figure 7. For a One-sided Two Row T-joint, the two weld element normal directions should point towards the weld toe. The length should be determined by the actual dimensions of the weld element (typically L=T1+T2).
Figure 8. Representation of a One-Sided T-Joint Fillet Weld with Two Rows of CQUAD4 Elements
The thickness of the weld element is recommended to be set equal to 0.35*L.
- Two-sided Two RowFor a Two-sided Two Row T-joint, the weld element normal directions should point towards the corresponding weld toe. The nodes of the weld elements are in line with the corresponding weld toes. The length should be determined by the actual dimensions of the weld element (typically L=T1+T2).
Figure 9. Representation of Two-Sided T-Joint Fillet Weld with Two Rows of CQUAD4 Elements
The thickness of the weld element is the effective individual weld throat (typically it is equal to 1.414*L).
- Two-sided Three RowMultiple rows are recommended for welds where the weld penetration is high and the weld typically forms the basis for contact between the two plates. Such welds are more rigid compared to welds where the penetration is lower, thereby additional rows of weld shell elements are required to capture the behavior. In Figure 10, the welds have penetrated more than the welds in Figure 9. For a Two-sided Three Row T-joint, the two weld element normal directions should point towards the corresponding weld toe. The weld element normal for the central vertical element can point to either weld toe.
Figure 10. Representation of a Two-sided T-Joint Fillet Weld with Three Rows of CQUAD4 Elements
Cross-joint
- One-sided One RowFor a One-sided One Row Cross-joint, the weld element normal direction should point towards the corresponding weld toe.
Figure 11. Representation of a One-sided Cross-Joint Fillet Weld with One Row of CQUAD4 Elements Each
- One-sided Two Row
Multiple rows are recommended for welds where the weld penetration is high and the weld typically forms the basis for contact between the two plates. Such welds are more rigid compared to welds where the penetration is lower, thereby additional rows of weld shell elements are required to capture the behavior. In Figure 12, the welds have penetrated more than the welds in Figure 11. For a One-sided Two Row Cross-joint, the weld element normal direction should point towards the corresponding weld toe. The vertical weld element normals should also point towards the corresponding weld toe.
Figure 12. Representation of a One-sided Cross-Joint Fillet Weld with Two rows of CQUAD4 Elements Each
- Two-sided Two RowFor a Two-sided Two Row Cross-Joint, the weld element normal direction should point towards the corresponding weld toe.
Figure 13. Representation of a Two-sided Cross-Joint Fillet Weld with Two Rows of CQUAD4 Elements Each
- Two-sided Three Row
Multiple rows are recommended for welds where the weld penetration is high and the weld typically forms the basis for contact between the two plates. Such welds are more rigid compared to welds where the penetration is lower, thereby additional rows of weld shell elements are required to capture the behavior. In Figure 14, the welds have penetrated more than the welds in Figure 12.
For a Two-sided Three Row Cross-Joint, the weld element normal direction should point towards the corresponding weld toe. The normals of the vertical weld elements can point towards either weld toe on each side.Figure 14. Representation of a Two-sided Cross-Joint Fillet Weld with Three Rows of CQUAD4 Elements Each
Overlap or Laser Edge Overlap
Meshing rules are the same as that for fillet weld. Normal direction of weld element should be toward weld toe. Weld nodes should be along the line of the weld toe. Weld element thickness should be effective weld throat. In laser weld, failure at weld throat is evaluated as well as weld toe and weld root.
Two Row Overlap
Multiple rows are recommended for welds where the weld penetration is high and the weld typically forms the basis for contact between the two plates. Such welds are more rigid compared to welds where the penetration is lower, thereby additional rows of weld shell elements are required to capture the behavior. The typical length of the weld element is L=T1+T2.
One Row Overlap or One Row Laser Edge Overlap
One Row Overlap or One Row Laser Edge Overlap (Alternative)
Laser Overlap
Failure Evaluation
Failure evaluation points differ from one weld type to another.
Fillet
Overlap
Laser Overlap
Laser Edge Overlap
Note the surface where weld throat is evaluated. This surface is determined by normal direction of the weld element.
Hot Spot Stress
HyperLife calculates hot spot stress based on grid point force of a toe/root element.
In the original approach suggested by Fermér, Andréasson, Frodin, grid point forces contributed to the element of interest were directly used without any "adjustment". Later research [P. Fransson and G. Pettersson, 2000] showed that averaging grid point forces made grid point forces less mesh sensitive.
- HyperLife identifies potential damage locations at weld toe, weld root, weld throat and their evaluation surface from weld elements location and its normal direction (as shown in previous sections).
- For the corresponding root and toe damage locations (in adjacent elements),
and in the throat (in the weld element), local coordinate systems are
constructed. The local X axis is constructed in the direction perpendicular
to and away from the corresponding weld element face at the center of the
adjacent element on the weld line (the X axis is in located in the plane of
the adjacent element). The local Y axis is constructed perpendicular to this
X axis in the plane of the adjacent element.
Figure 28. Seam Weld Stress Calculation Example
- Grid point forces are calculated at grids (Q and R) of the adjacent element
(2) along the weld line. Grid point force contributions are sourced from
elements attached (1 and 3) to the adjacent element.
Grid point forces are calculated as:
Moments are written as:
- At each node (
and
) of the adjacent element that lies on the
weld line, averaged grid point forces/moments weighted by length of the
adjacent element and the attached element on the weld toe line are
calculated.
Weighted forces are written as:
Weighted moments are written as:
- Line Forces and Moments are calculated based on the weighted grid point
forces and moments. These line forces and moments from both ends of the
adjacent element on the weld line are averaged to generate the line force
and moment at the midpoint (
).
Line Forces are calculated as:
Line Moments are calculated as:
The averaged line forces and moments at the midpoint, , for element 2 are:
- The line force and moment at the midpoint are then resolved in the local coordinate system constructed in step 2 to generate and respectively. This force and moment pair leads to tensile and bending stresses in the adjacent element with respect to the weld line. These are the forces that are used to calculate stresses.
- Stresses are then calculated normal to the weld line for the adjacent
element from this force moment pair. Stresses are calculated for both top
and bottom of the shell element, and depending on the type of weld, either
one or both are used for fatigue calculations. This is the final hot spot
stress used in further S-N Fatigue Damage Evaluation. For addition
information, refer to Stress-Life (S-N) Approach.
Fatigue Properties
There are a few fatigue properties relevant to Seam Weld Fatigue Analysis that allow you to control the fatigue behavior.
Bending Ratio
The upper and lower curves are referred to as Bending SN curve and Membrane SN curve, respectively. It is recommended that membrane SN curve should be used when membrane stress dominates in an element, and bending SN curve should be used when bending stress dominates. Interpolation between the two curves may be carried out depending on the degree of bending dominance.
Degree of bending dominance can be determined by the average bending ratio ( ). First, the bending ratio ( ) is defined as:
- Maximum bending stress equal to
- Maximum membrane stress equal to
The average bending ratio ( ) for an element is defined as:
- Square of the maximum stress at the top surface of shell element at which the damage is calculated (that is, root, toe, or throat shell elements)
- Bending ratio of shell element .
is the
An interpolation factor ( ) is now defined as:
when
when
The value is defined by the BRATIO field in the Assign Material dialog. It is set to 0.5 by default. If average bending ratio ( ) is less than or equal to the critical bending ratio ( ), then the Membrane SN curve is used to assess damage. If average bending ratio is greater than the critical bending ratio, then an SN curve that is interpolated between membrane SN curve and the bending SN curve is used. The value of the interpolation factor ( ) is used in the linear interpolation method as illustrated in Figure 30. For example, if you consider the Fatigue Strength coefficient value (SR1_i) for the interpolated curve, the calculation is performed as:
Thickness Correction
The thickness correction process is for size effect correction. SN curves are based on test results from a particular size of the specimen. In reality, the stress versus life curve may vary depending on specimen size. Therefore, thickness correction parameters can be used to correct for this effect. It may be applied based on the thickness of each shell element under consideration for Fatigue calculation (that is, toe, root, or throat element). The calculations are:
If , then there is no Thickness Correction.
If , HyperLife increases stress based on HyperLife:
This results in fatigue life reduction, making the design more conservative. TREF and TREF_N can be defined via the corresponding fields in the Assign Material dialog. The default values are 25 and 0.2 respectively. The defaults are in mm.
Thickness Correction can be turned on or off using the corresponding Thickness Correction field in the Fatigue Module dialog for Seam Weld Fatigue Analysis.
Mean Stress Correction
FKM mean stress correction is supported for Seam Weld Fatigue. Stress sensitivity can be defined in the Fatigue Module dialog via the FKMMSS field. Mean stress correction for Seam Weld fatigue can be enabled through the Seam Weld Fatigue Module dialog.
For more information on FKM mean stress correction, see the FKM section under Uniaxial S-N Fatigue.
Input/Output
To activate Seam Weld Fatigue Analysis, the Welds icon from the Fatigue Modules should be selected.

Fatigue Elements
Currently, shell elements (preferably CQUAD4) are supported for the seam weld calculations
Fatigue Parameters
The Method, FE Model Units, Mean Stress Correction, Certainty of Survival, and Thickness Correction are defined though the Seam Weld Fatigue dialog.
For more information on FKM mean stress correction, see the FKM section under Uniaxial S-N Fatigue.
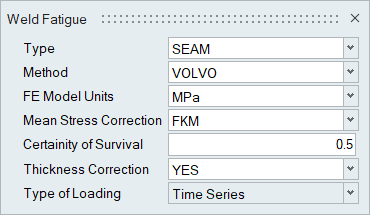
Fatigue Material
- The Material tool assists in assigning material properties to parts/sets and defining the SN curve.
- User-defined materials can be created or selected from
the SN material database.
Figure 33.
- BRATIO
- Critical bending ratio
- TREF
- Reference thickness for thickness effect consideration
- TREF_N
- Exponent for the thickness effect consideration
Fatigue Loads
- Load histories (channels) can be imported, or Block sequence loading can be created.
- Events define the pairing of FEA subcases and load histories.
- Time series, transient, modal superposition and random response fatigue events are supported in LoadMap for seam weld fatigue analysis.
- Random response fatigue supports fatigue events created with Frequency response subcases and Input PSD in loadmap.
Output
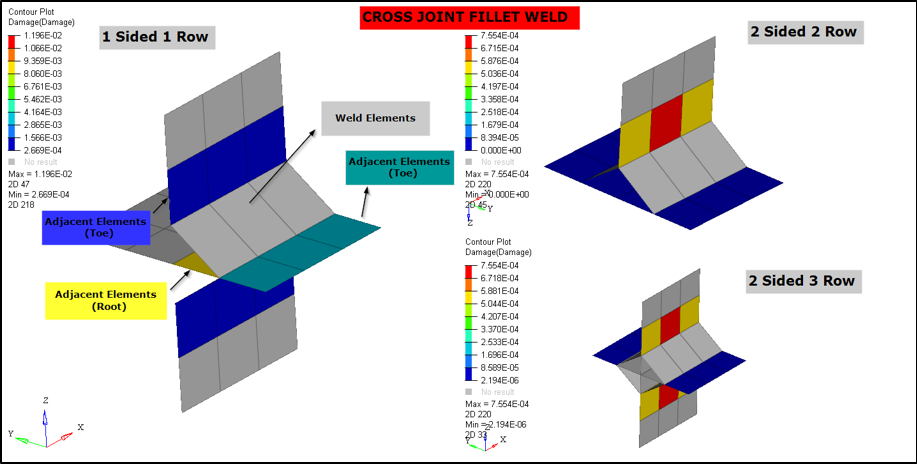
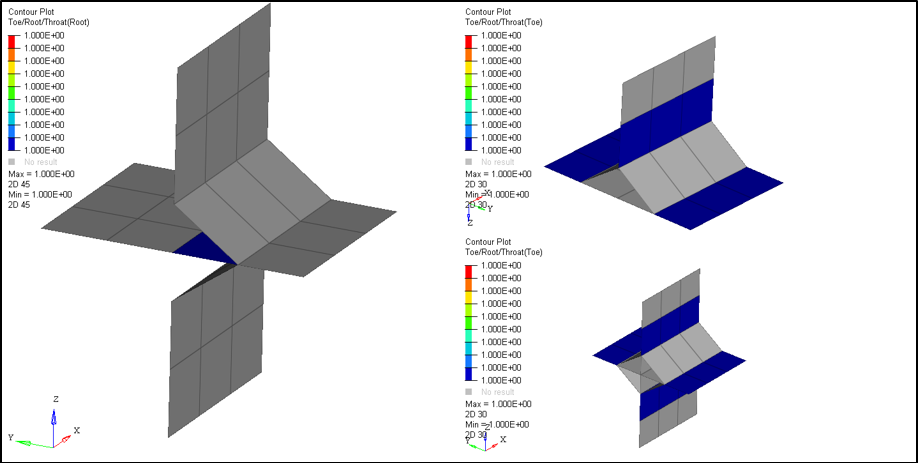