OS-E: 8010 Rubber Ring Crush
This example is a simulation of a rubber ring being crushed in OptiStruct with hyperelastic material and contacts.
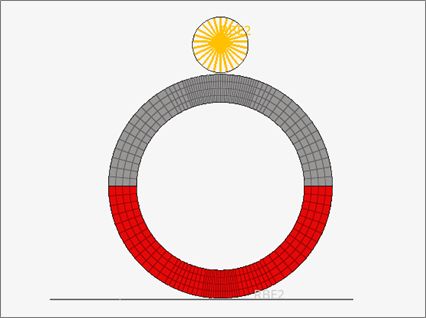
Model Files
Model Description
There is a flat, rigid surface on which a deformed rubber ring rests. On top of the ring rests another circular rigid roller that contacts the ring just slightly. The model has three possible contact interfaces, all of which are Auto Contacts, making it much easier to define contacts. Enforced displacement is applied at the center of the RBE2 of the rigid roller. The roller pushes down the rubber ring enough to produce contact on the inside surface of the ring. This analysis is performed using OptiStruct’s Explicit via ANALYSIS = NLEXPL.
- Young's Modulus
- 600 GPa
- Poisson's Ratio
- 0.3
- Density
- 0.0001 kg/mm3
- Poisson's Ratio
- 0.495
- Material Model
- 0.0001 kg/mm3
The hyperelastic material constants are obtained by conducting curve fitting with the provided TAB1 (simple tension/compression), TAB2 (biaxial tension), and TAB4 (shear) data for rubber material in the MATHE entry, during the OptiStruct run.
Results
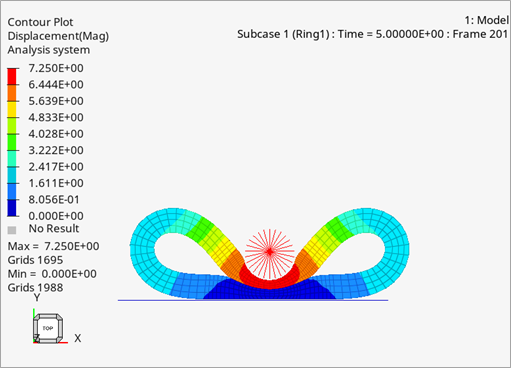