What is Inspire Friction Stir Welding?
Inspire Friction Stir Welding offers an analysis tool for virtual testing, validation, correction and optimization of friction stir welding designs.
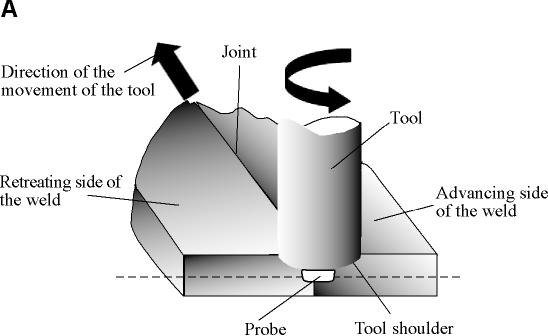
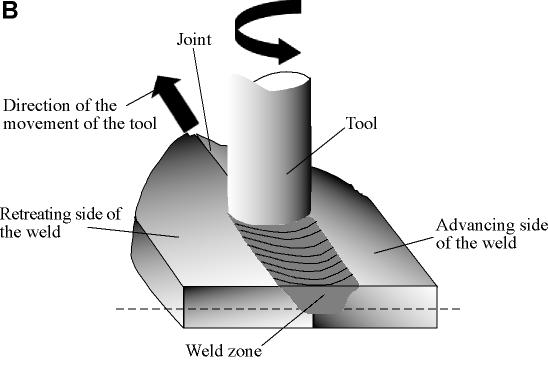
Stages of FSW Process
There are three distinct stages in the process.
- Piercing of the tool
- Tool rotation and translation to create the solid-state weld
- Withdrawal of the tool
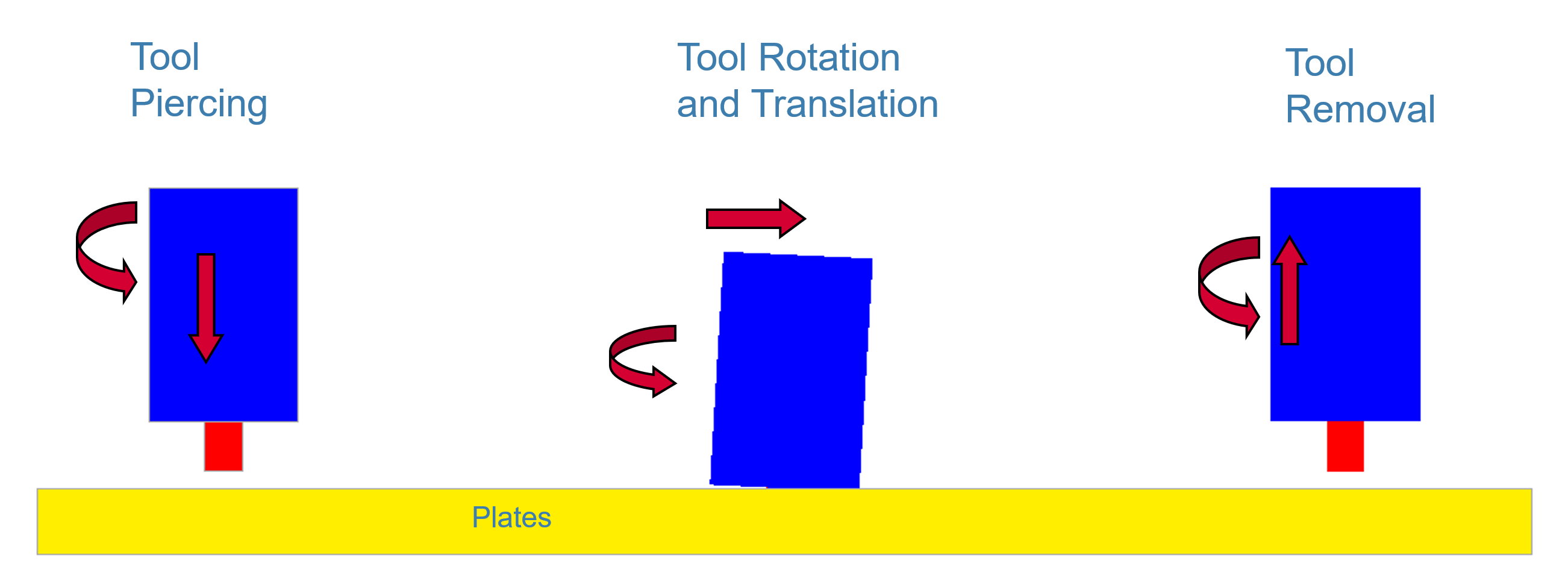
These three stages make this a transient process. The rotating tool is initially plunged into the joint until the shoulder contacts the workpiece. This is called piercing. Then it traverses along the contact line where the two parts are being welded together. Finally, it is removed away from the plates and this stage is called withdrawal. The pin may be tilted at an angle and it can also be threaded. The frictional heat generated by the rotating pin softens the alloys of the welded plates and mixes them together through viscoplastic deformation. This welding happens much below the melting temperature of the alloy. For example, aluminum alloys melt around 625-650 deg C and the joining is achieved with the alloys in the range of 400-450 deg C.
Advantages of FSW Process
- It is a solid-state joining process and does not require melting.
- It can be used to weld dissimilar alloys. (Inspire FSW does not support this feature.)
- Welded plates have high tensile, fatigue, and bend properties.
- The welding process requires minimal preparation work.
- This process does not use filler material or shielding gas. Hence, there are no fumes, etc.
Process Conditions and Parameters
- FSW is used to weld plates with thickness ranging from 2 mm to 20 mm. If larger plates are welded, specialized equipment may be required. Solver has no restriction and will allow any plate thickness.
- Pins to weld aluminum alloys can be made with H13 steel or its variations. To weld steel plates, higher strength pins such as titanium pins will be needed. Typical pin rotational speeds can range from 500 RPM to 4000 RPM, and the pin traversing speed can range from 2 mm/s to 25 mm/s.
- Pins can be cylindrical or conical in shape. In addition, they can be threaded.