OS-E: 3005 Eigenvalue Maximization
An irregularly shaped plate is optimized to increase its natural frequencies.
Model Files
Model Description
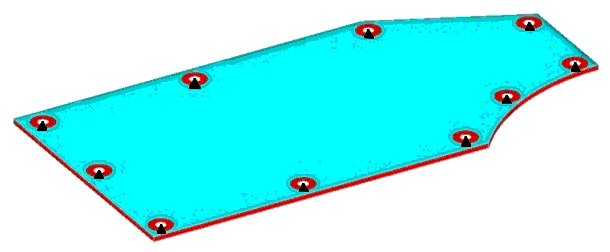
Figure 1. Cover Plate Model with Constraints Shown
(1) | (2) | (3) | (4) | (5) | (6) | (7) | (8) | (9) | (10) |
---|---|---|---|---|---|---|---|---|---|
DTPG | 1 | PSHELL | 5 | ||||||
20.0 | 60.0 | YES | 20.0 | NORM | NONE |
- DESOBJ(MIN)
- 1
- DESSUB
- 101
DRESP1 | 11 | freq1 | FREQ | 1 | |||
DRESP1 | 12 | freq2 | FREQ | 2 | |||
DRESP1 | 13 | freq3 | FREQ | 3 | |||
DRESP1 | 1 | wfreq | WFREQ | ||||
DCONSTR | 101 | 11 | 400.0 | ||||
DCONSTR | 101 | 12 | 500.0 | ||||
DCONSTR | 101 | 13 | 600.0 | ||||
DRESP2 | 1 | wfreq | 900 |
Results
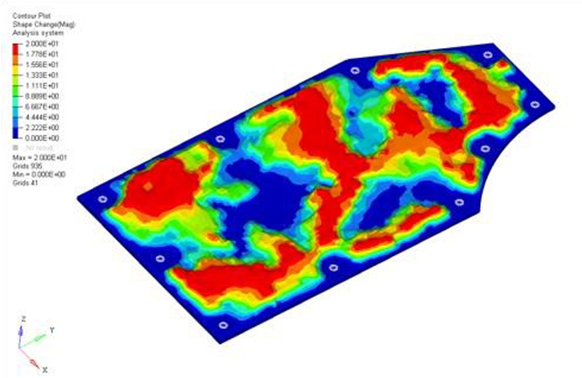
Figure 2. Solution for Plate with Draw Height Equal to 20mm
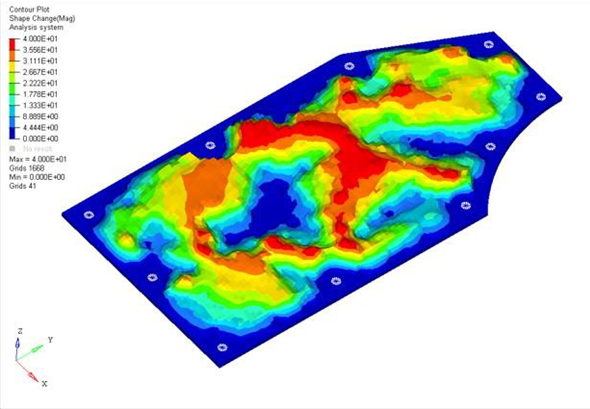
Figure 3. Solution for Plate with Draw Height Equal to 40mm
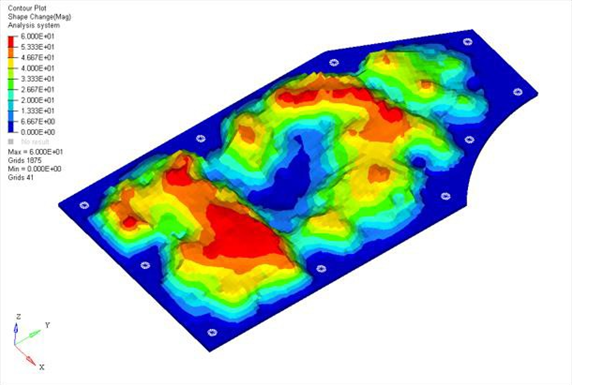
Figure 4. Solution for Plate with Draw Height Equal to 60mm
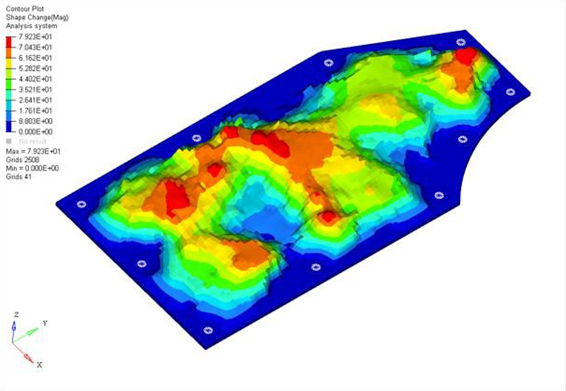
Figure 5. Solution for Plate with Draw Height Equal to 80mm
The reinforcement patterns have a similar shape, but runs with a higher maximum draw height use more levels of draws throughout the plate. All of the solutions made good engineering sense, connecting the weak areas of the plate with beads running primarily across the short span of the plate. These beads were fluidly connected across the long span of the plate allowing the beads to reinforce each other.