AlignedJournalBearing
Model ElementSpecifies a journal bearing that can overtake radial loads.
Class Name
AlignedJournalBearing
Description
The AlignedJournalBearing is a combination of a force element and optionally, a planar or inplane joint. The force element is a function of bearing dimensions, relative radial displacement, and velocity, as well as rotational velocity between the inner journal and outer bearing. The force can act only radially between the inner journal and outer bearing and does not account for tilting and axial misalignment.
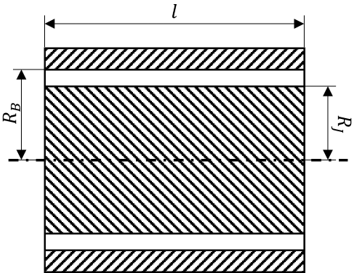
Attributes
The table below summarizes the attributes of the AlignedJournalBearing classes.
Variable | Type | Notes | Symbol |
---|---|---|---|
id | Int() | Unique identification number. | |
label | Str() | Descriptor of the journal bearing element. | |
rm | Reference("Marker", required=True) | Reference marker for the journal bearing element. Forces and states are calculated with respect to this marker. The z-axis of the marker must be parallel to the journal bearing’s axial axis. The marker has to be attached to the gearbox housing. |
|
mu | Double(required=True) | The dynamic viscosity of the lubricant. | |
width | Double(required=True) | The width of the journal bearing. | l |
rj | Double(required=True) | The radius of the journal (inner cylinder). | RJ |
rb | Double(required=True) | The radius of the bearing (outer cylinder). | RB |
journal | Reference(“Part", required=True) | The part that acts as the journal. | |
bearing | Reference(“Part", required=True) | The part that acts as the bearing. | |
output_rm | Reference("Marker") | Defines the reference marker where the output results are
written. By default, output_rm is equal to rm. |
|
method | Enum( “sommerfeld_short sommerfeld_long gumbel_short gumbel_long dynamic_gumbel_short dynamic_gumbel_long ”) |
The methodology (mathematical equation) used to define the hydrodynamic forces. | |
internal_connection_type | Enum(
“NONE INPLANE PLANAR”, Default=”INPLANE”) |
The type of joint/jprim used to constrain the journal and the bearing together, so the 2D representation is applied correctly. The bearing methodology only calculates the radial forces between the journal and the bearing. | |
lubrication_force_graphics | Bool(False) | A Boolean flag that creates 3D lubrication force vectors at discrete points around the journal circumference. | |
force_graphics_scale | Double(1) | A scaling factor for the visualization of lubrication forces. | |
nr | Int(20) | The number of radial steps along the journal circumference used for the lubrication force vectors, the Max/Min Pressure, and the Min Oil Film Thickness requests. | |
na | Int(7) | The number of axial steps along the journal axis used for the lubrication force vectors, the Max/Min Pressure, and the Min Oil Film Thickness requests. | |
contact | Bool(True) | A Boolean flag that enables the IMPACT contact element between the journal and bearing cylinder graphics. | |
contact_stiffness | Double(1000) | Stiffness property of the IMPACT contact element. | |
contact_damping | Double(0.1) | Damping property of the IMPACT contact element. | |
contact_exponent | Double(2.1) | Exponent property of the IMPACT contact element. | |
contact_dmax | Double(0.1) | dmax property of the IMPACT contact element. |
Example
jb = AlignedJournalBearing(id=1,
label=AlignedJournalBearing,
rm=reference_marker,
mu=0.05 * 1e-6,
width=40,
rj=9.8,
rb=10,
journal=journal_part,
bearing=bearing_part,
output_rm=reference_marker,
method="gumbel_short",
internal_connection_type="PLANAR",
lubrication_force_graphics=True,
force_graphics_scale=10,
nr=20,
na=7,
contact=True,
contact_stiffness=1000,
contact_damping=0.1,
contact_exponent=2.1,
contact_dmax=0.1
)