Extrusion Constraints
By using extrusion manufacturing constraints in topology optimization, constant cross-section designs can be attained for solid models - regardless of the initial mesh, boundary conditions or loads.
In some cases, it is desirable to produce a design characterized by a constant cross-section along a given path, particularly for parts manufactured through an extrusion process.
Extrusion constraints can also be used for the conceptual design study of structures that do not specifically need to be manufactured using an extrusion procedure. Those requirements can be regarded as specific geometric constraints and can be used for any design that desires such characteristics. For instance, it might be desirable to have ribs going through the entire depth of a solid domain.
As with other manufacturing constraints, extrusion constraints can be applied on a component level, and can be defined in conjunction with Minimum Member Size Control using the DTPL card.
Problem Setup
Define the Extrusion Path
In the example above, four grids are used to define the extrusion path (left figure), where the path computed by OptiStruct is inaccurate. To obtain a more accurate approximation, more grids are included in the extrusion path (right figure).
For twisted cross-sections, a secondary extrusion path needs to be defined in a similar manner through the EPATH2 field.
Example: Curved Beam
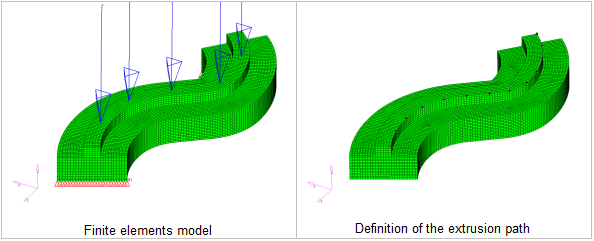
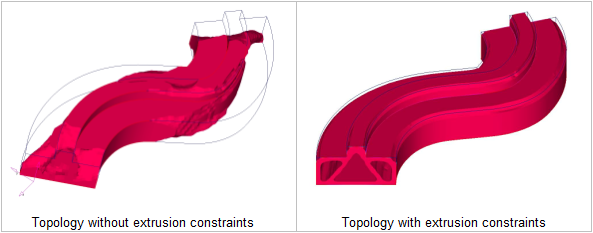
Example: Stair Shaped Structure
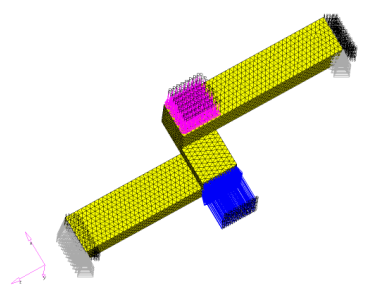
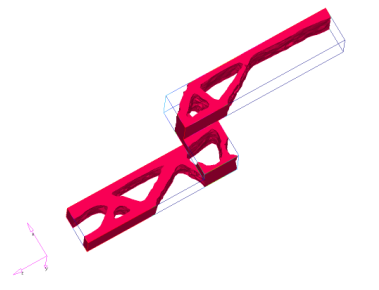
Example: Extrusion Constraints
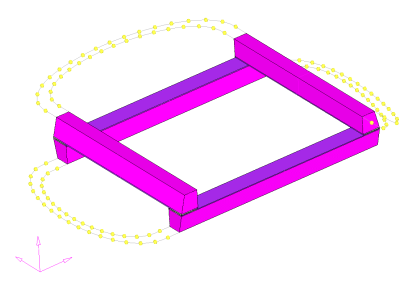
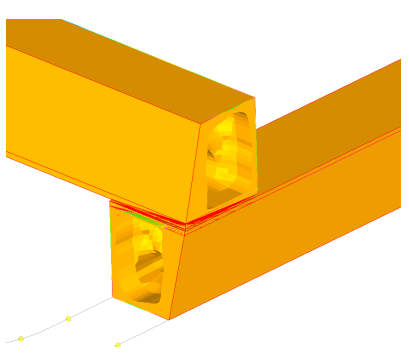